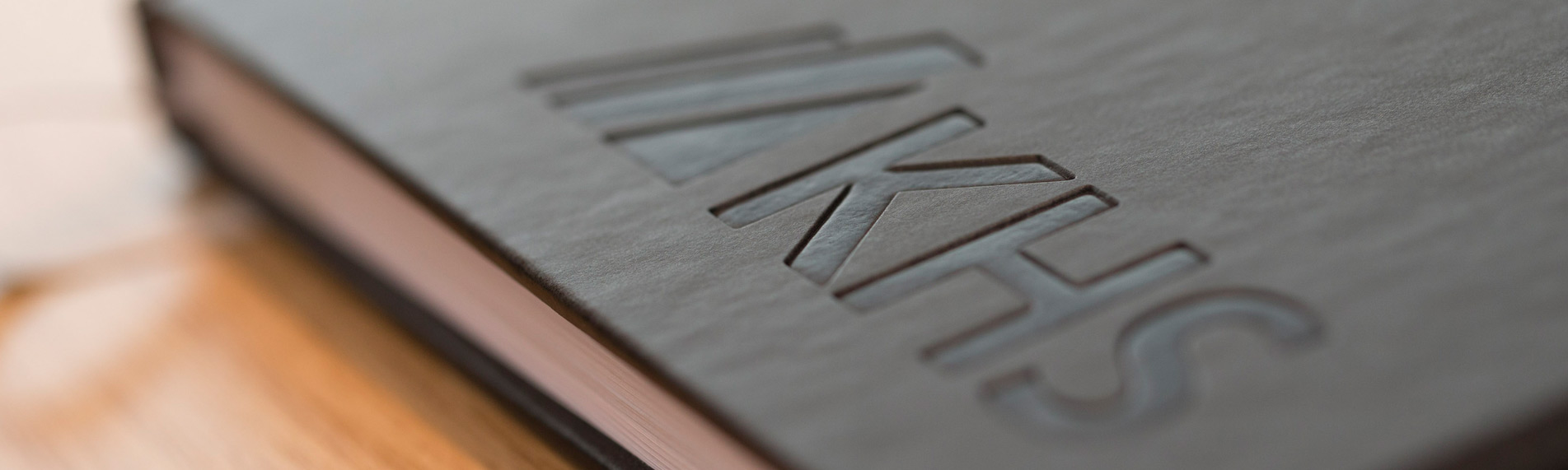
Increased Availability, Simplicity, and Reduced Costs
Modularization of vacuum pumps offers an extensive range of advantages
Olaf Muszinski* Filling beer without using vacuum pumps is no longer imaginable. These pumps not only help the gas exchange when filling bottles made of glass; in doing so they also considerably reduce the oxygen pickup and the amount of CO2 consumed. The standard practice to date was to supply a vacuum pump specifically suited to the customer's respective filling system based on given facts, such as the filling capacity, the product temperature, and the product's CO2 content. This meant that the KHS portfolio comprised a multitude of pump models of various size with different electrical systems and fittings. Modularizing the vacuum pumps has now made it possible to provide a standard vacuum pump model. Breweries now only have to reach one decision with regard to the capacity of the filling system, namely: should I invest in one, two, or three identical vacuum pumps? Apart from simplifying configuration, the modular system offers plenty of extra advantages, such as a reduced power consumption, higher availability, simplified maintenance, and partial or full redundancy achieved by specifically expanding the system. Vacuum pumps reduce CO2 consumption Low oxygen filling plays an important role when bottling beer, ensuring the high quality and long shelf life of the product. So that this essential filling method can be implemented with a minimum oxygen pickup, the gas has to be exchanged before the containers are filled in order to create a CO2 atmosphere. Following evacuation, CO2 is blown into the container to be filled, with oxygen slowly being expelled and replaced by CO2. Should CO2 be filled into the container without a vacuum pump being used, the consumption of this gas would be extremely high. To avoid this, vacuum pumps are used to assist the rinsing process at the beginning of the filling process. If glass bottles are being filled, vacuum pumps generate a negative pressure in the bottles, thus specifically drawing in air which is then compressed and released into the atmosphere. CO2 is then filled into the bottles to replace the expelled air. Vacuum pumps therefore ensure a faster and more thorough gas exchange and also reduce the amount of * Manager, Process Engineering Design, KHS GmbH, Bad Kreuznach. Phone: +49 (671) 852-2704 CO2 used, thus cutting costs and being kinder to the environment. Vacuum pumps are active throughout the entire gas exchange process within a filling system. Larger, individually configured vacuum pump used to date to get reliable results In the past, vacuum pumps were used that were specially configured to suit a specific filling system. Engineers calculated the lowest possible theoretical size of pump based on the intended hourly flow rate, the product temperature, the amount of CO2 contained in the product, and various other criteria. Once this minimum theoretical value had been computed, customers were advised to invest in a larger vacuum pump that came close to the theoretical pump dimensions. This was done to ensure that both the given filler output and the lowest possible oxygen pickup in the beer were reliably achieved. At the same time, this meant that the slightly higher pump power selected to give reliable results also increased the amount of electricity and thus water consumed by the machinery. Modular vacuum pump with integrated frequency converter now in use Modularizing the vacuum pumps means that this higher consumption of electricity is no longer necessary. This modularization also results in only identical vacuum pumps being used. A frequency converter is installed upstream of the pumps, which on the one hand ensures that these are independent of the electrical system and on the other that each vacuum pump always runs at its optimum operating point. Should the filling system require less vacuum when filling smaller bottles which have a lower flow rate, for instance, when controlled by the frequency converter the vacuum pump thus runs more slowly, or one of the pumps is completely shut down. If a higher flow rate is needed, the frequency converter then specifically boosts the pump output. This perfect adjustment of vacuum pump to filling system alone results in up to 45% less electricity being used, creating an optimum ratio between the vacuum and the power consumption. Even when the filler is underperforming or should it come to a standstill due to problems on the line, one or two of the pumps can be switched off. Frame structure with up to three standard vacuum pumps Where a single standard vacuum pump may be sufficient for low filler capacities, for higher filling outputs up to three standard pumps may be required. The pumps are positioned in a frame which can hold up to three standard vacuum pumps. Particularly where filling capacities are low, this enables partial or even full redundancy if expansion modules are incorporated. A second frame holding up to three standard vacuum pumps can be integrated into the system where filling capacities are especially high to ensure partial or full redundancy. Standard vacuum pumps are made of stainless steel or cast iron, depending on the customer, the advantage of stainless steel being that it can be cleaned with either water and caustic or with acid. Example application with minimum power consumption and partial redundancy The following gives an example of how the electricity consumption can be brought down to