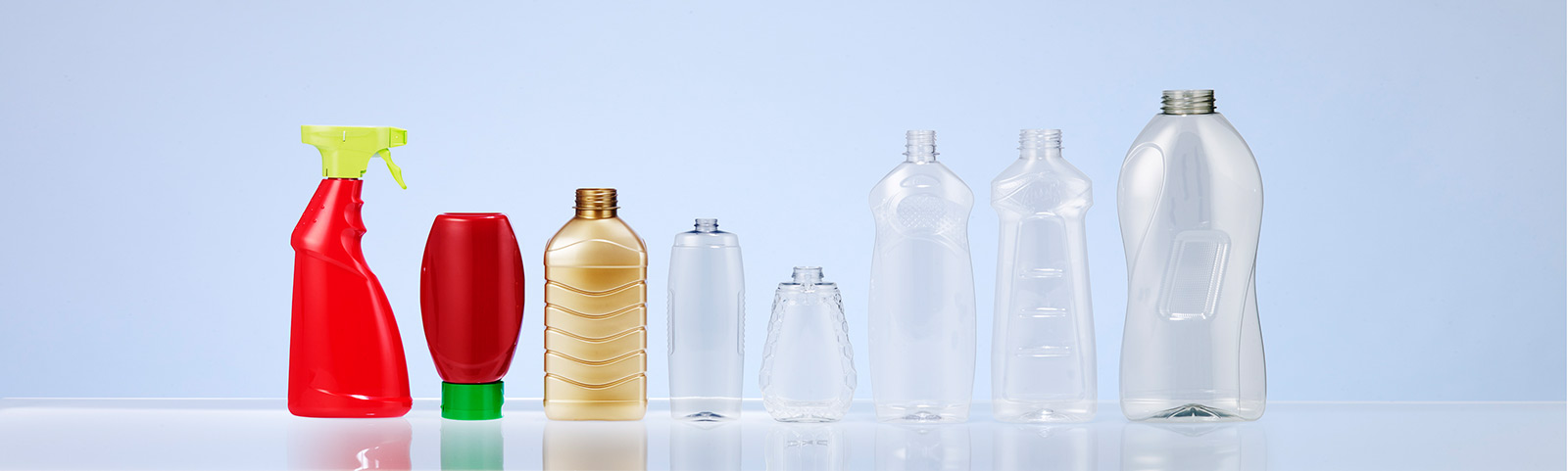
Perfectly formed oval bottles thanks to preferential heating
For lots of stretch blow molders, the oval bottles often used for home and personal care products and food pose something of a challenge during production. This is why we have developed the preferential heating (PH) process, where preforms are selectively heated according to their later bottle shape so that the material is evenly distributed. This means that differences in wall thickness are avoided and the bottle as a whole is more robust.
The stretch blow molders in the KHS InnoPET Blomax series offer one of the most precise and reliable preferential heating technologies on the stretch blow molder market. They produce oval bottles with perfect material distribution that can be several grams lighter than containers manufactured in the standard fashion. This cuts costs and saves on CO2 in the production and logistics processes.
Sustainable bottle production
Other benefits when it comes to sustainability are the machinery’s proven near-infrared radiation or NIR heating technology that operates on shorter wavelengths and is used exclusively by KHS on its rotary stretch blow molders. The effect here is that the heater heats the preforms faster than with the conventional infrared (IR) system. This improves energy efficiency and considerably reduces consumption. The heating segment in the heater is also shorter than that used in IR technology. This in turn affects the machine footprint which is much smaller – but not the quality of the produced containers; even thick-walled or opaque preforms are reliably and accurately prepared for stretch blow molding with this method. What’s known as the CLever-Loc mold shell system also saves time and energy: with the help of a toggle lever only one half of the mold is moved when the blow station is opened and closed, with the other half fixed to the blow wheel. This means that the mold does not have to be locked and unlocked mechanically and either the blowing pressure can be reduced and energy saved or the machine can produce more quickly. The PH method on KHS InnoPET Blomax stretch blow molders thus has one of the largest blow molding processing windows of all of the systems currently available on the market.
At the time of writing, no or only very small amounts of high-quality recyclate for polyethylene (HDPE) and polypropylene (PP) are available on the world market, making the purchase thereof a costly business. By switching from HDPE or PP to PET, beverage producers can use up to 100% recyclate and thus significantly cut the carbon footprint of their packaging material. Bio-based PET can also be processed.
Customers who currently buy in ready-made containers decrease their logistics overheads by changing to production on site – and as a result reduce their carbon footprint in the long term. In principle, in-house production also enables lighter containers to be manufactured as these are subjected to less mechanical stress prior to filling and capping than bottles made externally.
Cost efficiency thanks to clever heating
Less material means fewer consumables in the filling and packaging process and a drop in CO2 emissions: with lighter containers, energy can be saved in the heating process and less compressed air is required. As opposed to the manufacture of standard containers, a smaller compressor unit that is less expensive to procure can also often be used.
The InnoPET Blomax PH is also compelling regarding its lower costs for maintenance and wear and spare parts compared to the mechanically more complex machines on the market. The optional hollow stretch rods also help operators to cut down on their expenditure as the internal cooling of the bottle base increases the output per station, meaning that a smaller machine can manage the same capacity.
Another cost benefit is that the number of containers rejected because they do not meet specifications is lower as the preferential heater boasts extremely precise alignment (+-5° or optionally +-1.5°).
Perfect presentation of perfect bottles
The machine’s perfect material distribution satisfies the highest demands regarding appearance and product presentation – especially in the personal care and food segments. Sophisticated neck alignments (+-1.5°) – achieved by no other manufacturer and contractually assured by us – are also possible. This allows for special, attractive container/cap combinations that hold plenty of customer appeal. And that’s not all; by heating the preforms differently on both sides in the PH process, highly complex container geometries with concave and convex bottle walls can also be produced.
We would be pleased to develop your new oval bottle system together with you in the space of just a few weeks. We would also be happy to advise you on the benefits of in-house production compared to purchasing ready-made containers and on switching from HDPE or PP to PET or [r]PET. If you already produce oval bottles, we can help you optimize your containers and/or your production setup. Please feel free to contact us!
„With our preferential heating process you manufacture oval containers at top performance with the utmost precision while saving on energy and materials.“
Sebastian Wenderdel
PET packaging expert for food and home & personal care products
Further questions?
sebastian.wenderdel[at]khs.com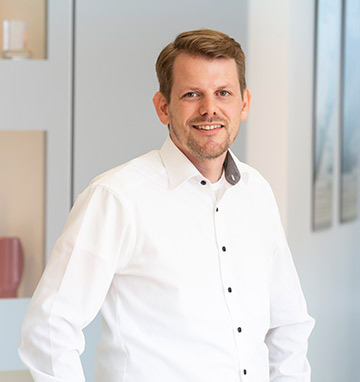