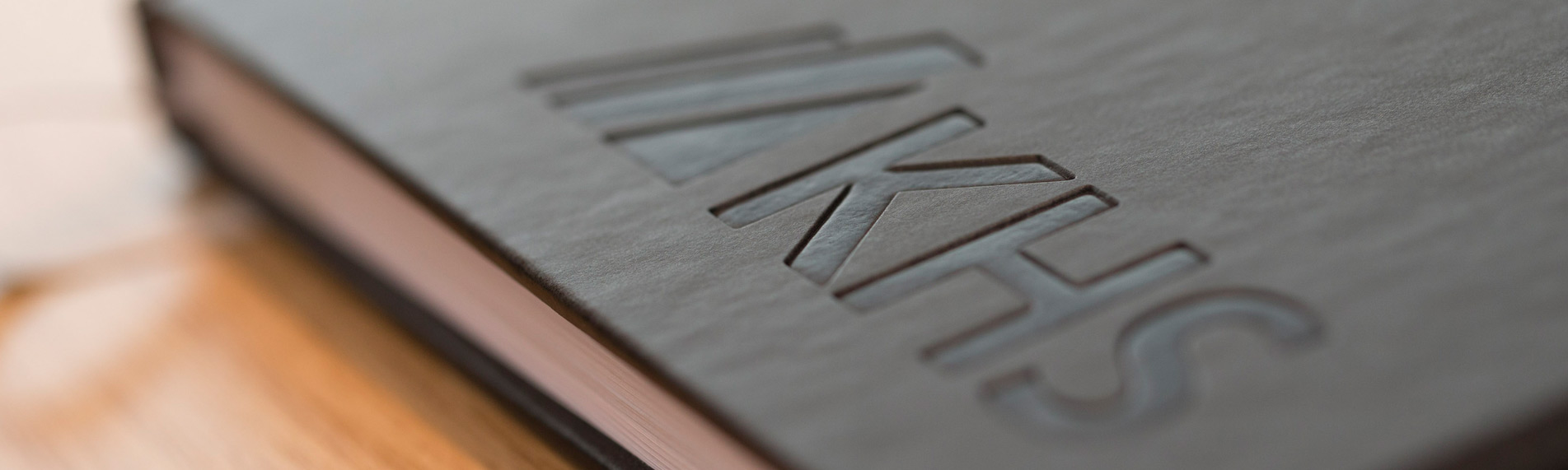
Press Release: China Brew & Beverage 2010
KHS and GLM2 Demonstrate Complete Line Competence for the Asian Market
On a booth measuring over 700 m2 / 7,500 sq ft, international manufacturer of filling and packaging equipment for the beverage, food, and non-food industries KHS GmbH appeared at China Brew & Beverage 2010 together with KHS GLM2, an enterprise that has been part of the KHS Group since 2006. This joint appearance will be marked by the presentation of technical systems that have been made both in China and in Germany. The Innopal AS1H palletizer concept, the Innopas PIISC pasteurizer, and the Innofill DPG-ZMS filling system are manufactured by GLM2, with the Innopro Paramix C dosing and blending system and the Innoket 360 labeler fabricated at KHS plants in Germany. Roland Flach, Chief Executive Officer of KHS GmbH, says, "With our inviting booth at China Brew & Beverage 2010 we would like to stress the great significance the Chinese and Asian market holds for us in general, with particular emphasis on the importance of our Chinese production facility." The Innopal AS1H depalletizing robot on display at the trade show exemplifies a depalletizing concept that is equally suitable for cans and PET and glass bottles. With the Innopal AS1H, pallets loaded with new containers are conveyed to the pushoff level on a pallet lift up a shaft that is enclosed on three sides. Below the pushoff level, the block is centered on all sides by an additional centering bar. A pushoff frame that is enclosed on all four sides gently pushes the containers onto the container table. Pallet liners are automatically disposed of by a pivoting pallet liner remover. The system not only handles packs very gently but also has a fast product changeover and is extremely easy to operate. The double-deck Innopas PIISC pasteurizer also has many advantages, starting with the installation and commissioning of the system in this modular generation of pasteurizers. Preassembled, container-sized modules help to speed up these processes. High process quality is ensured by the use of special clamp nozzles that produce an exceptionally precise spraying pattern that no longer permits overlapping water spraying between the pasteurizer heating zones. The heat balance within the machine is optimized and the water consumption greatly reduced. KHS' PU control safely kills all germs while providing full stability of taste, which is tantamount to a promise of quality. The PU control is based on the temperature/time behavior individually calculated for all styles of product to be pasteurized in conjunction with the respective type of packaging used. KHS' PU control makes it possible to quickly integrate new beverages or new glass and PET bottles or types of can into the pasteurizing process. The Innofill DPG-ZMS filler is a pneumatically controlled pressure filling system with a return gas tube that is chiefly used to fill beer and carbonated soft drinks in glass and PET bottles. The Innofill DPG-ZMS masters the extremely necessary low-oxygen filling process while at the same time specifically saving on CO2. Another advantage of this filling system lies in its high degree of flexibility with respect to both the product and the bottle. The Innofill DPG-ZMS provides perfect hygienic conditions as the system has no external mechanical control devices. Sealing systems fashioned according to the guidelines of hygienic design are used throughout all product and gas passages. With the Innopro Paramix C dosing and blending system, that deaerates, blends, and carbonates all in one, KHS is making provision for the beverage industry's strong desire for innovation the world over, which is also becoming increasingly apparent on the Asian market. One of the distinguishing features of the Innopro Paramix C is its ability to reduce the residual oxygen content in the water to less than 0.3 grams per liter after deaeration. The product is blended through precision mass flowmetering in the syrup pipe train upstream of the mixing pump with the utmost accuracy and also saves on product. The Innopro Paramix C is a three-component dosing and blending system to which a fourth or fifth dosing component can be added if required. It is possible to continuously produce both carbonated and non-carbonated beverages. The Innopro Paramix C is constructed according to the Plug & Produce principle. The system, in which both the deaeration and finished beverage tanks are positioned horizontally, fits into shipping containers and can be transported as one unit with all functional mixer modules fully integrated. Process quality, energy efficiency, reliability, and user friendliness: all these are terms that are applicable to the Innoket 360 roll-fed labeler. To boot, the Innoket 360 also has a completely ergonomic, easy-to-clean hygienic design. All machine parts can be readily accessed by operators, and changeover and servicing times have been reduced to a minimum. For example, a special vacuum drum that can be broken down into various segments speeds up the changeover process and also considerably reduces the handling weight. The highlight of the cutting unit are the self-sharpening cutters that ensure both functional stability and permanent precision cutting. The induction-based gluing system also provides precise and efficient gluing. "With our innovative technical systems and solutions", concludes Roland Flach, "at China Brew & Beverage 2010 we were pointing the way to the future and demonstrating our competence as a turnkey provider. And all of this under the motto of 'Our focus is on the customer, the customer, and once again the customer'."