SmartCan filler/seamer block by KHS/Ferrum
Hygienic block system for high outputs
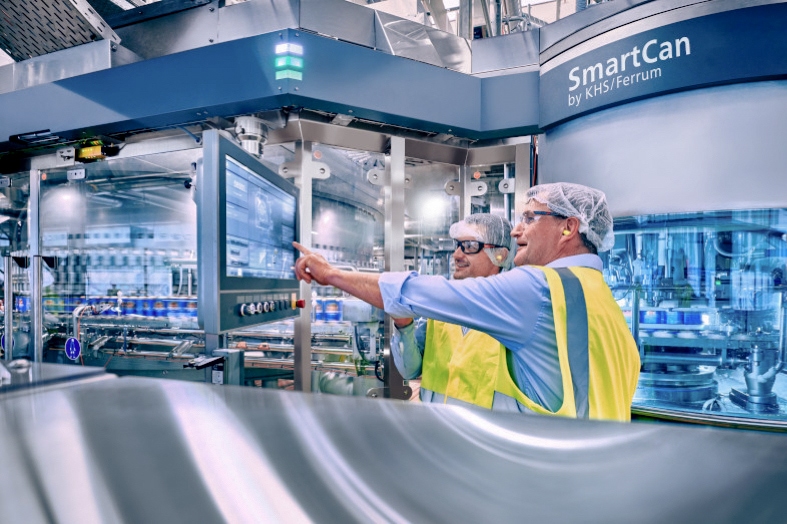
Good to know
Great flexibility, a high standard of hygiene and plenty of future viability all rolled into one: our SmartCan filler/seamer block by KHS/Ferrum combines numerous advantages in a single machine. The filler, seamer and housing are perfectly attuned to one another. The computer-controlled can filler and seamer can fill beer and carbonated soft drinks, juices, still beverages and even coffee and tea quickly and efficiently. The servodrive technology enables automated positioning with a highly accurate degree of reproducibility coupled with a low amount of wear. The can filler/seamer block can process up to 135,000 cans per hour with a diameter of 50 to 73 millimeters and a height of 88 to 200 millimeters.
Well thought out
The high-performance SmartCan filling block by KHS/Ferrum sets new standards in relation to hygiene and product safety. The can seamer and can transfer unit have been developed in accordance with the highest hygiene requirements. This improves access, making the block system very easy to clean. The SmartCan by KHS/Ferrum operates according to the volumetric filling principle: this provides maximum filling accuracy and freedom in the choice of can to be processed. Furthermore, all processes are automated: each process step is documented and can be reproduced at any time. In its first available size the can seamer comes with 14 seaming stations and a capacity of 108,000 cans per hour.
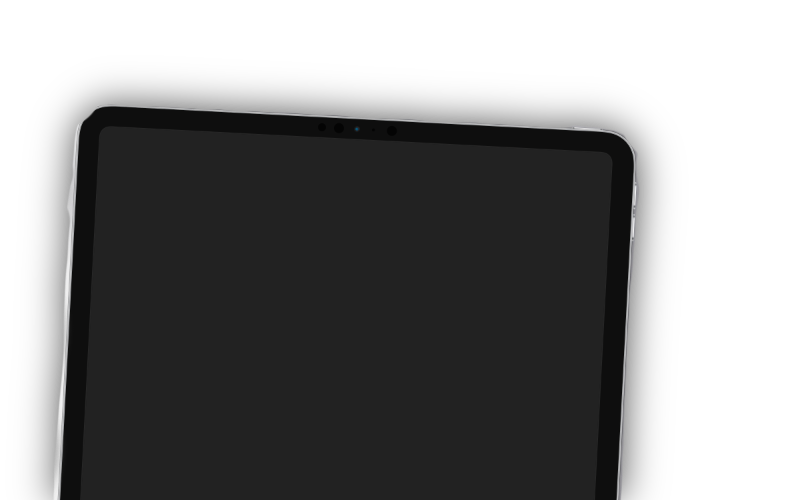
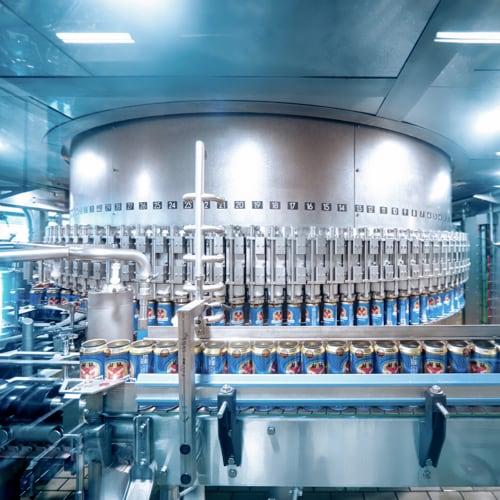
Further reading
Come together
Our high-tech can filler and the powerful Ferrum seamer grow even closer in their combined filler/seamer block.
Learn moreConvincing
- High machine availability thanks to fast format and product changeovers
- Future-proof through the consistent use of servodrive technology, modular software and hardware and intelligent interfaces
- Gentle processing of lightweight beverage cans
Sustainable
- Reduced CO2 consumption with low oxygen pickup
- Lower energy consumption thanks to warm filling at up to 20°C as opposed to the usual recooling
- Hygienic design for simple cleaning operations that save on resources
Good to know: with our platform system you can add modules to your machinery to allow you to flexibly process further beverage types or container sizes in the future. This means that you are all set up to meet constantly changing future market challenges today. Invest in the long term and benefit from efficient maintenance and an optimum supply of spare parts – for increased line availability.
Options
-
Hygiene housing
Brief description: mit hochgezogenen Mantelblechen
Benefits: 40% smaller volume, good access
Convincing: Optimum alignment of the sterile air flow, high standard of hygiene
Sustainable: Fewer FFUs, less cleaning effort thanks to smaller volume and small surfaces
-
Automatic CIP plates
Brief description: Rinsing plates are automatically retracted and extended
Benefits: Fast retraction and extension of the CIP rinsing plates saves time
Convincing: No operator intervention in the hygiene area
Sustainable: Rinsing plates are activated at the press of a button, saving time and resulting in higher availability for production
-
CO2 exhaust
Brief description: CO2 extracted in the service module area and on the seamer
Benefits: Machine safety; low CO2 concentration in the machine environment
Convincing: Safe working conditions
-
Hot filling
Brief description: Hot filling of juice, tea and still beverages
Benefits: Greater flexibility
Convincing: Safe filling of sensitive beverages
Sustainable: Broad filling spectrum on one machine
-
Automatic foam cleaning
Brief description: Automatic SOP cleaning of the outer surfaces within the cladding
Benefits: Fast, automatic cleaning without an operator
Convincing: Reproducible cleaning results as functions monitored
Sustainable: Low media consumption, safe and reliable function