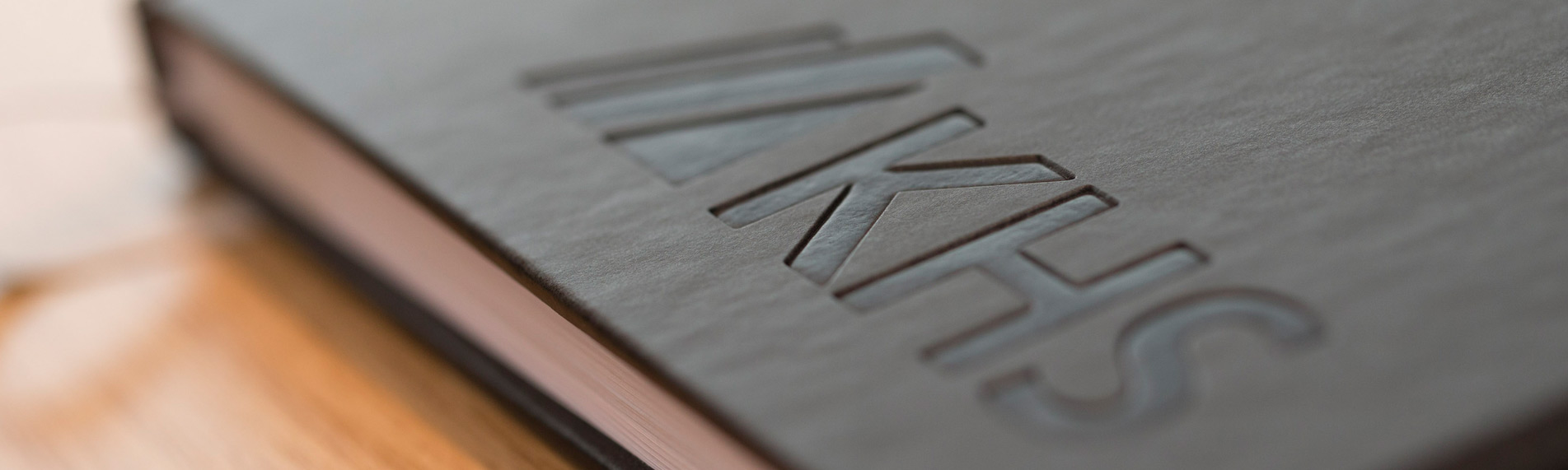
Fully recyclable: glass-coated PET bottles resolve juice production challenge
Priority for fully recyclable PET bottles: when the German Packaging Law comes into effect on January 1, 2019, the new legislation will set down binding rules to increase recycling quotas.
- Classic non-returnable PET bottles with composite materials currently difficult to recycle
- FreshSafe PET® from KHS provides sustainable solution
- With it beverage producers contribute to effective recycling process
Additives in PET bottles complicate recycling
In particular, this rule has an effect on all those beverages whose packaging materials cannot be easily recycled as they contain additives. Juice and nectar producers especially, who fill their products into PET bottles, are affected in some areas. Non-returnable PET bottles are essentially fully recyclable; however, most of today’s juice and nectar bottles do not consist solely of PET. In many cases they contain multilayer, blended or scavenger materials which protect the sensitive beverages from external influences such as oxygen pickup. The composition of these PET bottles is such that it does not allow the materials to be collected by type and recycled together with PET bottles which fall under the one-way deposit system, thus hindering the establishment of a global recycling process. “One quarter of the clear rPET flakes from yellow recycling sacks contain scavengers which impair the quality with their yellowish color, for example," states Herbert Snell, managing director of the MultiPet GmbH recycling company. “Mixing PET bottles like these with other beverage bottles made of PET makes it more much more difficult to use these rPET flakes for bottle-to-bottle recycling.” This is why at the moment they cannot be included in the German deposit system for one-way packaging, says Snell. According to a current study by packaging market research institute GVM, about 10% of all non-returnable PET bottles do not carry a deposit, meaning that in 2017 38,000 metric tons of PET material bypassed the deposit system. At present the majority of such containers is used to bottle juices and nectars. If producers in this beverage segment fail to optimize their packaging portfolio with a view to full recyclability, they also face the threat of higher additional fees for placing classic PET bottles with additives on the market.FreshSafe PET® juice bottles 100% recyclable
Beverage producers can find one alternative in the FreshSafe PET® technology provided by KHS. After the PET bottle has been manufactured, an ultra-thin glass coating is applied to its inside wall. These coated PET bottles are 100% recyclable as the coating is washed off during the recycling process, producing pure, fully segregated PET. This is also confirmed by packaging expert Benedikt Kauertz, head of Environmental Assessment of Packaging at the independent Institute for Energy and Environmental Research (ifeu) in Heidelberg, Germany. “Glass-coated PET bottles allow juice and nectar bottles to be included in the pure PET cycle and their materials to be recycled together with other used PET bottles for water and carbonated beverages, for instance. To this end, however, the deposit-assisted return system must be extended to include these specially optimized bottles.” 97.9% of non-returnable deposit PET bottles are now recycled in this manner; juice bottles are not included in this figure. The first premium juice producers have realized this and are now already using the new FreshSafe PET® technology worldwide. This can reduce the circulation of non-returnable PET bottles which are hard to recycle in the medium to long term, acknowledges Mario Dechent, director of Research and Development for the Eckes-Granini Group GmbH. “We directed our attention to the full recyclability of PET juice bottles very early on. With FreshSafe PET® coating technology we’ve been using a sustainable system to fill our beverages for over ten years now, one which also permits pure-grade bottle-to-bottle recycling and thus increases the availability of useful recycling materials.”Barrier costs also pay off thanks to lower fees
Beverage producers naturally incur additional costs when they invest in barrier technology. However, as the overall operating costs are reduced, the procurement pays off relatively quickly. With it juice and nectar producers can switch to less expensive standard PET preforms, relieving them of the obligation to source preforms from a specific manufacturer. Furthermore, compared to standard composite materials FreshSafe PET® provides a much better barrier quality and ensures much longer shelf lives. As they are fully recyclable, in the future FreshSafe PET® bottles prove more favorable when it comes to the calculation of participation fees. KHS offers beverage producers an individual consideration of the total costs accrued when using this barrier technology. “Measured against the huge benefit of additional product protection and longer product shelf lives in particular, the costs per bottle are actually lower,” says Philipp Langhammer, product manager for barrier technology at KHS Corpoplast. “In view of the possible extra costs for the circulation of PET bottles which are tricky to recycle levied by the new Packaging Law, beverage producers should make their packaging portfolio future proof now and thus help to introduce a sustainable packaging system.”Possible full ban on plastics which are difficult to recycle
