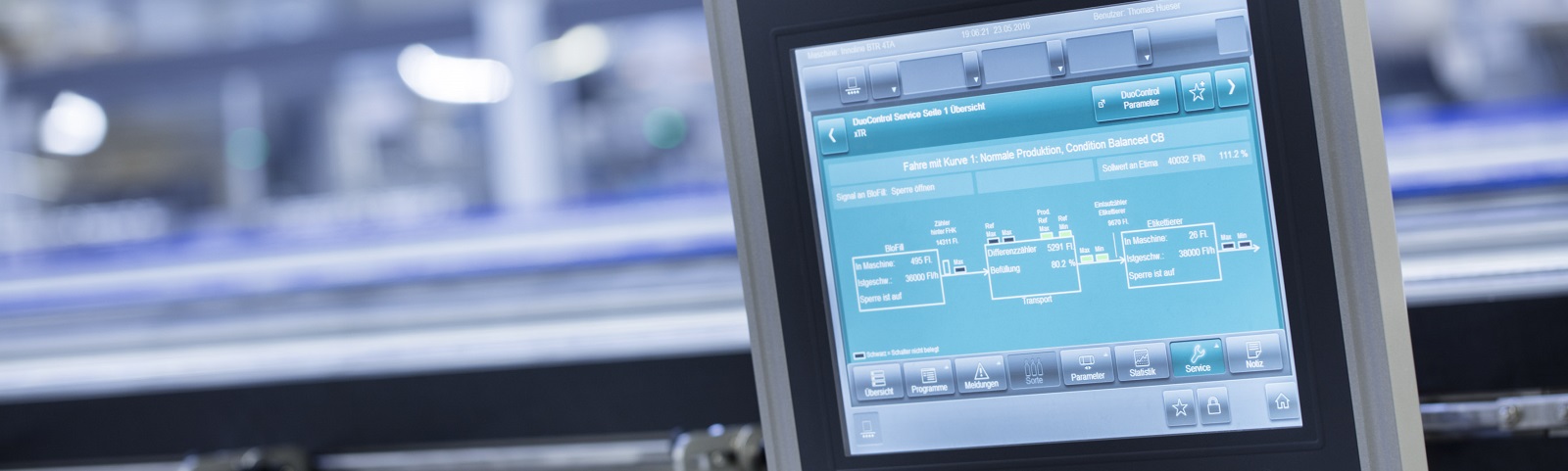
Data interface to remote systems
Reliable connection of your machines to an MES or PDAS
As a beverage manufacturer you face many different challenges. To ensure effective IT support of your internal processes you need process-related manufacturing execution systems (MES) and production data acquisition systems (PDAS) which provide you with key figures and quality data throughout all processes and complete batch tracking. These systems must be connected up to your machines and their various control systems using specifically configured communication interfaces.
To keep configuration and programming effort to a minimum and enable uniform preparation of all of your systems engineers have developed the Weihenstephan standards for production data acquisition in beverage systems. Right from the start KHS played a major role in their planning and conception. These standards define a universal interface used to connect various machine and process controllers to a higher-level IT system and also stipulate what type of industry-specific data must be provided for acquisition. Specifically, this involves the following:
- Physical specification of the interface, i.e. the network and protocols used to connect machines and controllers to an IT system.
- Specification of the interface content, i.e. which data points in which machines and controllers must be provided as a standard and which format and name should be used.
- Data analysis and reporting which provide functions for the calculation of significant and decision-relevant key figures.
- Guidelines for monitoring the interfaces and data contents and instructions which ensure reliable operation and documentation.
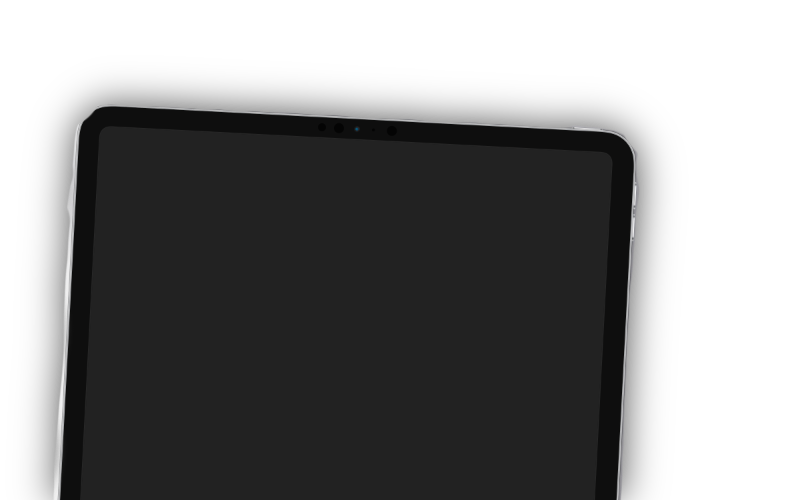
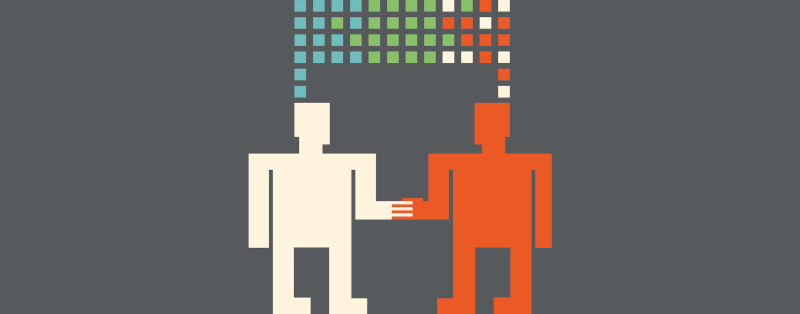
Further reading
Mutual understanding
New standard interfaces ease communication between KHS machines and beverage producers’ MES systems – regardless of the supplier.
Learn moreAt KHS we also attach great importance to the reliable and standardized connection of our machines with their various controllers and devices to an MES or PDAS – whether our own or from a different company.
This allows us to also give you the advantage of having a defined interface with clearly specified responsibilities. With a tool specially designed for this purpose we test the functionality of the communication interfaces during factory acceptance of the machines. Using this tool you can also check whether any faults that might occur are the responsibility of the machine supplier or of the supplier of the connected system.
This gives you a number of other benefits: this standardization means your data acquisition and evaluation is much more detailed and informative; you avoid investment costs, as laborious, cost-intensive individual programming is no longer required; and at the same time you are using the most innovative communication technology. You can rely on us – and that's standard!