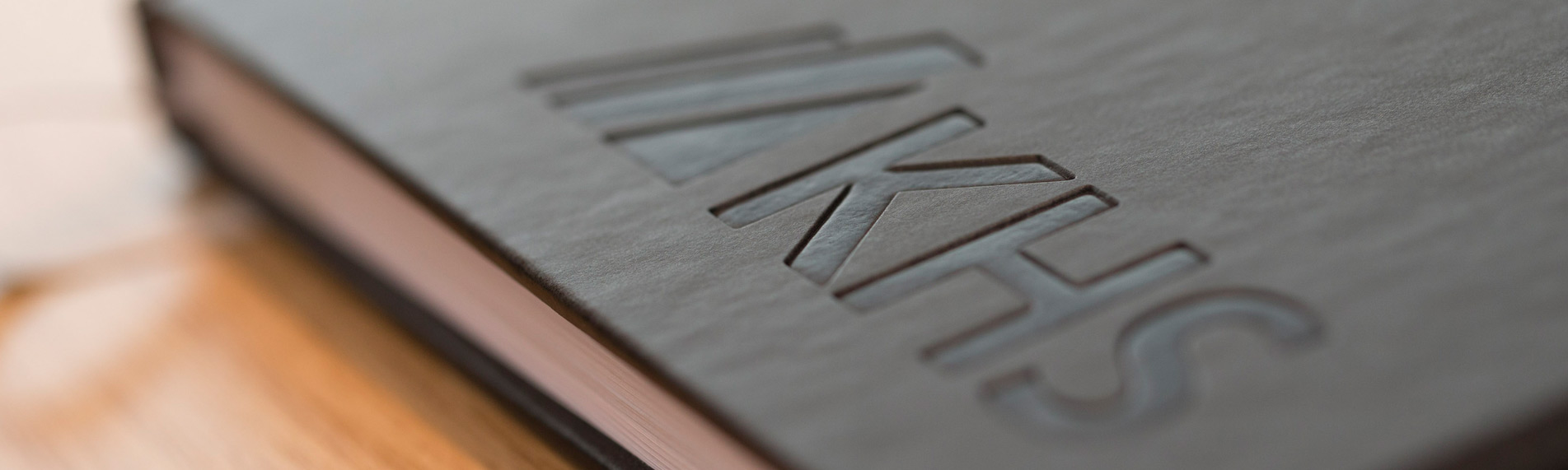
Win-Win-Situation
KHS-Linienoptimierungen sichern Getränkeunternehmen eine hohe Anlageneffizienz
Christian Schlichtenbrede*
Ilakshan Rameswaran**
Bei der Investition in neue Abfüll- und Verpackungstechnik spielt die Anlagenleistung stets eine große Rolle. Kunden verlangen eine Lösung, die den Bedarf an abgefülltem Produkt perfekt abdeckt. Die Abnahme jeder Linie erfolgt bei einem hohen Wirkungsgrad. Weit über 90 Prozent sind es in der Regel bei Dosenanlagen, um die 90 Prozent bei Glas- und PET-Linien. Ziel jeder Anlagenabnahme ist es, den höchstmöglichen Wirkungsgrad zu erreichen. Umso erstaunlicher die Tatsache, dass das Interesse am Anlagenwirkungsgrad über die Zeit hinweg bei vielen Getränkeunternehmen immer weiter nachlässt. Dabei bedeutet ein Abfall der Leistung in der Regel einen konkreten Umsatzverlust. Um wieder zu einer hohe Linienleistung zu kommen bzw. sie von Beginn an aufrecht zu erhalten, bietet KHS Getränkeunternehmen weltweit sowohl die Möglichkeit, Linienoptimierungen in Anspruch zu nehmen als auch speziell auf den jeweiligen Betrieb hin zugeschnittene Servicepakete zu ordern. Wie genau Linienoptimierungen ablaufen und was konkret von Ihnen zu erwarten ist, darum geht es in nachfolgendem Beitrag.
