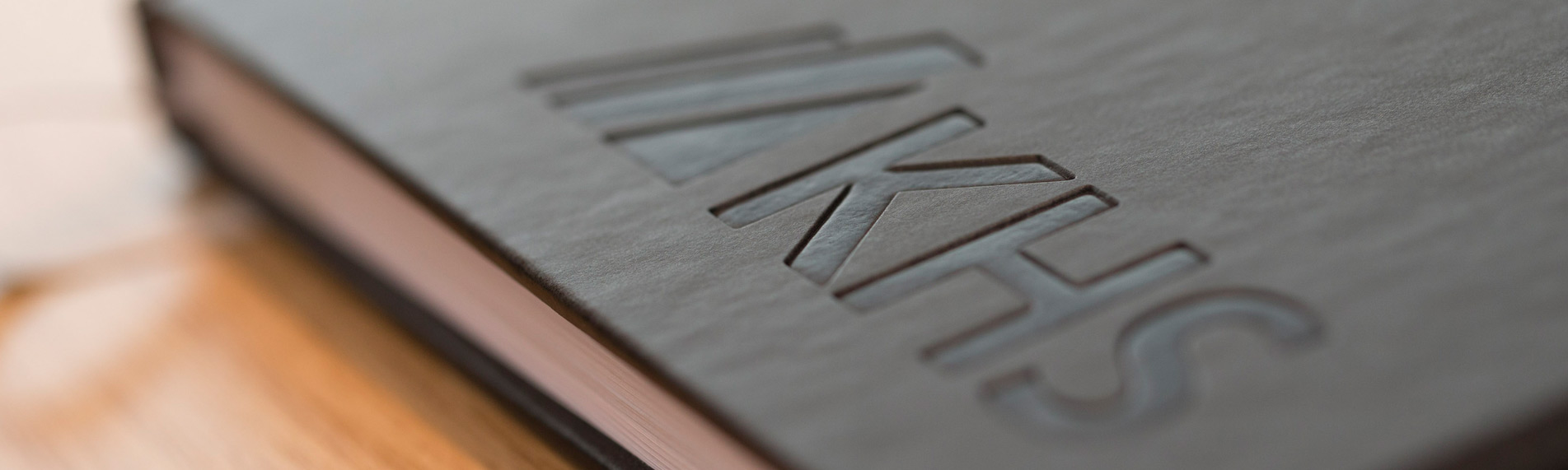
KHS lubricants and individual consulting: KHS expands its service portfolio
The KHS Group is expanding its portfolio for consumables, and in the future will offer customers all products from one source.
- Time savings and cost advantages thanks to high availability on site
- Simplified documentation for error-free maintenance
- Comprehensive and individual advice from certified employees
Dortmund, November 14, 2018 – The KHS Group is expanding its portfolio for consumables, and in the future will offer customers all products from one source. Bottlers no longer need to dependent on products offered by external suppliers. This not only results in cost advantages, but also simplifies machine maintenance. In addition, KHS continues to expand its consulting services with certified employees even further.
"By expanding our product portfolio, we have now significantly simplified the highly complex subject of bottling plant lubricants for our customers," says Daniel Raatz, Head of Maintenance Products at KHS. As a rule, bottlers require in-house specialists for lubricants who keep track of the products procured from different suppliers. The Dortmund-based system provider now offers everything from one source, emphasizes Raatz. This includes comprehensive consulting services and lubricant plans adapted to customer requirements. In the future, the company will be additionally offering lubricants optimally tailored to KHS machines. "This makes it possible to even more precisely use suitable products for all systems in operation," says Raatz.
Special antimicrobial lubricants
KHS offers, for example, standard and special antimicrobial lubricants for its Innofill filler series, dry lubricants for its Innoline pack conveying technology, and those with special adhesion properties for its Innopack shrink packers. "We only supply H1 lubricants1) that are manufactured from synthetic components," explains Raatz. The life cycles of these products are longer than those of mineral oil-based products which means longer intervals between lubricant changes and reduced operating costs. Another criterion for KHS was that none of the lubricants offered are declared as hazardous substances or dangerous goods. KHS products have also been certified as harmless according to food and health law requirements by the National Sanitation Foundation (NSF)2). Approval of a lubricant by the NSF is required in the production process if occasional or technically unavoidable contact with food can occur. "Customers who must be certified in accordance with the directives and international IFS food standards3)require H1 lubricants in bottling plants," explains Raatz. The halal and kosher certification of KHS lubricants is also relevant for bottlers and producers who produce products according to Muslim or Jewish food specifications.
Advice also on complex challenges
KHS provides all customers competent advice regarding their individual lubricant requirements. For this purpose, systems manufacturer KHS initially offers users overviews that are tailored to their machines and lines and contain information on lubricant changing intervals and quantities. "Precise specifications of this kind increase production reliability and efficiency," says Raatz.
In addition to personal advice, KHS customers will find detailed lubricating instructions in the operating manuals and spare parts lists. In the case of challenges such as increased operating temperatures, timely and condition-oriented lubricant changing can extend the service life of machines. In the future, necessary preventative lubricant changes will be displayed on the HMI panel thereby enabling KHS to offer its customers all the necessary information from planning to ongoing production.
CLS-certified employees
In addition to technical advice provided by CLS-certified employees (certified lubrication specialist), machine manufacturer KHS also provides support with regard to all operational lubricants and lubrication points on KHS systems. "Converting to a reduced lubricant portfolio which KHS has been adapted to existing systems, will result in significant cost savings for customers," Raatz points out. Moreover, KHS ensures a faster availability of products.
1) H1 lubricants are food grade lubricants for machinery and equipment used in the food industry, for example.
2) The NSF - National Sanitation Foundation - tests and certifies products and systems according to food and health law requirements.
3) International Featured Standards: IFS standards are standardized food, product, and service norms that ensure that certified companies produce and operate in accordance with specifications agreed to with customers.
About the KHS Group
KHS is one of the leading manufacturers of filling and packaging systems for the beverage, food and non-food industries. The KHS Group includes the following companies: KHS GmbH, KHS Corpoplast GmbH, NMP Systems GmbH and numerous subsidiaries outside Germany.
KHS GmbH manufactures modern filling and packaging systems for the high-capacity range at its headquarters in Dortmund, Germany, and at its factories in Bad Kreuznach, Kleve and Worms. The KHS Group's PET expertise is pooled at KHS Corpoplast GmbH in Hamburg, Germany, where innovative PET packaging and coating systems are developed and produced. NMP Systems GmbH, a wholly-owned subsidiary of KHS GmbH based in Kleve in Germany, designs and markets new, resource-saving packaging systems for PET bottles.
In 2017 KHS and its 5,070 employees achieved a turnover of around €1.137 billion within the Salzgitter consolidation. The companies in the KHS Group are 100% subsidiaries of the MDAX-listed Salzgitter AG corporation.
Consumables
KHS consumables save customers time and offer significant cost advantages for operating bottling lines.
Download image (JPG, 7 MB)