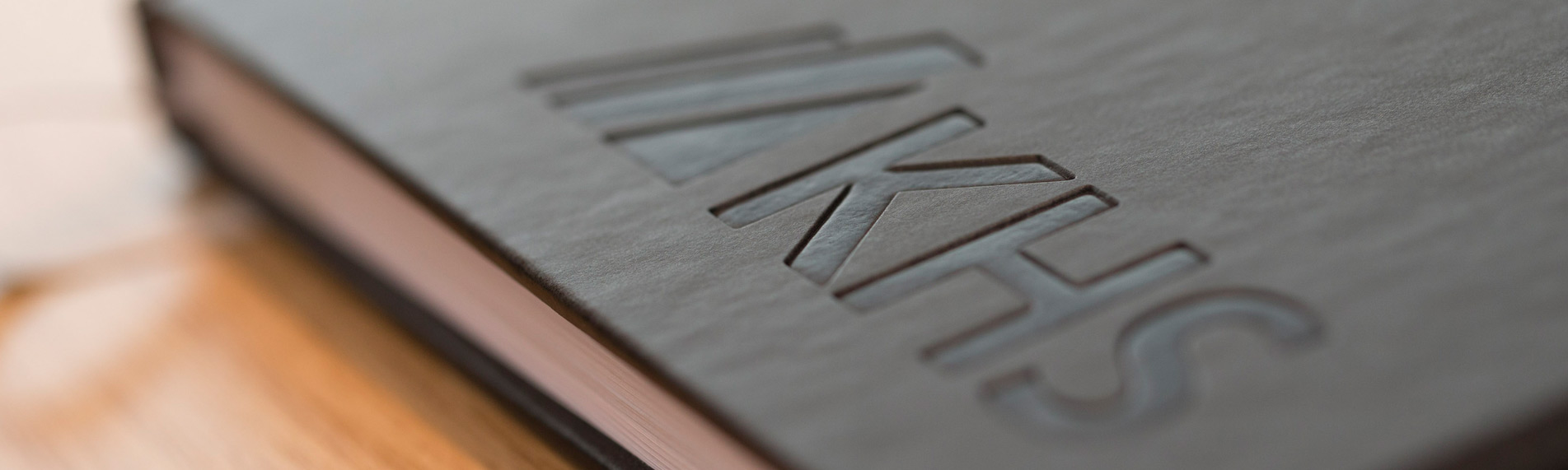
Energy costs practically halved: KHS converts stretch blow molder for Mineralbrunnen Teinach GmbH
Upgrade for KHS InnoPET Blomax Series III improves heater box efficiency
Dortmund, April 19, 2016 – Overheads for materials and the price of energy are among the biggest cost drivers in production. Mineral water bottlers Teinach GmbH have thus charged the KHS Group with the modernization of their PET bottle filling line. In the course of the process the systems supplier greatly improved the level of energy efficiency by optimizing the heater boxes on the PET stretch blow molder in particular. Non-alcoholic beverages in the Teinacher and Hirschquelle brand portfolio are the chief products for the company from the north of the Black Forest which belongs to Mineralbrunnen Überkingen-Teinach KGaA. At its plant in Bad Teinach, just under an hour's drive west from Stuttgart, the mineral water bottler achieves an output of about 150 million bottles of water and soda pop per annum, a third of which are made of PET. Preform heating consumes a lot of energy and is thus a relevant factor when it comes to the operating costs incurred during the manufacture of PET bottles. One of Michael Schanz's main tasks, head of Engineering at Mineralbrunnen Teinach GmbH, is thus to constantly monitor the energy efficiency of the lines. He was therefore immediately enthusiastic about the new possible savings offered by KHS' InnoPET machines. KHS analyzed the savings potential of the reliable InnoPET Blomax Series III together with the engineers from the mineral water company. The stretch blow molder in Teinach has been in operation since 2007. "Over the last nine years the machine has given us wonderful service. KHS then showed us that with little effort we could improve further on our levels of energy efficiency," Schanz explains. After a maximum of two days the machine would again be ready for operation, yielding savings of up to 50%. "After we'd discussed the details, it only took a few weeks before conversion started." This was possible as KHS was able to make use of a tested development from its energy-saving solutions product module. Optimized heater box geometry with ceramic reflectors The upgrade primarily consisted of converting the heater box on the Blomax Series III Compact where the PET preforms are heated for the downstream stretch blow molding process. Frank Goebel, head of Service Engineering at KHS, highlights the development of the past few years: "We have almost 600 Series II Blomaxes in operation worldwide. We aim to continue to support the operators of these durable machines even after many years of service." At Teinach this specifically means saving over 40% in energy by converting the heater box which KHS achieved by adding new reflectors made of modern ceramics to the heater boxes and precisely adjusting the geometry. Thanks to their special design the physical properties of the ceramic elements have a very positive impact on the energy distribution, resulting in less energy being needed to heat the preforms. The reflectors and infrared emitter are also built so that the sensitive bottle thread area is not unnecessarily heated. The amount of cooling in this area can then be reduced, thus saving Teinach even more energy. This higher efficiency often also makes it possible to shorten the heating segment, explains Goebel. If fewer heating elements are required in the heater, the infrared emitter consumption also drops as a result. KHS usually converts the heater boxes on all Series III Blomaxes in a maximum of two days. KHS process engineers make the fine and final adjustments during the startup phase so that disruption to production is kept very short. Teinach's