Reduzierter Anlagenwirkungsgrad bedeutet hohe Verluste an abgefülltem Produkt
Betrachtet man beispielsweise eine Mehrweg-Glaslinie mit einer Leistung von 50.000 Flaschen/h, die an 240 Produktionstagen im Jahr jeweils 20 Stunden produziert, entspricht ein Verlust von nur einem Prozent Wirkungsgrad einer verringerten Ausstoßmenge von 2,4 Millionen Flaschen jährlich. Innerhalb des Lebenszyklus einer Abfüllanlage können unterschiedliche Ereignisse auftreten, die die Anlagenleistung negativ beeinflussen. Beispielsweise mag es sich um technische Mängel oder um organisatorische bzw. logistische Änderungen handeln. Jegliche Minderleistung bedeutet auf die Produktmenge umgelegt eine Erhöhung der Kosten. Eine effiziente Abfüll- und Verpackungsleistung bedingt folglich sinkende Herstellkosten für das Produkt und die damit verbundene erhöhte Wettbewerbsfähigkeit des
* Leiter Service Organisation & Development, KHS GmbH, Dortmund,
Tel.: 02 31/5 69-1 08 45
**Service Organisation & Development, KHS GmbH, Dortmund,
Tel.: 02 31/5 69-1 03 02
Getränkeherstellers. Generell gilt: Aufgrund des hohen Personalbedarfs, des großen Investitionsaufwands und aufgrund von Instandhaltungskosten für die Anlage ist Abfüll- und Verpackungstechnik einer der kostenintensivsten Teilbereiche innerhalb eines Getränkeunternehmens. KHS-Linienoptimierungen verhelfen dazu, Kosten hier gezielt zu minimieren.
Vor der Anlagenanalyse steht die Vorbereitung
Entscheidet sich ein Getränkebetrieb für eine Linienoptimierung, erfolgt bei KHS als erster Schritt eine umfangreiche Vorbereitung auf die Analyse des Ist-Zustands der Anlage. Im Rahmen dieser Vorbereitungsphase werden vom Getränkebetrieb zur Verfügung gestellte und bei KHS vorhandene Unterlagen gesichtet. Dabei handelt es sich in der Regel um das Layout der Anlage sowie Daten und Fakten zu einzelnen Maschinen hinsichtlich Baujahr, Hersteller und gegebenenfalls um spezielle Zusatzfunktionen. Ebenso wichtig sind Dokumentationen über die Anlagen-Performance, Produktionslisten, Angaben, welches die Kernprodukte sind und welche Produkte bei der Verarbeitung innerhalb der Linie besonders problembehaftet sind. Generell gilt: Je mehr an Datenmaterial vorliegt, umso intensivere Vorbereitungen können stattfinden und desto gezielter lässt sich schließlich auch die Situation vor Ort beurteilen.
Bediener müssen „mitgenommen“ werden
Äußerst hilfreich ist ein der Linienoptimierung vorausgehender Vorbereitungstermin vor Ort. Hier können mit dem Produktionsleiter noch offen stehende Fragen persönlich geklärt werden. Wesentlich ist auch ein Vorabgespräch mit den Bedienern, die an der zu betrachtenden Anlage arbeiten. Zum einen, um ihnen zu erklären, welche Aktionen in Hinblick auf die Anlagenoptimierung geplant sind. Zum anderen, weil sie Hinweise zu eventuellen Schwachstellen in „ihrer“ Linie liefern können. Wichtig ist, dass Bediener eine Linienoptimierung nicht etwa als persönliche Kontrolle, sondern vielmehr als eine Chance für den optimierten Anlagenlauf und die Leistungssteigerung sowie eine damit verbundene Verbesserung der Arbeitsbedingungen wahrnehmen. Nur so wird Transparenz erreicht und ein Ideenaustausch ist möglich. In diesem Zusammenhang ist es besonders förderlich, Mitarbeiter des Unternehmens gemeinsam mit KHS-Personal bereits mit den bei der Anlagenanalyse anfallenden Tätigkeiten zu betrauen.
Bis ins letzte Detail durchdachte Beobachtung der Linie im Praxisbetrieb
Im Anschluss an die Vorbereitungsphase erfolgt als nächster Schritt die exakte Beobachtung der Linie im Praxisbetrieb. Dauer und Umfang der Anlagenanalyse richten sich mit danach wie viele verschiedene Produkte, Flaschengrößen, Verpackungsalternativen und Palettenkombinationen auf der zu analysierenden Linie zu betrachten sind. In jedem Fall muss die Produktion der „Brot und Butter“-Produkte aber auch die Produktion der Produkte, bei denen es üblicherweise kneift, unter Beobachtung ablaufen. Besonders aussagekräftig gestaltet sich eine Anlagenanalyse immer dann, wenn sämtliche Abfüll- und Verpackungsoptionen mit einbezogen werden.
