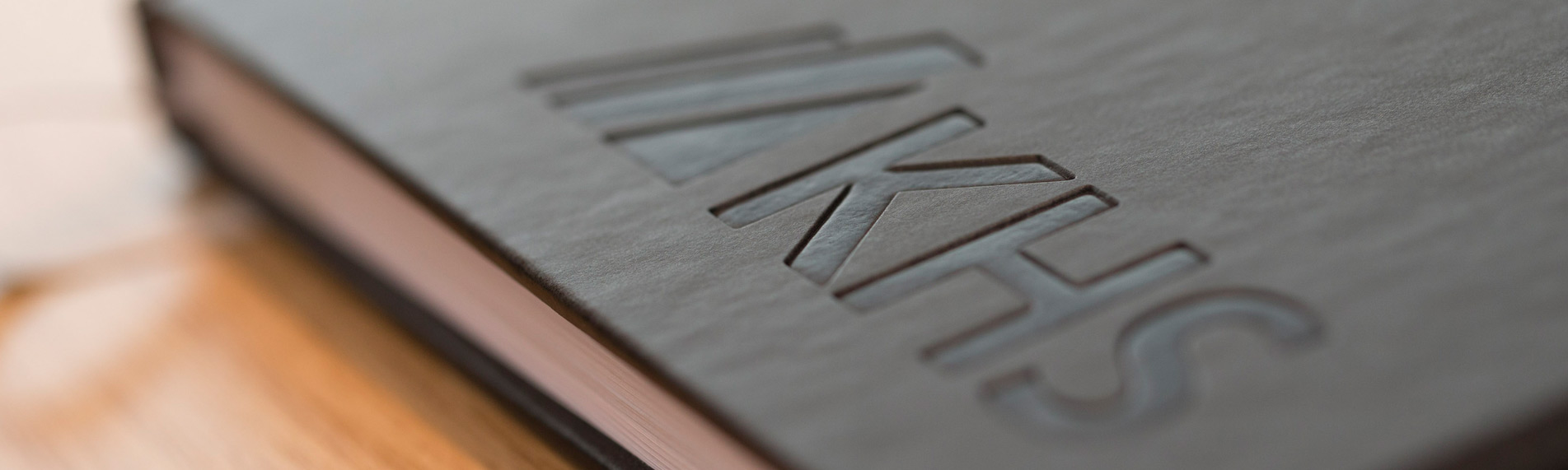
Do it yourself
Carlsberg Bulgaria goes for cutting-edge filling technology
For the first time ever, Carlsberg Bulgaria is canning its beer itself – thanks to the use of proven technology and KHS’ comprehensive service.
The making of beer has tradition here: in 1882, brewer Franz Milde opened what’s now one of Bulgaria’s oldest breweries in the city of Shumen in the east of the country. Nationalized in 1944, Shumensko Pivo, as the company called itself, produced around 350,000 hectoliters of beer per year in the 1960s – in part with the aid of a filling system imported from the former German Democratic Republic. Re-privatized in 1999, Shumensko became part of the Carlsberg Group in 2002 – together with Pirinsko Pivo, which was established in 1967. Based in Blagoevgrad near the border with North Macedonia and Greece, this company was already brewing around 400,000 hectoliters of beer per year by 1980.
More than the sum of its parts
In 2004, the two entities merged under the name of Carlsberg Bulgaria to create one of the country’s leading beverage companies. Today, the two sites jointly fill well over two million hectoliters of beer per year. This output includes the two local traditional beers Pirinsko, the leader on the domestic market, and Shumensko, the country’s third most popular beer. The international portfolio also includes the Danish premium brand Tuborg, Žatecký, which is brewed with Czech hops, as well as 1664 Blanc, Budweiser, Erdinger and Grimbergen, which the company distributes. Somersby Cider and the mixed beer beverage Garage round off the diverse range.
Market leader with great potential
“Today, we’re the leading domestic beer producer in terms of both quantity and value,” says Metodi Stoyanov, integrated supply chain director and the man responsible for local supply chain management and production optimization. “We’re one of the most dynamic and fastest-growing filling companies in our sector.”
The brewery fills more than half of its products into PET bottles and around a quarter into returnable glass bottles. Sales of beverages in cans especially have risen heavily over the past few years. “Cans give consumers one key benefit,” explains Stoyanov. “Unlike returnable glass bottles, they don’t have to be returned to the retailer but can instead simply be recycled through the recycling loop.”
