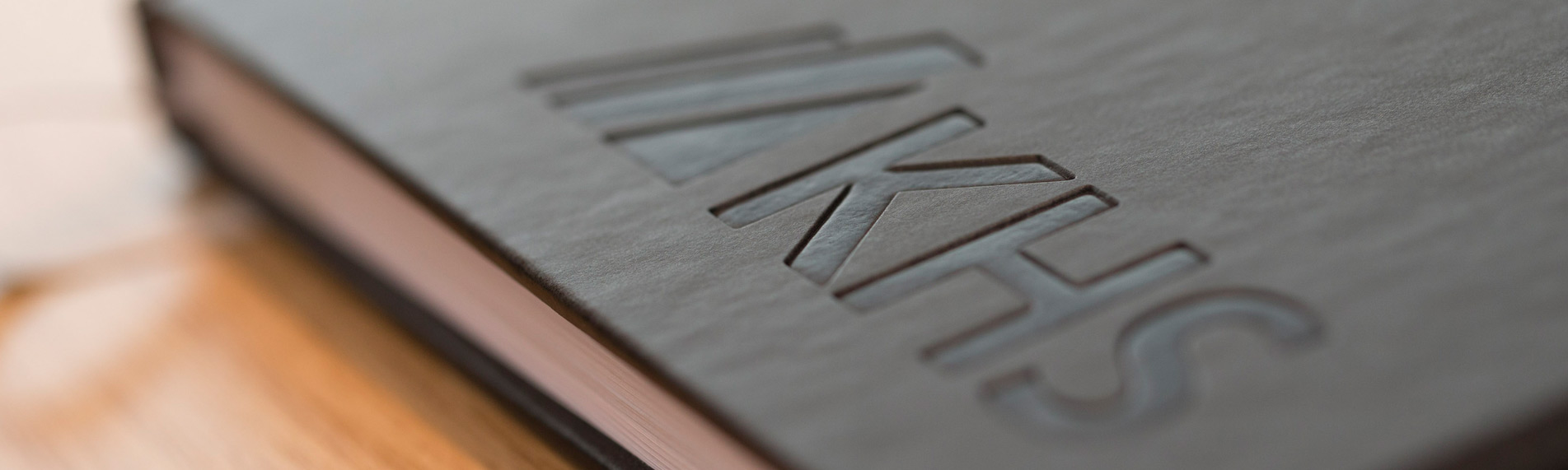
Further addition for Nature MultiPack
KHS provides universal adhesive for plastic bottles
- System can be used with practically any shape, size or material thickness of container
- Separation of PET bottles easier for consumers
- Containers fully suitable for processing in bottle deposit machines
Dortmund, November 30, 2023 – Following the launch of a universal adhesive for beverage cans, KHS is now also offering this pioneering further development for plastic bottles. This increases the possible uses of Nature MultiPack, one of the most environmentally-friendly forms of secondary packaging currently available on the beverage market.
KHS has further streamlined its resource-conserving system that joins beverage containers together with just a few dots of adhesive without using any shrink film whatsoever – and made it much more flexible in its application. After presenting its new universal adhesive that can be used on all standard aluminum cans regardless of their coating or surface treatment at the interpack trade show this year, the systems provider has now taken the next logical step and provided a similar consumable for PET bottles. These now have an adhesive at their disposal that can be used on practically any shape, size or material thickness of the same. This is facilitated by a special process where the adhesive is foamed during application to the containers. “This is a principally proven technology that’s been used for many years in the production of foam for mattresses or seals in car manufacture, for example,” explains Dr. Matthias Caninenberg, head of Nature MultiPack Technology at KHS. “In our case we face two challenges. One of these lies in the process technology, the aim of which is to reconcile three different objectives: protection of the container wall against damage, simple handling and safe transportation of the pack.”
Three objectives: a triangle of tension
In order to effect the perfect balance in this “triangle of tension”, as Dr. Caninenberg calls it, nitrogen is added to the adhesive on the KHS Innopack Kisters NMP packaging machine before this is applied to the full PET bottle. During application, the previously pressurized gas expands and foams the adhesive. This gives the glue a higher elasticity that has three benefits:
- Firstly, it is easier for consumers to separate the bottles from one another. Instead of containers suddenly snapping apart, the adhesive is compressed and peeled off much more slowly during opening. This gives people the impression that even less strength is required to unstick the containers – even though very little was needed before. Practical application is thus as simple as with the previous pack.
- Secondly, the outer wall of the PET container is subjected to less stress when the pack is opened, meaning that even with lightweight bottles with a very low wall thickness overload and damage are more or less totally ruled out.
- And thirdly, as the adhesive and thus the pack are more flexible, the forces applied along the logistics chain can be better absorbed and compensated for without the pack being damaged.
The second challenge concerns the machine technology. “The gas/adhesive mixture must be homogenous in its distribution to the applicators. To this end, we’ve developed an optimized pressure nozzle with the help of modern production facilities. What’s more, our machine operates within an extremely narrow tolerance range in order to perfectly maintain the aforementioned triangle of tension. The very first shot has to hit the tolerance window,” Dr. Caninenberg ascertains. “The machine and process technology must of course function reliably for this to be the case.”
The new setup has two further pluses to offer when it comes to the recycling of the PET containers. When separated from the container, the dots of adhesive do not leave any notable sticky residue behind and thus do not cause any disruptions when fed into bottle deposit machines. Moreover, the density of the adhesive is greatly reduced by foaming, enabling it to rise to the surface much better when washed off during the actual recycling process. This makes it even easier to remove this material from the recycling loop.
Optimum wetting
Dr. Caninenberg describes why a separate universal adhesive for aluminum cans and PET bottles continues to be necessary: “The two materials have a different surface energy. This defines how liquids behave on a solid. Unlike on a raincoat, for instance, where de-wetting creates the required water-resistant effect, we use an adhesive matched to the surface energy of the container for optimum wetting.”
In combination with a further technical novelty, the cardboard bottle clip carrying handle specially designed for Nature MultiPack, KHS gives the beverage industry “one of the most resource-conserving and environmentally-friendly forms of secondary packaging currently available,” as Dr. Caninenberg proudly sums up.
Universal adhesive for PET bottles
The new universal adhesive for PET bottles not only protects the container wall but also ensures simple handling and safe transportation of the pack.
Download image (JPG, 105 KB)KHS Innopack Kisters NMP
The packaging machine operates within a narrow tolerance window that requires absolute reliability of the machine and process technology.
Download image (JPG, 101 KB)Even easier to separate
Joined by their respective universal adhesive, both PET bottles and beverage cans can be even more easily separated by consumers.
Download image (JPG, 73 KB)Dr. Matthias Caninenberg
“Foaming the adhesive during application to the containers is a challenge to both the process and machine technology,” says Dr. Matthias Caninenberg, head of Nature MultiPack Technology at KHS.
Download image (JPG, 46 KB)