head of Engineering is suitably satisfied with his company's decision to invest in this new feature. "We're always trying to save energy to cut costs and protect the environment," states Schanz. The bottler demonstrates this outside the production shop, too, through its a long-term cooperation with the Central/North Black Forest Nature Park for the conservation of the unique local countryside, for example. Or with its system of energy management, certified according to ISO 50001. "We can simply read off the history of the heating costs for the modernized system on the electricity meter and document the significant savings," he claims. Schanz also adds that KHS converted the line quickly and competently without affecting system operation. Since the end of last year the revamped heater box has been running without any problems whatsoever. Through the amount of energy saved, investing in a modernization of the InnoPET Blomax Series III pays off for users after one to three years depending on the line's capacity utilization and the price of electricity. KHS also offers the conversion for both versions of the Blomax Series II: the Modular or the Compact. "For many companies, energy-optimized PET stretch blow molders are an excellent way of reducing production costs," says Goebel. He expects more orders for this sustainable KHS conversion product in 2016. About Teinach Mineralbrunnen GmbH Mineralbrunnen Teinach GmbH is part of Mineralbrunnen Überkingen-Teinach GmbH & Co. KGaA. The regional brand company fills about 1.5 million bottles of non-alcoholic beverages a day. The mineral water bottling plant produces Teinacher and Hirschquelle Vital mineral waters, a curative Hirschquelle water and soda pops Teinacher Limo, Limo Light, ISO, ACE and Multi 10. Mineralbrunnen Teinach GmbH has 130 employees and is situated in Germany's largest nature reserve, the Central/North Black Forest Nature Park which covers approximately 3,750 square kilometers. Besides holding the Energy Management System Standard according to ISO 50001, ISO 500001 and IFS Food Version 6 2013 certificates, Mineralbrunnen Teinach GmbH was the first mineral water plant to be granted the Assured Sustainability – Investment in the Future seal of approval for sustainability in ecology, economy and social competence in 2013 by the private German Institute for Sustainability and Economy. Teinach thus stands for sustainable product, service and consultancy quality, future economic orientation and forward-looking corporate management and social and ecological responsibility. About the KHS Group The KHS Group is one of the leading manufacturers of filling and packaging systems for the beverage, food and non-food industries. The KHS Group includes the following companies, among others: KHS GmbH, KHS Corpoplast GmbH, KHS Plasmax GmbH and NMP Systems GmbH. KHS GmbH manufactures modern filling and packaging systems at its headquarters in Dortmund, Germany, and in Kleve, Bad Kreuznach and Worms. The KHS Group's PET expertise is pooled at KHS Corpoplast and KHS Plasmax in Hamburg, Germany, where light PET packaging and innovative coating systems are developed and produced. NMP Systems GmbH, a wholly-owned subsidiary of KHS GmbH based in Düsseldorf in Germany, designs and markets new, resource-saving packaging systems for PET bottles. The group has an international production and service network. In 2015 KHS was awarded the Top 100 seal of approval for exceptional innovative power and outstanding innovative success among German SMEs. In 2015 the company with 4.871 employees achieved a turnover of €1.172 billion based on the Salzgitter Consolidated Group. The companies in the KHS Group are 100% subsidiaries of the MDAX-listed Salzgitter AG corporation.