An einer Anlagenanalyse sind in der Regel mehrere KHS-Techniker beteiligt. Ein Teamleiter nimmt die Einsatzplanung vor und legt Messorte fest. Als Teamleiter ist ein Senior-Techniker von KHS tätig, der über ein sehr gutes Allgemeinwissen zu sämtlichen Maschinen verfügt. Die beteiligten Techniker stammen üblicherweise aus der Region, in der das Unternehmen ansässig ist, sprechen die dort vorherrschende Sprache und kennen die Kultur. Zudem sollten – wie bereits aufgeführt – Techniker des Kunden in den Optimierungsprozess mit einbezogen sein.
Ideal ist für jedes zu betrachtende Produkt ein sechsstündiger Leistungstest. Ausgestattet mit Stoppuhren und Dokumentationsunterlagen notieren alle Beteiligten während des Anlagenlaufs das Geschehen in ihrem vorgegebenen Bereich detailgenau. Sämtliche Störzeiten werden präzise aufgezeichnet und in ein speziell hierfür entwickeltes System eingegeben. Ergebnis ist unter anderem die Darstellung der OEE (Overall Equipment Effectiveness) und sind Berechnungen zur mittleren Reparaturzeit (MTTR = Meantime to repair) sowie zur mittleren Betriebsdauer zwischen den Störungen (MTBF = Meantime between Failure) für den oben genannten Leistungstest.
Pareto-Diagramm vermittelt zügigen Störquellen-Überblick
Auf Basis der sorgfältig ermittelten Daten gilt es, Lösungsvorschläge zur Anlagenoptimierung zu erarbeiten. Ein Pareto-Diagramm gibt einen schnellen Überblick, an welchen Stellen der Linie Effizienz verloren geht und wo die größten Störquellen liegen. Theoretisch ist es möglich, sämtliche Störquellen zu beheben. Damit verbunden ist jedoch meist ein hoher zeitlicher und finanzieller Aufwand. Aus diesem Grund wird das Augenmerk häufig zunächst einmal auf jene Störquellen gerichtet, die für einen Großteil der verlorenen Anlageneffizienz verantwortlich zeichnen.
Detektivischer Spürsinn bei der Ursachenermittlung gefragt
Bei der Ursachenermittlung zu den Störungen ist oft detektivischer Spürsinn gefragt. Werden beispielsweise Störungen am Füller angezeigt, muss der Füller nicht für das Störungsverhalten verantwortlich sein. Erfahrungsgemäß sind 90 Prozent aller Ursachen von Störungen nicht in den Bereichen zu finden, in denen sie auftreten, sondern vielmehr bei vor- und nachgeschalteter Technik. Beispiel: Ein Füllsystem steht aufgrund von umgefallenen PET-Flaschen mehrmals am Tag. Der Grund für die „Umfaller“ mag dennoch nicht am Füllsystem, sondern beispielsweise an verschlissenen Übergängen oder an der nicht sachgemäßen Reinigung von Transporteuren liegen. Eine Reparatur bzw. ein intensiver Reinigungsvorgang könnten hier den Anlagenwirkungsgrad bereits um einige Prozentpunkte anheben. Generell wird alles hinterfragt. Angefangen bei den Produktionsplänen über die logistischen Abläufe bis hin zu der Qualifikation der Mitarbeiter – überall dort kann Optimierungspotenzial vorhanden sein.
Aufnahme aktueller Ist-Geschwindigkeiten und Erstellung des V-Diagramms
Zur Anlagenanalyse gehört immer auch die Aufnahme der aktuellen Ist-Geschwindigkeit jeder einzelnen Maschine. Daraufhin erfolgt die Erstellung eines V-Diagramms, welches das Leistungsgefälle der Einzelkomponenten bis zur definierten Leitmaschine – in der Regel der Füller, bei PET-Linien der Blasmaschinen-Füller-Block – darstellt. Ergibt sich kein V-Diagramm (beim Blasmaschinen-Füller-Block als Leitmaschine ist es ein Diagramm, das einen Flügel des V darstellt), sind Geschwindigkeitseinstellungen der Maschinen nicht mehr optimal. Möglicher Grund dafür: Bediener stellten bestimmte Maschinen mit dem Ziel, Störungen zu beheben oder die Anlagenleistung zu steigern, auf eine schnellere oder langsamere Arbeitsweise um. Innerhalb kürzester Zeit ist in einem solchen Fall der reibungslose Transport der Behälter durch die Linie nicht mehr gewährleistet. Es gilt nun Geschwindigkeiten derart zu regulieren, dass das klassische, der Berg’schen Kurve folgende V-Diagramm, erneut entsteht. In diesem Zusammenhang von hoher Bedeutung: die Erläuterung welche hohen Verluste an Anlageneffektivität selbst eine einzige Geschwindigkeitsregulierung mit sich bringen kann. Künftigen willkürlichen Eingriffen wird somit gezielt entgegengesteuert.
