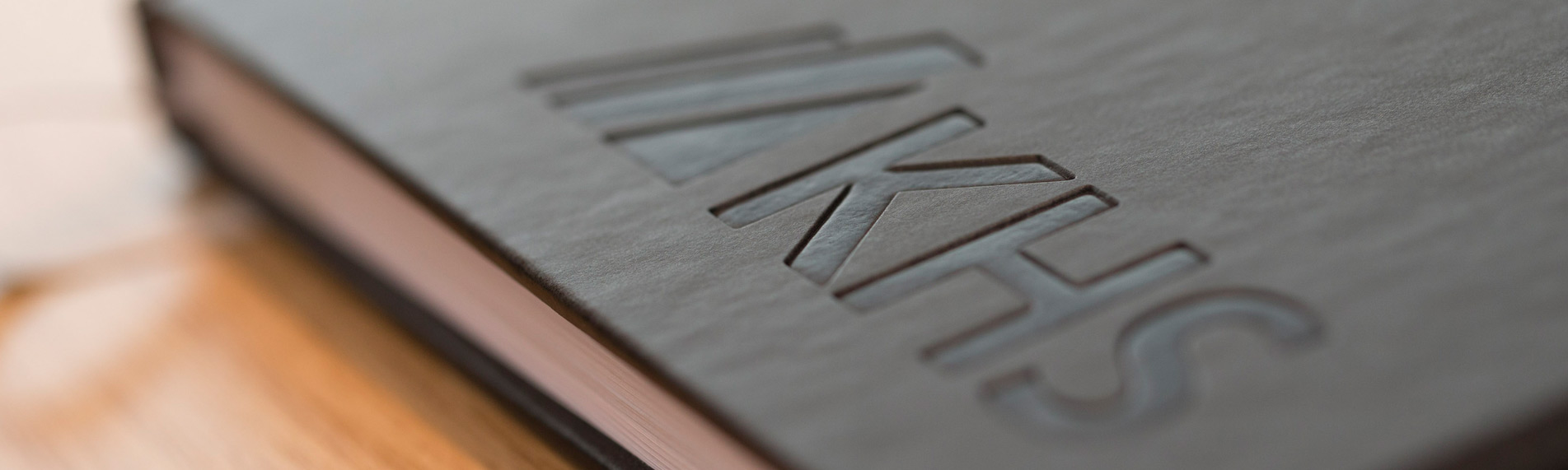
Expertise for the resource-saving and flexible filling of sensitive products
First linear InnoPET BloFill ABF aseptic block from KHS satisfies current dairy requirements.
The market for sensitive beverages is flourishing. Throughout the world manufacturers of dairy products have recognized the potential of wholesome beverages and expanded their product portfolio over the past few years. Most of the new products are filled into PET bottles. With its new linear InnoPET BloFill ABF aseptic block KHS is satisfying the requirements of the dairy industry for flexible filling technology for sensitive products. Fast format changeovers and a modular design are the ideal solution to the rapid changes in demand producers are now faced with.
Sensitive beverages are becoming increasingly popular all over the world. The demand for functional foods with less sugar in particular is growing. “Keeping to a healthy diet is playing a central role in the lives of more and more consumers,” explains Thomas Redeker, sales director for Dairy Europe at the KHS Group. “The demand for products that are sustainably packaged and attractively presented has also greatly increased in the last few years.”
Dairy industry innovations filled into PET containers
PET bottles are the ideal vehicles for this new trend. An increasing number of makers of dairy products are thus relying on containers made of polyethylene terephthalate. “Not only producers but also consumers are convinced by their many different advantages,” says Redeker. In particular this includes the great capacity for individual design this type of container has. “PET bottles lend themselves to exclusive design. The cap and label can also be perfectly tailored to the brand. This had a positive effect on the brand positioning at the point of sale,” Redeker states.
The plastic containers also score when it comes to their environmental balance as they are fully recyclable. PET bottles not only provide reliable product protection; they also have good pouring properties.
KHS satisfies customer and consumer demands with new block
KHS first recognized the potential of PET containers for aseptic filling 25 years ago. Its latest development is the linear InnoPET BloFill ABF aseptic block. This combines the rotary InnoPET Blomax Series V stretch blow molder with the linear Innosept Asbofill ABF 712 aseptic filler.
The block yields many benefits. It not only takes up less space than the individual machines, for instance; the air conveyor is also no longer required. This cuts down on energy consumption. Another advantage is that personnel costs are reduced as only one operator is needed in place of the former two. “By blocking the machinery and including a continuous clock module we also minimize the risk of soiling. This has a positive impact on hygiene and line availability," smiles Redeker.
Fast format changeovers within the space of up to ten minutes also help to boost system availability. They are performed under aseptic conditions, doing away with the need for any additional cleaning and sterilization. The short changeover times also let producers of sensitive beverages fill a large number of different stock-keeping units (SKUs) in a very short time indeed. The linear aseptic block is designed to fill milk, mixed milk beverages, juice, smoothies and iced tea into PET bottles holding between 250 milliliters and two liters. The equipment outputs up to 12,000 1.0-liter bottles and a maximum of 15,000 0.5-liter bottles per hour.
