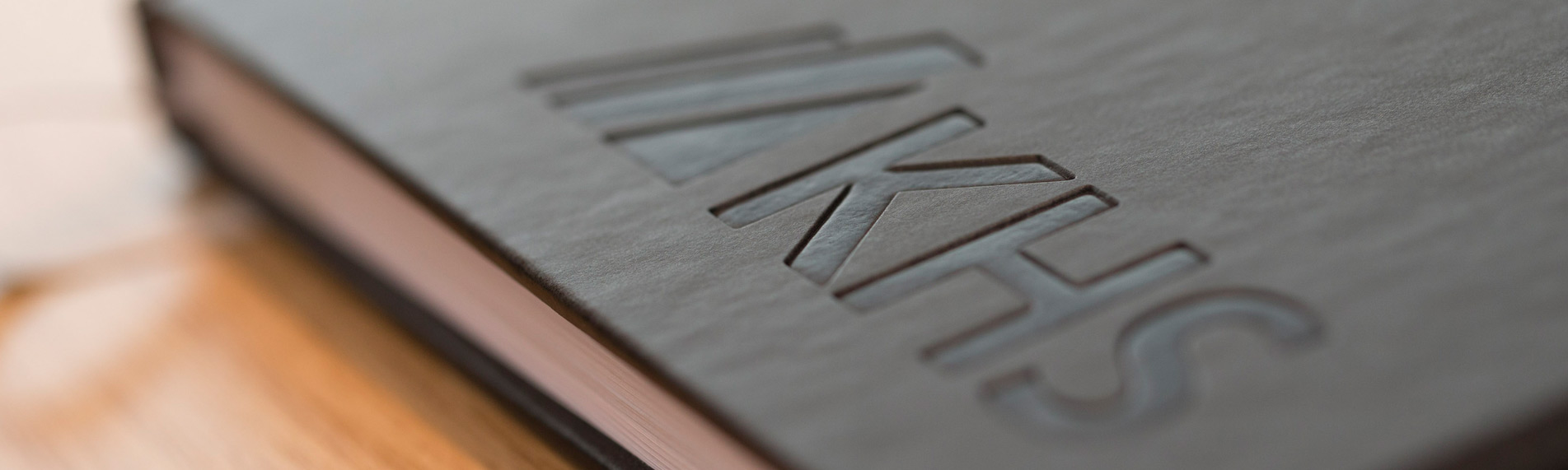
Compact, efficient, high-performance engineering: KHS exhibits systems at the Craft Brewers Conference
Innovative high-performance engineering for the low-capacity range: KHS USA, Inc. will be presenting its compact and efficient systems at this year’s BrewExpo America® which is staged as part of the Craft Brewers Conference.
- Premiere of the new Innopro Craft CIP Skid cleaning system
- Further developed Innofill Can C can filler has greater capacity
- Tailored to craft breweries and smaller beverage producers
Denver (USA), March 28, 2019 – Innovative high-performance engineering for the low-capacity range: KHS USA, Inc. will be presenting its compact and efficient systems at this year’s BrewExpo America® which is staged as part of the Craft Brewers Conference. KHS’ main emphasis at the trade show will be on the tried-and tested Innofill Can C can filler and the fully automatic Innopro Craft CIP Skid cleaning system. KHS will be exhibiting at Booth #16033 from April 8-11, 2019.
With the development of its Innopro Craft CIP Skid KHS provides a new system for the supply of rinsing and cleaning media to its can, bottle or keg fillers. “This CIP system is perfectly tailored to the requirements of the lowest capacity range,” states Rick Feuling, product manager of Filling and Process Technology at KHS USA, Inc. It has an automatic recipe setting option. Around 230 liters of caustic a minute can be produced to sanitize system piping and fillers with a maximum of 60 valves. The Innopro Craft CIP Skid also contains a fully automatic CIP media heating system, including chemicals dosing at the appropriate recipe-controlled concentration. This shortens cleaning processes and makes them safer and simpler. “With this effective and flexible system beverage producers also save on resources such as water and energy during operation,” states Feuling
Innofill Can C can filler with greater capacity
The further developed version of the Innofill Can C can filler will also be spotlighted at BrewExpo America®. Growing interest in the system has prompted KHS to engineer a new machine size with 27 filling valves and six seaming stations for the production of formats holding between 150 milliliters and one liter. This boosts the filling capacity for 330-milliliter cans, for instance, from 15,600 to 20,100 per hour. Suitable for both the beer and CSD markets, not only are the can filler’s technology and compact design convincing but also its fast installation time. As the filling and seaming stations, valve manifold, cladding and control cabinet on the Innofill Can C form an enclosed, ready-to-produce machine unit, all that has to be done during installation is to connect up the electrical cables, piping and conveyors. “Multiple reference projects realized on this market prove that KHS plant engineering has customers convinced. In addition to the growing number of craft brewers, medium-sized breweries are also asking for a cost-efficient variant for the medium-capacity range,” emphasizes Feuling.
About KHS GmbH
KHS GmbH is one of the leading manufacturers of filling and packaging systems for the beverage, food and non-food industries. The KHS Group includes the following companies: KHS GmbH, KHS Corpoplast GmbH, NMP Systems GmbH and numerous subsidiaries outside Germany located in Ahmedabad (India), Sarasota and Waukesha (USA), Zinacantepec (Mexico), São Paulo (Brazil) und Suzhou (China).
KHS GmbH manufactures modern filling and packaging systems for the high-capacity range at its headquarters in Dortmund, Germany, and at its factories in Bad Kreuznach, Kleve and Worms. The group's PET expertise is pooled at KHS Corpoplast GmbH in Hamburg, Germany, where innovative PET packaging and coating systems are developed and produced. NMP Systems GmbH based in Kleve in Germany designs and markets new, resource-saving packaging systems. KHS is a wholly owned subsidiary of the SDAX-listed Salzgitter AG corporation.
In 2017 the KHS Group and its 5,070 employees achieved a turnover of around €1.137 billion.
Innofill Can C
growing interest in the system has prompted KHS to engineer a new machine size with 27 filling valves and six seaming stations for the production of formats holding between 150 milliliters and one liter. This boosts the filling capacity for 330-milliliter cans, for instance, from 15,600 to 20,100 per hour.
Download image (JPG, 730 KB)