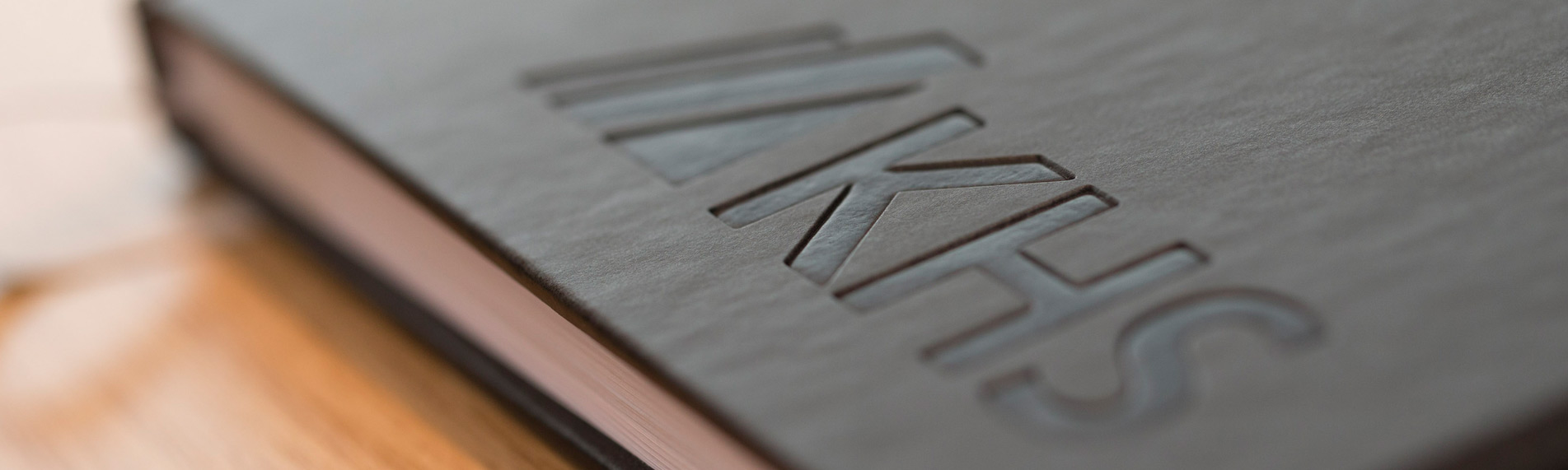
Appearing for the first time at drinktec
New Advanced series wrap-around packer and wrap-around shrink packer with plenty of extras
With its new Advanced series, KHS is able to provide the beverage, food, and non-food industries with modular packaging technology that offers maximum flexibility. Depending on the demands made by the variety of products and specific capacities, the packaging machines can be equipped with optimum functional modules in the low-, medium-, and high- capacity ranges. If required, other function modules such as tray stackers and leaflet, glass, and partition inserters can be integrated into the packaging machines or replaced at a later date. Shrink packers, tray packers, tray shrink packers, and pad shrink packers in the new Advanced series have been available on the market to date. There are now two new additions to the Advanced family: the Innopack WP wrap-around packer and the Innopack WSP wrap-around shrink packer. Wrap-around packers and wrap-around shrink packers in the Advanced series process a variety of different containers for the beverage, food, and non-food industries. Whether glass, metal, or plastic containers, cans, or cardboard cases – this new generation of machines is able to package them all perfectly at an output of approximately 100 cycles per minute. Maximum flexibility is also provided with regard to the range of cardboard to be processed; diverse types of craft and corrugated cardboard, with thickness of between 0.6 and 5 millimeters, are no problem at all. Besides making wrap-around packs, the wrap-around packers and wrap-around shrink packers in the Advanced series demonstrate their great flexibility in their ability to package products in trays and tray shrink packs. Products for wrap-around packs and tray packs are grouped using multiservo sectioning units. This type of sectioning unit allows up to four servo motors to be used and is designed exactly as prescribed by the range of products to be processed by the particular beverage company. The new multiservo sectioning unit has proved particularly advantageous when it comes to forming a number of product units with different sizes on one machine. It is also important to note that during the entire packaging process, the product groups formed are always conveyed safely and individual products held firmly in place by folding chains located in the front and rear carton packing areas equipped with cam-controlled folding pickups. At the same time, special folding cams hold both sides in place while the blanks and product group are combined. Like the other machines in the Advanced series, the wrap-around shrink packer features a newly developed functional module for film wrapping that is able to process much thinner film than has previously been possible. Perfect processing results are guaranteed with films of up to 35 µm in thickness and 950 mm in width. The servo-driven film cutter ensures highly precise film cutting with low wear. The new Advanced wrap-around shrink packer can also be equipped with what is known as an eco shrink tunnel, which as opposed to the conventional type of shrink tunnel, is gas heated and cuts energy costs by up to 50% and carbon emissions by up to 60%. Format changeover has also been optimized further. Format changeover with electronic operator prompting, introduced with the Advanced series, is now also integrated into the wrap-around packer and wrap-around shrink packer. The advantage of operator-controlled format changeover is that the operator panel informs the machine operator exactly where new settings have to be made. The electronic display of operator-controlled format changeover also communicates exactly how to adjust each station. Any play in the gear wheels or chains is already taken into account with the relevant instructions – yet another plus point. In operator-controlled format changeover, adjustments can either be made manually or using Accu-Drive. Another new feature is the folding station that in the future can be adjusted in the direction of travel simply by selecting a format at the operator panel. The additionally integrated servo motors adjust the folding and applicator chains to the new gaps for other formations practically at the push of a button.