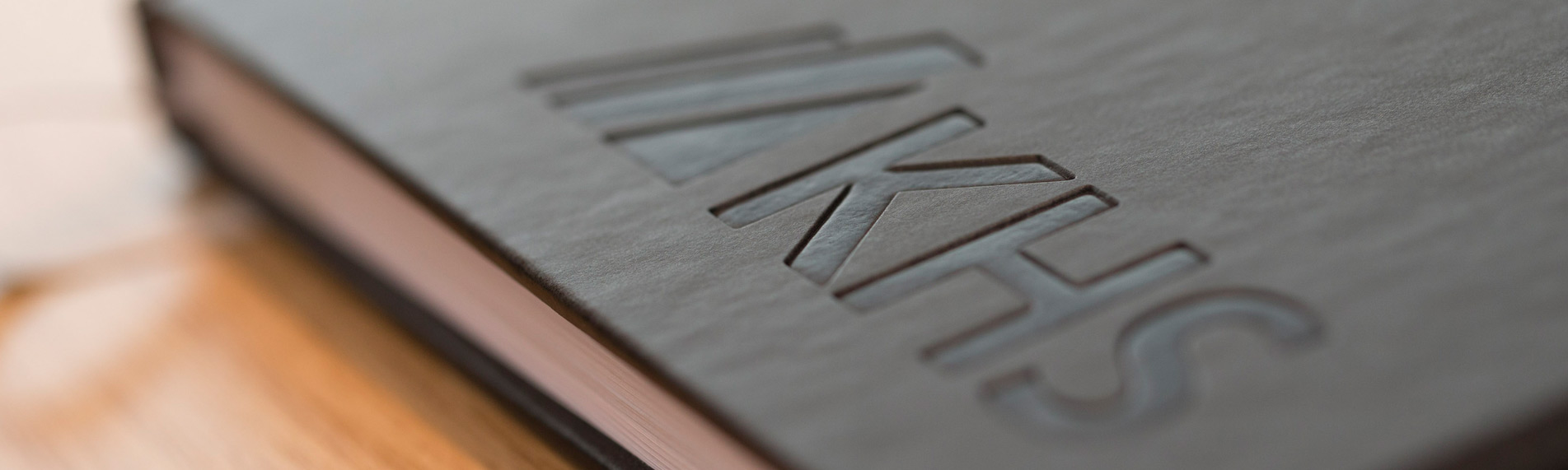
Flexible and low on space: KHS presents innovative block systems for the sensitive range
Yoghurt is no longer spooned out of the pot but drunk. Breakfast is no longer just eaten at the kitchen table but also on the hoof.
- Hygienic filling of sensitive beverages
- Modules for individual customization
- KHS’ new chunk dosing unit
Microbiological safety, little space required
Another advantage of the linear system is that it is particularly efficient where there are frequent format changeovers and smaller product batches. It also reliably sterilizes bottles and closures. “The filler can be combined with a screw capper, film/foil sealer, nitrogen application or the new chunk dosing unit as required,” Niehr informs us. The KHS dosing module provides bottlers with flexible product design options by adding chunks to the beverage, such as whole cherries, strawberries, vegetables or cereals with a length of up to ten millimeters.New modular system for rotary machines
Besides the new developments for its linear filler KHS also offers a new modular system for its rotary machines for high-performance filling. The new concept can process between 24,000 and 36,000 and in the future even up to 54,000 bottles per hour depending on the bottler’s required production capacity. The system offers plenty of scope as regards the bottle size, with container volumes ranging from 250 milliliters to 1.5 liters. With the new KHS concept the machines can be adapted in the form of standardized modules for three hygiene categorization classes specified by the German Engineering Association or VDMA. Ultraclean KHS filling machines (UCF) satisfy the requirements of VDMA class III, extended shelf life fillers (ESL) those of class IV and KHS aseptic filling machines those stipulated by VDMA class V. “In the future a KHS filler can be configured depending on which hygiene class a beverage producer’s products fall under and precisely tailored to suit the individual specifications of the customer,” says Niehr.About the KHS Group
KHS is one of the leading manufacturers of filling and packaging systems for the beverage, food and non-food industries. The KHS Group includes the following companies: KHS GmbH, KHS Corpoplast GmbH, NMP Systems GmbH and numerous subsidiaries outside Germany. KHS GmbH manufactures modern filling and packaging systems for the high-capacity range at its headquarters in Dortmund, Germany, and at its factories in Bad Kreuznach, Kleve and Worms. The KHS Group's PET expertise is pooled at KHS Corpoplast GmbH in Hamburg, Germany, where innovative PET packaging and coating systems are developed and produced. NMP Systems GmbH, a wholly-owned subsidiary of KHS GmbH based in Kleve in Germany, designs and markets new, resource-saving packaging systems for PET bottles. In 2016 KHS and its 4,995 employees achieved a turnover of around €1.18 billion within the Salzgitter consolidation. The companies in the KHS Group are 100% subsidiaries of the MDAX-listed Salzgitter AG corporation.Chunk dosing unit
KHS has extended its portfolio to include a new chunk dosing unit which provides flexible product design options – such as the addition of chunks measuring up to 10 x 10 x 10 millimeters.
Download image (JPG, 908 KB)Linear aseptic
New developments make the KHS Innosept Asbofill ABF linear filling system even more powerful.
Download image (JPG, 973 KB)Linear aseptic
KHS now supplies the linear Innosept Asbofill ABF machine as a space-saving block system.
Download image (JPG, 842 KB)Rotary aseptic
KHS offers a new modular system for its rotary machines for hygienic filling in the high-performance range.
Download image (JPG, 1 MB)Rotary aseptic
The rotary filler can be configured depending on the hygiene categorization class and tailored to suit customer requirements.
Download image (JPG, 1 MB)