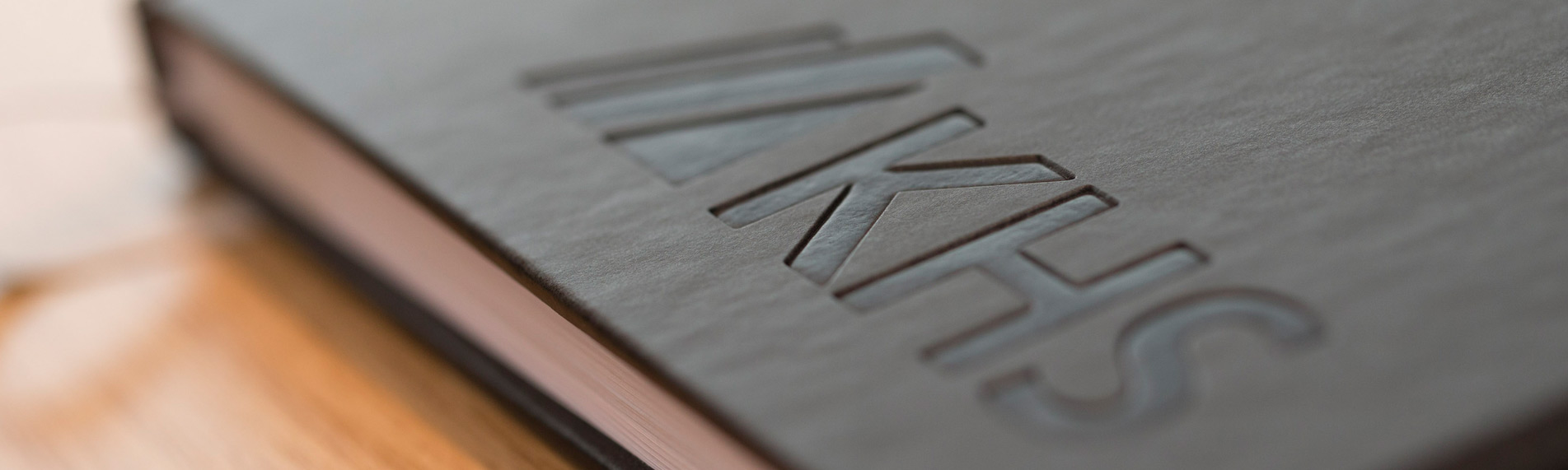
Boosting Energy and Resource Efficiency in the Manufacture of PET Bottles
First results of the study sponsored by the Federal Ministry of Education and Research
How can the efficiency of energy and resources be increased in the long term in the manufacture of PET bottles? As part of a project sponsored by the Federal Ministry for Education and Research and run by the Research Center of Karlsruhe, experts have been investigating just this in the stretch blow mold process chain. The project started in 2009 and should be completed by 2011. The first results have now been published. Also involved in the project are the Institute for Plastics Processing (IKV), the company AdPhos Innovative Technologies, Okertaler Mineralbrunnen, a mineral water bottling plant, and KHS Corpoplast. Practical tests of the latest findings are being performed on an InnoPET Blomax Series III at Okertaler Mineralbrunnen. The enormous number of PET bottles that pass through the hands of consumers year in, year out shows just how important this project is. Each year, around 25 billion PET bottles are made in Germany alone, with the figure at 500 billion worldwide. The project is paying particular attention to three criteria: the consumption of materials, electricity, and compressed air. The chief defined characteristic is the weight of the PET material used in the production of a PET bottle. As a rule, 70% of the cost for a PET bottle is attributable to the material used. Preform manufacture and the actual production of the PET bottle account for a further 15% of costs respectively. Reducing energy consumption in the manufacture of PET bottles is always equal to a reduction in cost. First experiments have shown that faster stretching of the PET material can result in a saving in materials of about 3%. For the 1.5-liter PET bottles fabricated at Okertaler Mineralbrunnen, this means that the weight of the PET could be reduced from 31 to 30 grams. One gram less material per PET bottle would lead to a considerable saving of 100,000 kilograms (roughly 220,500 lb) of PET material per annum, assuming that approximately 100 million PET bottles are produced a year. At a market price of €1.20 for one kilogram (2.2 lb) of PET, the amount saved per year would be €120,000. Tests carried out at the Okertal mineral water bottling plant to date have revealed that in the preform preheating process the consumption of energy can be optimized by up to 20%. Applying the obtained values, the amount of electricity needed to preheat preforms would drop from 0.15 kilowatt hours per kilogram to 0.12 kilowatt hours per kilogram. The new InnoPET Blomax Series IV generation of stretch blow molders is capable of even larger reductions in energy consumption of up to 30%. Potential savings in compressed air of around 31% can be made for Okertaler Mineralbrunnen's 1.5-liter PET bottle. A further 5% saving can be assumed in addition to this, brought about by a change in the shape of the bottle. This would result in a total 36% reduction in the use of compressed air, in turn generating a yearly cost cut of €26,000 if we assume that one kilowatt hour costs €0.10. Project objectives planned until 2011 include further optimization of the amount of material, energy, and compressed air used for PET bottles and the stretching process, and also research into new heating technologies. The data collected at Okertaler Mineralbrunnen on increasing the efficiency of energy and resources in the manufacture of PET bottles could form the basis for optimized PET bottle systems at any number of similar companies. Similarly, the results of the study can be used to generally classify stretch blow molders that are particularly economic in their consumption of energy.