Taken into their own hands
Whereas its filled beer cans were previously imported, Carlsberg has now had its own line in Blagoevgrad for the first time since January 2023. Delivered and installed by KHS, the system has the capacity to fill up to 40,000 500- and 550-milliliter or 60,000 330-milliliter cans per hour. Stoyanov is extremely pleased with the new line. “We need far less room for can filling than we do for filling PET and glass bottles. Given the limited space available to us, that’s one advantage, of course. What’s more, the KHS machines are less complex, making them easier to both operate and maintain. Production thus runs smoothly and without any issues. I’m particularly delighted with the high level of efficiency: we achieve an OEE of 76%,” Stoyanov smiles.
The entire installation process also ran efficiently despite rather adverse circumstances. “The project began during the aftermath of the Covid pandemic when there were lots of supply chain challenges,” Stoyanov recalls. “KHS was an extremely well-organized and reliable partner for us here. Once the parts had all been delivered, the schedule for installation and commissioning was precisely adhered to, even though at the same time we still had to complete our new production shop.”
Reliable and efficient
Unlike most canning lines, which use tunnel pasteurizers for microbiological safety, the Bulgarian site consciously opted for the KHS Innopro KZE flash pasteurizer. “We don’t can any sensitive beverages that we’d need a tunnel pasteurizer for,” explains Stoyanov. “Thanks to our high hygiene standards during the filling process, we’re instead able to use a flash pasteurizer on all of our systems. This improves the taste of our products. It also takes up far less space. And thanks to the faster heat transfer, we use less energy.” Stoyanov is generally very enthusiastic about the overall extremely low energy consumption of the new line. All performance values also exactly meet his expectations, as he’s pleased to discover.
Condensation avoided – quality and hygiene assured
Following the filling process, the cans pass through the KHS Innopas WICG compact heater. Frank Schneidermann, global key account manager at KHS, explains the reason for this. “The containers are filled with cold beer at a temperature of 8 to 10°C. Our compact heater raises their temperature to 20 to 28°C to prevent the formation of condensation. This can dampen the cardboard used for the trays and layer pads on the pallets, potentially leading to unhygienic mold growth. Wet cardboard can also make the pallets less stable and put their proper storage and safe transportation at risk. Given the increasingly demanding nature of logistics processes, this is an important topic – including at Carlsberg Bulgaria, where after coming off the line, the packs are transported by pallet lift to a storage area located four meters below the production shop.”
Long-term functionality
To ensure that the machines remain fully functional over time, a three-year service contract was also entered into. This includes both predictive maintenance and ReDiS, the remote service that makes it possible to directly and quickly eliminate faults, even from afar – without needing a KHS service engineer to be physically present on site.
“The reliable and continual support that we receive from the KHS Service team is extremely important to us. After all, we’re new to the world of can filling and using our technology partner’s expertise we’re first safeguarding our production processes,” emphasizes Stoyanov. Although training is part of the service package, he’s convinced that his operators will learn the most by looking over the shoulders of KHS’ service engineers and putting their acquired theoretical knowledge into practice.
Metodi Stoyanov and Plamen Zhelev (source: Frank Reinhold)
Up to 60,000 cans an hour can be filled on the KHS Innofill Can DVD which delights both Metodi Stoyanov, Carlsberg Bulgaria (left), and Plamen Zhelev, KHS.
Download image (JPG, 218 KB)Local and international beer brands (source: Frank Reinhold)
Besides with its international portfolio, Carlsberg Bulgaria primarily scores with local beer brands Shumensko and Pirinsko.
Download image (JPG, 280 KB)Innofill Can DVD (source: Frank Reinhold)
Up to 60,000 cans an hour can be filled on the KHS Innofill Can DVD.
Download image (JPG, 391 KB)Innopro KZE (source: Frank Reinhold)
The Innopro KZE takes up little space and is low on energy consumption.
Download image (JPG, 313 KB)Innopas WICG (source: Frank Reinhold)
In the KHS Innopas WICG compact heater the cold-filled cans are sprayed with warm water to heat them up to 20 to 28°C.
Download image (JPG, 359 KB)Innopal PB and Innopal PTR (source: Frank Reinhold)
With the help of robots, the KHS Innopal PB palletizer and KHS Innopal PTR pallet conveyor form layers automatically, stack products on the pallet and feed these to the logistics area.
Download image (JPG, 343 KB)