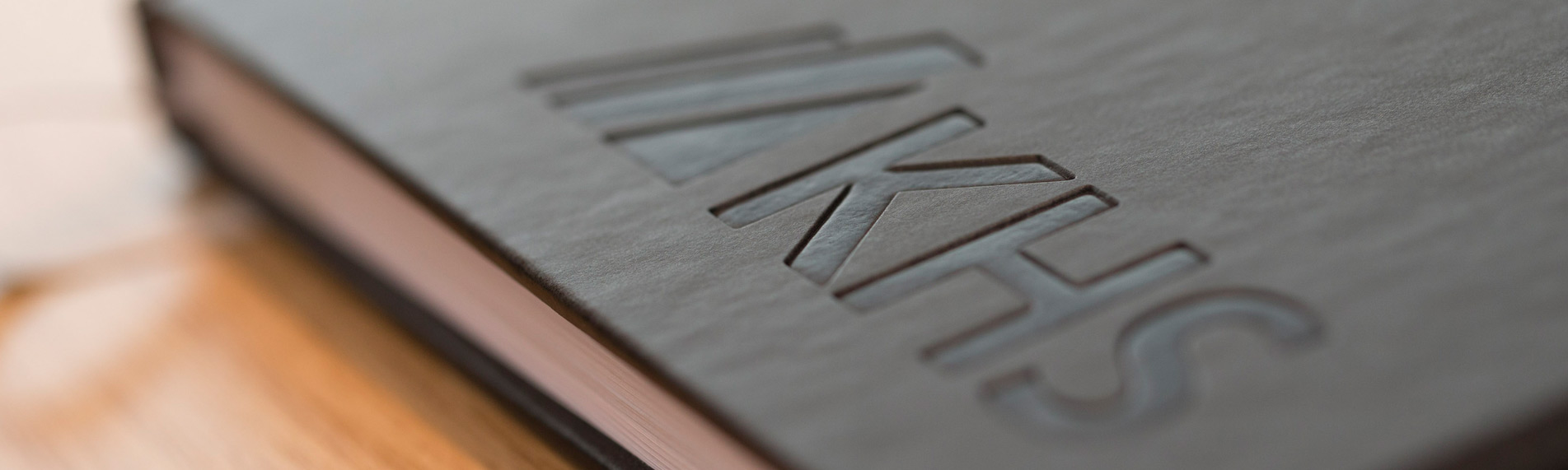
Erstmals anlässlich der drinktec präsentiert
Neuer WrapAroundPacker und WrapAroundShrinkPacker gemäß Baureihe Advanced mit umfassendem Vorteilspaket
Mit der neuen Baureihe Advanced bietet KHS der Getränke-, Food- und Nonfood-Branche modular gestaltete Verpackungstechnik, die maximale Flexibilität in sich trägt. Je nach Anforderung durch das Produktspektrum und durch die geforderte Leistung werden die Verpackungsmaschinen im niedrigen, mittleren und Hochleistungsbereich mit den optimalen Funktionsmodulen ausgestattet. Bei Bedarf lassen sich auch im Nachhinein noch weitere Funktionsmodule wie. z. B. Tray-Stapler, Glas-, Leaflet- oder Gefacheinserter in die Verpackungsmaschinen integrieren oder austauschen. Verpackungsmaschinen der neuen Baureihe Advanced befinden sich bislang als ShrinkPacker, TrayPacker, TrayShrinkPacker und PadShrinkPacker auf dem Markt. Neu sind nun gemäß Vorgaben der Advanced Baureihe gestaltete WrapAroundPacker (Innopack WP) und WrapAroundShrinkPacker (Innopack WSP). WrapAroundPacker sowie WrapAroundShrinkPacker der Baureihe Advanced verarbeiten unterschiedlichste Behälter für die Getränke-, Food- und Nonfood-Branche. Ob Glas-, Metall- oder Kunststoff-Behälter, Dosen oder Kartonverpackungen – alles lässt sich auf den neuen Maschinengenerationen perfekt verpacken. Die Leistung liegt bei bis zu 100 Takten/Minute. Höchste Flexibilität ist auch in Hinblick auf das zu verarbeitende Spektrum an Kartonmaterial gegeben. So dürfen unterschiedlichste Kraft- oder Wellpappekartons sein – angefangen bei einer Kartonstärke von 0,6- bis hin zu 5 Millimeter. Zusätzlicher Flexibilitätsaspekt: Neben der Bildung von Wrap-Around-Verpackungen managen WrapAroundPacker und WrapAroundShrinkPacker der Baureihe Advanced bei Bedarf auch die Verpackung von Produkten in Tray- bzw. Tray-Shrink-Verpackungen. Die Produktgruppierung erfolgt bei der Bildung von Wrap-Around-Verpackungen bzw. Tray-Verpackungen mittels Multi-Servo-Abteileinheit. Diese Abteileinheit erlaubt einen Einsatz von bis zu vier Servomotoren und wird ganz so ausgelegt, wie es das zu verarbeitende Produktspektrum des jeweiligen Unternehmens erfordert. Besonders vorteilhaft ist der Einsatz der neu entwickelten Multi-Servo-Abteileinheit bei der Bildung einer Vielzahl an Produkteinheiten unterschiedlicher Größen auf einer