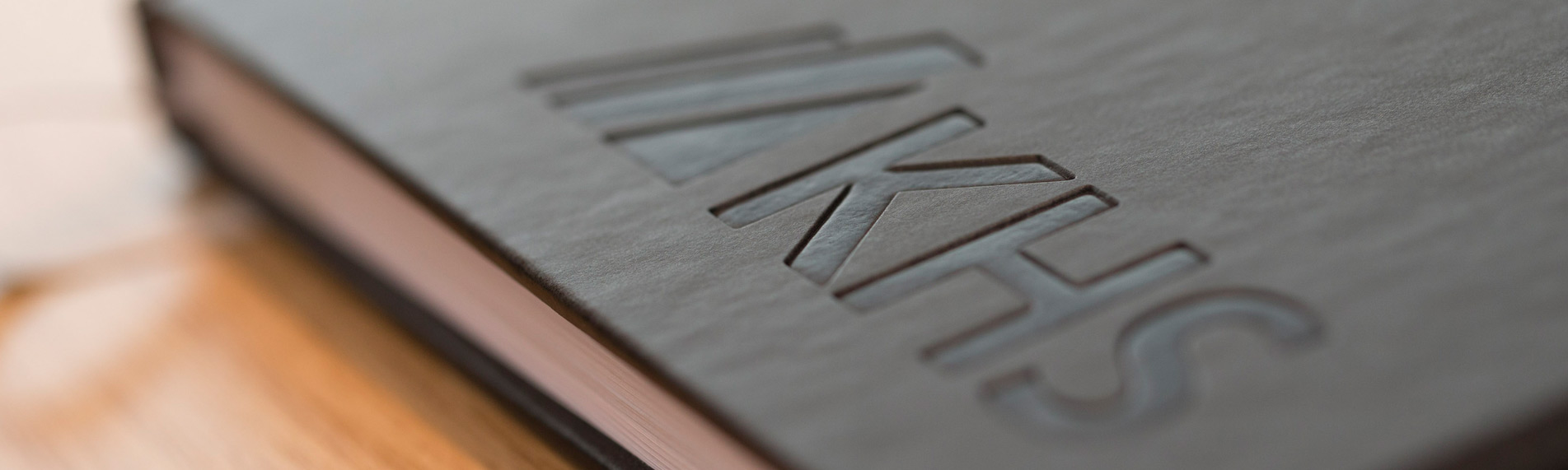
Press Release: Brau Beviale
KHS offers a broad range of innovations and services
At this year's Brau Beviale one of the world leaders in filling and packaging technology KHS will be presenting a wide range of innovations. With its new platform system Innofill Glass, for example, the company will be heralding a new dawn of filling machines for glass bottles. The Innofill Glass filler works on the following principle: a base machine is provided to which various electronic KHS filling systems can be added. The beverage-specific characteristics of the individual filling processes are taken into account in every respect. The main aspect of the platform system is the concept of Hygienic Design that has been consistently implemented right down to the last detail. This has resulted in a number of largely simple functional elements that include many benefits, such as enhancement of the filling quality, improved equipment availability, and reduced costs for energy, water, cleaning agents, and maintenance. The Innofill Glass platform system is controlled by the new, award-winning KHS operator panel (red dot award and iF award) with an integrated RFID system. The first KHS filling system to profit from this innovative platform system is the Innofill DRS-ZMS pressure filling system for beer and soft drinks, now well established in the brewing sector. Consistent further development of the filling procedure ensures high beer quality through an extremely low-oxygen filling process with low consumptions. One outstanding innovation in the field of process technology is the newly developed Innopro ECOStab. The Innopro ECOStab is a regenerative beer stabilizing system which uses PVPP. As opposed to those which include classic horizontal mesh and gap cartridge filters, the cost of investment for the Innopro ECOStab is much lower. This system thus appeals not just to large beer companies but also to small and medium-sized breweries. Compared to standard systems the Innopro ECOStab requires a lower PVPP volume which means that much less PVPP is used. Other plus points of the Innopro ECOStab are the fact that the system permits PVPP materials from different manufacturers to be used; that it operates continuously with a high degree of automation, can be packed into a container, and has a compact frame design which enables fast installation and commissioning. Low container volumes in the Innopro ECOStab also mean that the setup times for system startup and shutdown are short, that changeover times between various types of beer are also kept brief, and that the blending amounts are slight when beer types are changed over. KHS has designed the extremely compact Innokeg Till CombiKeg keg washing and racking machine specifically with small and medium-sized businesses in mind. It operates on the proven rotary processing principle that KHS has been steadily further developing for decades. The standard Innokeg Till CombiKeg R3 has three washing heads, one racking head, and a volumetric filling system with return gas control. The Innokeg Till CombiKeg also comes in an R5 version with five washing heads and one racking head. The Innokeg Till CombiKeg is modular in design, enabling a great number of possible configuration options. These include incorporating the exterior keg washer and the media tanks in the system housing, for instance. The patented Direct Flow Control (DCF) racking system saves up to 40% of CO2 per keg. Fully assembled and tested, the machine fits in a standard-size container and can be installed and commissioned in the shortest time imaginable according to the Plug & Produce principle. KHS' most recent innovation in labeling technology, the Innoket 360 S, will also be presented during Brau Beviale. This roll-fed labeling machine furthers the tried-and-tested expertise of the Innoket 360 labeler and generates even more advantages. The Innoket 360 S is modular, extremely compact in design, and can be configured and expanded to meet the customer's individual labeling requirements. As with the proven Innoket 360, the Innoket 360 S has a segmented vacuum drum for quick and simple changeover. And also like the Innoket 360, the highlight of the new Innoket machine's cutting unit is that the cutters are self-sharpening. This ensures functional stability as well as long-lasting precision cutting. KHS has defined the mineral water, fruit juice, and soft drinks bottling segment as the main target group for the Innoket 360 S. The chief objective of KHS is that its customers are satisfied and extremely pleased with KHS technology – and remain so throughout the entire life cycle of their KHS machinery. Service is thus being allotted great importance at Brau Beviale 2011. Presentations in this area include countless upgrades for older KHS machines which boost the performance of outdated KHS technology and which at the same time meet the high demands of the beverage industry for lines and systems that are sustainable. Another key topic of the trade show is the KHS spare parts concept which has been thoroughly rethought. Under the motto of Best Value KHS will be focusing on customer requirements and showing that top spare parts quality goes hand in hand with a fair price for spares. This Best Value label has been established following the biggest reworking of the KHS spare parts price structure the company has ever seen.