Non-returnable PET bottles for juice and nectar which are difficult to recycle not only face the threat of higher fees due to their unfavorable properties. In the long term a complete ban on packaging such as the above could also even come into effect. The European Strategy for Plastics presented by the European Commission at the beginning of 2018 envisages all plastics having to be recycled by 2030. Various national initiatives in other countries of Europe are also promoting the reduction in plastic waste. In France, for example, the only plastics in use by 2025 at the latest should be recyclable. Moreover, in Great Britain new plastic packaging is to consist of an average of 30% recycled PET. International beverage producers have also begun to set themselves targets for a much higher recycling quota as a voluntary obligation. “By steadily ousting PET bottles for juice and nectar which are hard to recycle the market is increasingly opening up to recyclable packaging systems,” emphasizes Langhammer. The growing demand for FreshSafe PET® also illustrates that barrier technology has already hit a nerve among beverage producers. With it KHS provides a system which can significantly raise recycling quotas for PET beverage packaging the world over. “The move away from composite materials which are difficult to recycle has already begun,” states Langhammer. “With the help of our technology the opportunities for processing pure PET are fundamentally increased.” For more information go to: https://pet.khs.com/en/freshsafe-pet/About the KHS Group
KHS is one of the leading manufacturers of filling and packaging systems for the beverage, food and non-food industries. The KHS Group includes the following companies: KHS GmbH, KHS Corpoplast GmbH, NMP Systems GmbH and numerous subsidiaries outside Germany. KHS GmbH manufactures modern filling and packaging systems for the high-capacity range at its headquarters in Dortmund, Germany, and at its factories in Bad Kreuznach, Kleve and Worms. The KHS Group's PET expertise is pooled at KHS Corpoplast GmbH in Hamburg, Germany, where innovative PET packaging and coating systems are developed and produced. NMP Systems GmbH, a wholly-owned subsidiary of KHS GmbH based in Kleve in Germany, designs and markets new, resource-saving packaging systems. In 2017 KHS and its 5,070 employees achieved a turnover of around €1.137 billion. The companies in the KHS Group are 100% subsidiaries of the MDAX-listed Salzgitter AG corporation.KHS - InnoPET FreshSafe Block
The answer to the discrimination of juice and nectar bottles by the new German Packaging Law: FreshSafe PET® technology from KHS combines product protection with bottle-to-bottle recyclability. (Source: KHS Group)
Download image (JPG, 707 KB)PET bottles
At the moment PET juice bottles with a scavenger barrier are difficult to recycle and should therefore not enter the recycling system together with other non-returnable PET bottles. Glass bottle coating from KHS provides a system for pure-grade recycling.
Download image (JPG, 7 MB)MultiPet GmbH – Herbert Snell
Including classic juice bottles with scavengers in pure-grade bottle-to-bottle recycling makes the further processing of rPET flakes more difficult, says Herbert Snell, managing director of the MultiPet GmbH recycling company. (Source: MultiPet GmbH)
Download image (JPG, 846 KB)ifeu – Benedikt Kauertz
Benedikt Kauertz, head of Environmental Assessment of Packaging at the independent Institute for Energy and Environmental Research (ifeu) in Heidelberg, is certain that glass-coated PET bottles enable juice and nectar bottles to be included in the pure PET cycle. (Source: ifeu)
Download image (JPG, 169 KB)Eckes-Granini
The Eckes-Granini Group GmbH has been using FreshSafe PET® technology in its bottle processing for many years now. (Source: Eckes-Granini Group GmbH)
Download image (JPG, 3 MB)Eckes-Granini – Mario Dechent
Mario Dechent, director of Research and Development at Eckes-Granini, directed his attention to the full recyclability of PET juice bottles very early on. This system permits pure-grade bottle-to-bottle recycling and increases the availability of useful recycling materials. (Source: Eckes-Granini Group GmbH)
Download image (JPG, 212 KB)KHS - Philipp Langhammer
Philipp Langhammer, coating technology product manager at KHS Corpoplast, considers the glass coating of PET bottles to be an essential extension of the recycling-by-type system. (Source: KHS Group)
Download image (JPG, 526 KB)FreshSafe-PET
Information for consumers on the special bottle quality: KHS has designed a logo for beverage producers which indicates that they use the barrier coating system. (Source: KHS Group)
Download image (JPG, 271 KB)