Maschine. Von höchster Bedeutung: Während des Verpackungsvorgangs sind gebildete Produktgruppen zu jedem Zeitpunkt sicher geführt und einzelne Produkte fest gehalten. Dafür sorgen im vorderen und hinteren Kartonbereich Faltketten an denen Faltmitnehmer befestigt sind, welche über Kurven gesteuert werden. Gleichzeitig geschieht ein beiderseitiges seitliches Fixieren während der Zusammenführung von Zuschnitt und Produktgruppe über spezielle Faltkurven. Der WrapAroundShrinkPacker erhält wie die anderen Maschinen in der Advanced-Baureihe das neue entwickelte Funktionsmodul für den Folienwickel. Hier lassen sich wesentlich dünnere Folien verarbeiten als bislang möglich. Bis zu einer Folienstärke von 35 µm und einer Folienbreite von 950 mm sind perfekte Verarbeitungsergebnisse gewährleistet. Das über Servoantrieb angesteuerte Folienschneidemesser sorgt für einen äußerst präzisen Folienschnitt und geringen Verschleiß. Als Schrumpftunnel kann für den WrapAroundShrinkPacker der neuen Baureihe Advanced der so genannte Öko-Schrumpftunnel zum Tragen kommen, der auf Gas-Beheizung setzt und gegenüber der herkömmlichen Schrumpftunnelvariante eine Energiekosteneinsparung von bis zu 50 Prozent und eine Reduzierung des CO2 Ausstoßes um bis zu 60% realisiert. Auch die Formatumstellung wurde weiter optimiert. So wird die mit der Advanced-Baureihe eingeführte Formatumstellung mit elektronischer Bedienerführung auch in den WrapAroundPacker und in den WrapAroundShrinkPacker integriert. Vorteil bei der bedienergeführten Formatumstellung: Der Bediener erhält bereits über das Bedienpult der Maschine Auskünfte dazu, wo genau neu eingestellt werden muss. Gleichzeitig wird bei der bedienergeführten Formatumstellung mittels elektronischer Anzeige exakt kommuniziert, wie an einzelnen Stationen zu verstellen ist. Eventuelles Spiel in Zahnrädern oder Ketten ist bei den entsprechenden Anweisungen – und das ist ein zusätzliches Plus – schon mit berücksichtigt. Wahlweise sind Verstellungen bei der bedienergeführten Formatumstellung manuell oder mittels Accu-drive zu realisieren. Neu ist auch die Verstellung der Faltstation in Laufrichtung, welche künftig einfach über die Formatauswahl am Bedienpult zu realisieren ist. Die zusätzlich integrierten Servomotoren stellen die Falt- und Andrückketten quasi per Knopfdruck auf die neuen Abstände für andere Formationen ein.