Ermittlung optimaler Pufferstrecken
Ebenso geht es bei einer Anlagenanalyse stets um die Ermittlung optimaler Pufferstrecken. Bedeutet ein zu kleiner Puffer zwischen einzelnen Maschinen eine zu geringe Zeitspanne, um eventuelle Störungen zu kompensieren, kann ein zu großer Pufferbereich nach einem Maschinenstillstand beispielsweise verhindern, dass die Linie wieder in den optimalen Betriebspunkt zurückfindet (TRNS: Time Return to Normal Situation).
KHS-Anlagensimulationssystem Innosim zeigt Auswirkungen auf
Wie sich eine Optimierung von Pufferstrecken aber auch wie sich eventuelle Umbauten oder auch neue Geschwindigkeitseinstellungen an den Maschinen und viele Änderungen mehr auf den Lauf einer Linie auswirken, lässt sich mit dem KHS-Anlagensimulationssystem Innosim anschaulich darstellen. Hiermit steht ein Werkzeug zur Verfügung, welches das dynamische Verhalten einer Linie detailgenau abbildet. Die Erstellung jedes Simulationsmodells beginnt mit der Eingabe allgemeiner Daten in das Simulationssystem wie z. B. den Behälter- und Gebindeabmessungen. Danach werden die Einzelwirkungsgrade von Maschinen mit der zu erwartenden Störcharakteristik und Fakten zu Pufferstrecken an das System kommuniziert. Eine Schicht von 8 Stunden lässt sich in wenigen Sekunden simulieren. In ein paar Minuten ist bei Simulation von zahlreichen Schichten eine gesicherte Aussage zur Anlageneffektivität unter vorgegebenen Bedingungen machbar. Neue Situationen sind in das Simulationsprogramm zügig integrierbar. So ist schnell darstellbar, wie sich die Anlageneffektivität bei Änderungen und Anpassungen verändert. In Zukunft werden hierbei auch Pufferstrecken, Formatwechselzeiten, Wartungsintervalle sowie Operator-Wege mit berücksichtigt.
Aufnahme von Medienverbräuchen kann mit in die Linienoptimierung integriert werden
Im Rahmen einer Linienoptimierung ist auch die Aufnahme von Medienverbräuchen wie elektrischer Energie, Druckluft, CO2 und Wasser möglich. Für Wasser-, Dampf- und Flüssigkeitsaufnahme hält KHS elektronische Messgeräte bereit, die Durchflüsse mittels Ultraschall aufnehmen. Ein Diagramm veranschaulicht sämtliche Energieströme in der Anlage. Im Anschluss an die Analyse zeigt KHS Möglichkeiten zur Reduzierung des Medienverbrauchs auf. Beispielsweise kann eine in die Jahre gekommene Flaschenreinigungsmaschine enorm vom Austausch der Stahlträger nebst Stahl-Flaschenzellen durch mit Kunststoff-Flaschenzellen ausgestattete Energiesparträger profitieren. Allein durch Einsatz von Energiesparträgern in der Reinigungsmaschine lassen sich 10 bis 15 Prozent Wärme sowie 15 bis 20 Prozent Frischwasser einsparen. Dazu kommt die reduzierte Laugeverschleppung. Weiteres Beispiel zur Energieeinsparung: die Umrüstung des Schrumpftunnel-Bereichs einer Verpackungsmaschine von der Elektro- auf die Gas-Beheizung. Hier fällt ein einfacher Austausch von Elektro-Heizkassetten gegen Gas-Heizkassetten sowie die Verbindung des Schrumpftunnels mit einem Gasanschluss an. Folge: eine bis zu 50 prozentige Energiekostenreduzierung. Zudem profitiert die Umwelt von einer bis zu 60 prozentigen Minderung des CO2-Ausstoßes.
Klare Win-Win-Situation
Fazit: Wer nach Einsparpotenzialen im Getränkebetrieb sucht, der sollte dort beginnen, wo große Reserven schlummern – bei der Anlagentechnik. Spezialistenwissen zu Linienoptimierungen ist im wahrsten Sinne des Wortes Gold wert. Oder anders gesagt: Bei einer Linienoptimierungen handelt es sich immer um eine Win-Win-Situation für alle beteiligten Parteien.