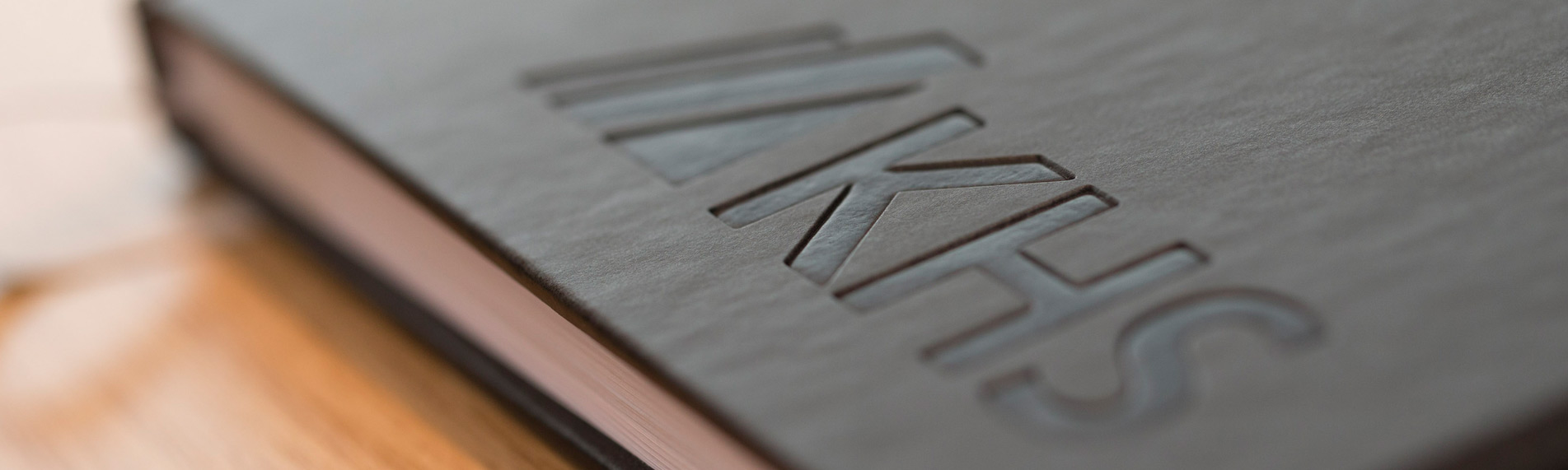
KHS Connect
Digital interfaces developed further for even closer cooperation with the customer
- Fast retrieval of information and data exchange on the digital service portal
- Digital machine label: direct access to specific system information
- New secure data interface to the KHS cloud for machine monitoring and analysis
Dortmund / Nuremberg, November 29, 2023 – Strong connection: KHS lines and machines are in operation the world over, with all relevant information on the same collated on the digital KHS Connect service portal. This considerably speeds up the exchange of data between the Dortmund systems supplier and its customers. Which conversion options are available for a client’s line or what’s the status of a spare parts order? Detailed, customized answers to questions such as the above can be found on the portal. New digital machine labels now make it even easier to access all of the necessary information. In developing a secure cloud-based access system to machine data through the portal, KHS is also setting a further milestone in the field of line monitoring.
“We can no longer imagine data exchange with our customers without the digital KHS Connect service portal that hugely facilitates networked communication on both sides,” says Kathrin Gareis, service product manager at KHS. “It enables beverage fillers to obtain relevant information on their lines whatever the time of day or night or wherever they happen to be. As in an online shop you can use it to view your order history, for instance, follow instructions or find customized recommendations for any line conversions you might need.” If a wear part is required that cannot be immediately named, for example, KHS’ experts can quickly identify it once a photo has been uploaded.
Quicker and more direct: from the line straight to the service portal
In conjunction with KHS’ new digital machine labels customers can now retrieve data relevant to their machine(s) even faster. On new machines the label is directly attached to the HMI during commissioning. Existing machines are to be successively provided with labels in the course of on-site service engineer assignments. By simply scanning the QR code or using the near-field communication or NFC function, operators can directly access their respective machine section in KHS Connect using their smartphone or tablet.
Next level: cloud-based machine monitoring and analysis
In developing a secure interface for data exchange between customer machines and the KHS cloud, the systems supplier from Dortmund is taking the next important step toward new forms of cloud-based cooperation. In the future, this will allow KHS experts to evaluate detailed real-time data from machines remotely if required in order to recognize where these can be optimized or identify problems during production and react to these. At the moment pilot projects are underway at a number of beverage production facilities that receive a summary of their machinery’s relevant KPIs through KHS Connect. The first step in and basis for this further development was to implement KHS Connect Remote Edge on existing production lines. This easy-to-install, plug-and-play hardware is already standard in new commissioning operations and can be retrofitted to existing machines without any trouble whatsoever. “The use of this setup paves the way for future IIoT applications,” says Deniz Ulutürk, product manager for digital products at KHS. “In establishing secure interfaces to the KHS cloud, we now enable our clients to use multiple forms of application software on the basis of KHS Connect Remote Edge.”
Extended options – from any location with independent software
What makes data transmission via the KHS cloud on the service portal so smart is that through the dashboard real-time data can be accessed and intersite analysis provided at any time and from any location. “Cloud access is a valuable addition to our powerful local line IT systems Innoline Flex Control and Innoline BLM (Basic Line Monitoring). These modular, standard software packages which have been adapted specifically for the beverage industry provide a customized overview of the entire filling process, giving operators an essential competitive edge,” emphasizes Ulutürk. “Our interface, designed to meet high cybersecurity requirements, allows completely new digital solutions to be used on the KHS cloud, regardless of the operating system – whether this is desktop-based or mobile.” The benefit for customers is that KHS provides independent updates to ensure that the latest software version is always in use. “The foundations for an even more digital future in our direct relations with our customers have been laid. These will now be built upon further,” Ulutürk announces.
KHS Connect (Source: Frank Reinhold)
Through the digital KHS Connect service portal customers can access all information relevant to their lines and machines whenever they wish and wherever they happen to be. As in an online shop the portal displays the status of all orders and recommends possible conversions.
Download image (JPG, 48 KB)Digital machine labels (Source: Jörg Schwalfenberg)
By scanning a QR code or using the near-field communication or NFC function, customers can access their respective machine data on the digital KHS Connect service portal even faster using their mobile device.
Download image (JPG, 81 KB)KHS Connect Remote Edge (Source: Frank Reinhold)
The easy-to-install, plug-and-play KHS Connect Remote Edge device readies production line hardware for future IIoT applications.
Download image (JPG, 79 KB)Kathrin Gareis (Source: Frank Reinhold)
“We can no longer imagine data exchange with our customers without the digital KHS Connect service portal that hugely facilitates networked communication on both sides,” says Kathrin Gareis, service product manager at KHS.
Download image (JPG, 45 KB)Deniz Ulutürk (Source: Jörg Schwalfenberg)
“With our digital KHS Connect service portal, powerful hardware and secure interfaces to cloud-based data exchange, we’ve paved the way for completely new forms of digital cooperation with our customers,” says Deniz Ulutürk, product manager for digital products at KHS.
Download image (JPG, 62 KB)