Bottlers also profit from the modular design of the dry aseptic block which allows the filler to be expanded at any time. Operators can retrofit their block with a chunk filler or additional filling and capping unit, for instance. “The modular design gives our customers greater flexibility. They don’t have to think about precisely which products they want to bottle when purchasing the block,” Redeker says. “KHS enables them to retrofit the required modules on site as soon as they expand their product portfolio.” This in turn permits beverage producers to react more flexibly to changing market demands.
Stretch blow molder with high energy savings gentle on the environment
With the integration of the stretch blow molder the aseptic block gains a number of further plus points. One of these is that the heating system in the new Blomax generation consumes up to 40% less energy compared to most standard heating systems thanks to its optimized near infrared heating concept and new Double Gate technology. This is made possible by the near infrared heater centrally installed in the closed reflector tunnel. In the heater the preforms pass the centrally arranged heating units to both the left and right. The preforms are spaced just around 18 millimeters apart instead of the previous approximately 37 millimeters. The Dortmund systems supplier has thus been able to considerably reduce the number of heater boxes used. The air management system for heater box ventilation has also been optimized. “The fan can be set separately for the neck, reflector and lamps. This means that the machine only cools the areas which actually need cooling,” explains Redeker.
Effective sterilization with the KHS system
When further developing its linear aseptic filler KHS also focused on increased efficiency. The filling machine for sensitive products is available in both a standard aseptic and ESL version. In the KHS process sterilization takes place in several stages. First, the machine disinfects the neck and bottle interior. Here, the inside of the container is sprayed twice with a hydrogen peroxide aerosol (H2O2) at a speed of up to 80 kilometers an hour. “This ensures that every part of the bottle is sprayed and sterilized; we even achieve this with individual designs and critical shapes,” Redeker states. Secondly, two aerosol reaction cycles are initiated. The process ends with a four-stage drying process which uses sterile hot air.
Gentle filling ensures product protection
In order to ensure the quality of the products, it is essential that the aseptic zone is absolutely clean. KHS ensures this by gentle non-contact filling, among other things, performed in two stages. This prevents any excessive beverage foaming.
After filling the bottle is conveyed to the capping unit. Here, the closure is sterilized in the same manner as the bottle in the filling section. This entails two-step disinfection with H2O2 and two drying stages with hot sterile air. “In the capper unit we’ve also made sure that all parts in the aseptic zone have a flat surface. By doing so we can prevent any air turbulence, making cleaning and disinfection easier,” Redeker comments. The bottle is then dated for full documentation of all information. “Our customers can always see which product was filled when on which valve,” explains Redeker.
One-block system
With its new dry aseptic block KHS has reacted to the current dairy demand for flexible, resource-saving filling of sensitive products. The new system also boosts line availability and considerably reduces energy consumption. Operators also have greater flexibility thanks to the short changeover times: format changes are facilitated by the well-coordinated interfaces. The modular design also enables customers to expand their linear aseptic filler block in order to meet current market demands at all times.
About the KHS Group
The KHS Group is one of the leading manufacturers of filling and packaging systems for the beverage and liquid food industries. The KHS Group includes the following companies: KHS GmbH, KHS Corpoplast GmbH and numerous subsidiaries outside Germany, located in Ahmedabad (India), Sarasota and Waukesha (USA), Zinacantepec (Mexico), São Paulo (Brazil) and Suzhou (China).
KHS manufactures modern filling and packaging systems for the high-capacity range at its headquarters in Dortmund, Germany, and at its factories in Bad Kreuznach, Kleve, Worms and Hamburg, where the group's PET expertise is pooled. The KHS Group is a wholly owned subsidiary of the SDAX-listed Salzgitter AG corporation.
In 2019 the KHS Group and its 5,149 employees achieved a turnover of around €1.260 billion.
InnoPET Blomax Series V
The heating system in the new Blomax generation consumes up to 40% less energy compared to most standard heating systems thanks to its optimized near infrared heating concept and new Double Gate technology.
Download image (JPG, 168 KB)Innosept Asbofill ABF 712
The linear Innosept Asbofill ABF 712 filler for sensitive products is available in both a standard aseptic and ESL version. In the KHS process the containers are sterilized using a hydrogen peroxide aerosol and sterile hot air.
Download image (JPG, 99 KB)Blocking
By blocking the stretch blow molder and linear filler the systems supplier minimizes the risk of soiling. This has a positive impact on hygiene and line availability.
Download image (JPG, 177 KB)High output
The new linear InnoPET BloFill ABF aseptic block from KHS is designed to fill milk, mixed milk beverages, juice, smoothies and iced tea into PET bottles holding between 250 milliliters and two liters.
Download image (JPG, 178 KB)Growing PET segment in the dairy industry
With its new dry aseptic bock the systems provider has reacted to the current dairy demand for flexible, resource-saving filling of sensitive products into PET containers.
Download image (JPG, 158 KB)