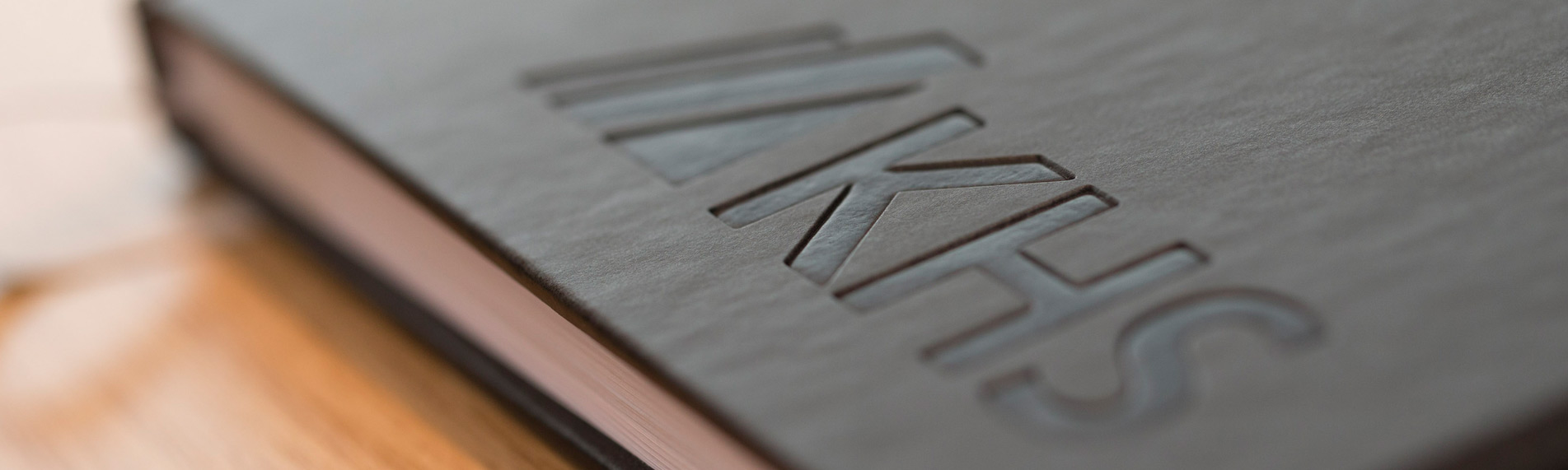
Big technology on a small scale: KHS builds compact can filler for craft brewers
Craft beers have long established themselves on the world market. The KHS Group is thus now offering a new can filler to meet the requirements of small to medium-sized brewing companies.
- For low to medium outputs of 10,000 to 48,000 cph
- Fast product and format changeovers possible
- Filler and seamer in compact plug-and-play design
No flavor carryover during product changeovers
One of the innovative features of the Innofill CAN Compact is its extremely hygienic design. In particular, this includes a gapless bell guide with PTFE expansion joints (Teflon) and bells which are lifted and positioned fully electropneumatically to seal the cans – without any mechanical action from cams and rollers. This does away with the need for water lubrication, simplifies cleaning and promises a service life which is up to twice as long as before. KHS also uses PTFE materials in the filling valve, for example to seal the filling valve piston and in the gas membranes. Flavor carryover when changing the product to be filled is thus as good as eliminated. This is of especial interest to craft brewers who often brew a large number of different beers and also make mixed beer beverages. The bell enables can necks from 200 to 206 to be processed. “We’ve managed to develop an uncomplicated piece of standard equipment which keeps procurement costs as low as possible,” says Härtel.Product tank holds 200 instead of 500 liters
The new central product tank, which is installed at the top of the filler carousel and has a working volume of 50 to 200 liters, holds 300 liters less than the product tank on the big machines. Unlike in the latter plant technology, the tank does not rotate with the filler carousel on the Innofill CAN Compact. The beverage to be canned is supplied to the filling stations by a rotary distributor. Electromagnetic inductive flow meters upstream of each filling valve permit exact filling volumes in the cans. The entire machine is very clearly structured and thus hygienic and easy to maintain.About the KHS Group
KHS is one of the leading manufacturers of filling and packaging systems for the beverage, food and non-food industries. The KHS Group includes the following companies: KHS GmbH, KHS Corpoplast GmbH, NMP Systems GmbH and numerous subsidiaries outside Germany. KHS GmbH manufactures modern filling and packaging systems for the high-capacity range at its headquarters in Dortmund, Germany, and at its factories in Bad Kreuznach, Kleve and Worms. The KHS Group's PET expertise is pooled at KHS Corpoplast GmbH in Hamburg, Germany, where innovative PET packaging and coating systems are developed and produced. NMP Systems GmbH, a wholly-owned subsidiary of KHS GmbH based in Düsseldorf in Germany, designs and markets new, resource-saving packaging systems for PET bottles. In 2016 KHS and its 4,995 employees achieved a turnover of around €1.18 billion within the Salzgitter consolidation. The companies in the KHS Group are 100% subsidiaries of the MDAX-listed Salzgitter AG corporation.Can formats
The Innofill CAN Compact processes cans holding between 150 milliliters and 1 liter.
Download image (JPG, 37 KB)Manfred Härtel
Filling product manager for KHS in Bad Kreuznach, Germany.
Download image (JPG, 371 KB)Innofill CAN Compact
The Innofill CAN Compact has a capacity of 10,000 to 48,000 cans per hour.
Download image (JPG, 911 KB)Innofill CAN Compact
The patented purging process allows approximately 30% less CO2 to be used compared to conventional systems.
Download image (JPG, 938 KB)