a minimum and partial or full redundancy can be achieved using the advantageous new system. A filling system has a capacity of 50,000 0.33-liter or 50,000 0.5-liter glass bottles an hour. The client plans to use a vacuum pump with a connecting load of 18.5 kW which can cope with all of its filling requirements. The operating point output at 50 Hertz is 14.5 kW. With this 14.5 kW the vacuum pump can cope with a bottling rate of 26,000 liters an hour, resulting in a calculated reserve vacuum of 4%. If the pump fails, the line stops. By way of comparison, we shall now take a look at what happens when modularized vacuum pumps are used in the same scenario. Two vacuum modules are used with a connecting load of 16 kW each. If the 0.33-liter glass bottle is to be filled at a rate of 16,500 liters an hour, it is sufficient to use just one of the vacuum pumps which is operated at between 50 and 60 Hertz. If one pump fails, the second pump could provide a 100% reserve, meaning the filling system would continue to run at full capacity. Should the 0.5-liter glass bottle be scheduled for filling at an output of 25,000 liters an hour, the second pump could be switched in and run so that the necessary residual vacuum is available yet the pump always runs at its optimum operating point with a low number of Hertz. Should a pump fail at the required output of 25,000 liters an hour, the filler would not have to come to a standstill. The capacity of the pump still operating could be increased by the frequency converter and the output of the filler automatically throttled. This means that in this example operators could rely on a filling capacity of 75%. The standby vacuum pump If even more reliability is required, based on the example described above it would be possible to integrate a third standard vacuum pump into the system as a standby. Apart from having the advantage that a standby pump can be quickly switched into the system, another plus point is that during any planned maintenance there must not necessarily be any loss of output – nor must the line be shut down. Fast availability of vacuum pumps and spare parts Another asset of the modularized vacuum pump is that the spare parts have also been standardized. This means that delivery can be rapid, should this be necessary. As the spare parts are similar, even if more than one vacuum pump is used, less space is needed to store spares. Yet another bonus of the modularized vacuum pump concept is that should a pump become faulty, it can be quickly replaced. It is no longer necessary to manufacture specially designed and configured pump models, thus also reducing pump manufacturing time. Should there be no replacement standard vacuum pump on site, the wait time would be reduced to that required for the pump to be shipped to the customer's plant from KHS' central warehouse. Eco vacuum pump also modularized The KHS modularized vacuum pump concept is being applied to both the classic water ring pump and the KHS Eco vacuum pump. The clear advantage of the Eco vacuum pump is that it saves water. The additional components in the Eco vacuum pump are the beer pre-separator and the heat exchanger. While compressed gas is specifically discharged as it is in the classic vacuum pump, in the Eco vacuum pump the water passes to a heat exchanger where it is cooled to the required temperature. This thus does away with the need to pipe in fresh water to bring down the water temperature – a procedure required by the classic vacuum pump – before the water is sent to the intake end of the pump. Where the average water consumption for the classic vacuum pump is 12 liters of water per hectoliter of beer, the Eco vacuum pump uses just 0.3 liters of water for the same amount of beverage. Consequently, using the Eco vacuum pump, water consumption can be reduced by an impressive 97% as opposed to that of the classic vacuum pump. Reduction in cooling capacity yet another benefit All of the advantages mentioned above in conjunction with the modularized vacuum pump apply to both the classic water ring pump and the Eco vacuum pump. Yet another boon of the modularization concept pertinent to the KHS Eco vacuum pump alone is that when the electricity consumption is reduced by the pumps being constantly run at their optimum operating points, the amount of cooling required in the heat exchanger is also reduced to the same degree. A reduction in cooling capacity of up to 45% can be achieved here. Already prepared for future energy efficiency regulations In modularizing its vacuum pumps KHS is not only meeting current energy efficiency regulations (EC no. 640/2009) but also those regarding motor design which will soon come into force. As the identical vacuum pumps are fitted with an IE2 motor and frequency converter, according to the present status of statutory regulations KHS is already well prepared for the energy efficiency specifications due to come into effect on January 1, 2017. Well thought-out down to the last detail All told, the new vacuum pump modularization concept offers breweries an extensive range of remarkable benefits – one that would not have been feasible simply by integrating a frequency converter into existing vacuum pump concepts. In addition to cutting down on the consumption of electricity, the new system also has the advantage of enabling redundancy, the particularly fast procurement of spare parts, and simplified maintenance. This in turn increases the availability of the line, thus resulting in a concrete increase in production performance.