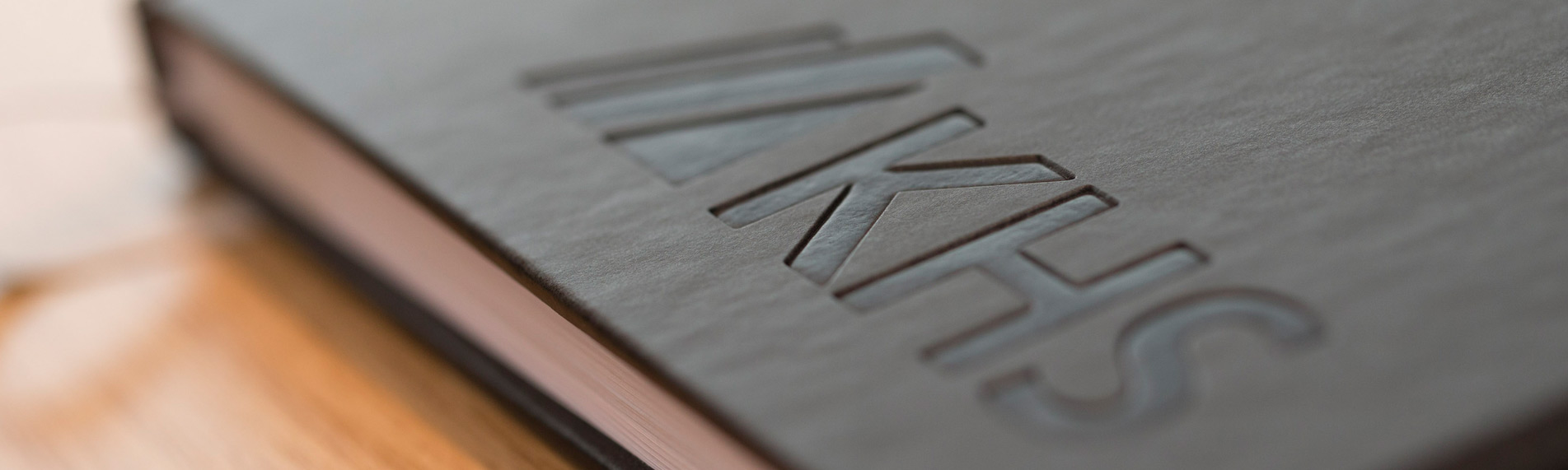
Rothaus takes the next step in glass filling with KHS
Better on all counts: Rothaus recently opted for the KHS Innofill Glass DRS filler and is now benefitting from a number of important new features.
- Innofill Glass DRS with numerous improvements
- Badische Staatsbrauerei Rothaus AG first customer for the new system
- Patented system monitors the filling process and ensures beer quality
Dortmund, January 17, 2019 – Better on all counts: Rothaus recently opted for the KHS Innofill Glass DRS filler and is now benefitting from a number of important new features. This is because KHS has made a number of specific further developments to its glass filler. For the brewery this means reliable, high-performance beer bottling.
The name is not new. For many years now KHS has provided its customers with an established glass bottler in the Innofill Glass DRS which has been frequently adapted to include new features in order to satisfy user requirements. The version of the filler now up and running at Badische Staatsbrauerei Rothaus AG is quite special, however. The flexible inline machine with its 132 filling stations for up to 50,000 bottles per hour provides hygienic filling with low CO2 and product consumption. KHS has considerably improved no less than four areas of the machine, drawing on its 150 years of expertise in brewery machines.
Rothaus fills 0.5-liter and 0.33-liter bottles on its new investment. Fast format part changeovers ensure a high level of flexibility during production planning and line efficiency. To this end KHS provides its hygienic QUICKLOCK fast-acting locking system as the new standard. Bottle guide parts can be exchanged with a few manual adjustments and remain securely in place thanks to the positive fit between the mount and the format part. The conversion time for fillers with a crowner is thus cut by up to 33% to just 15 or 20 minutes. “Simple lever knobs not only release and lock parts; they’re also robust and can withstand broken glass or chemicals,” states Ludwig Clüsserath, head of Filling Technology Development at KHS.
Clever technology in a compact form
In order to prevent bottle breakages from the outset, the Innofill Glass DRS is also equipped with the SOFTSTOP system which is registered as patent pending. This compact, hygienic bottle flowgate is activated at full power. Here, a light barrier measures the distances of the containers as they are fed into the filler. A brake wedge then gently decelerates the bottle flow so that the filling process and foaming take place at a constantly high output. This ensures stable filling quality. No conversions to other formats are necessary and the new braking ramp means that there is no additional scuffing1 and less noise.
Unique selling point for more quality
During the subsequent filling process the unique DIAS diagnostic assistance system carefully logs the filling process. Pressure sensors in every single filling valve monitor the pressure, time and step sequences without interruption. In this way any deviations from the target values are immediately recognized. A further special mention should be given to the fact that the evacuation and CO2 purging processes are monitored to ensure low oxygen pickup. Broken bottles are consistently detected across the entire processing angle and a bottle burst routine2 triggered. The sensor data can be invoked as a pressure graph on the monitor. "This gives operators the chance to detect any faults as quickly as possible," states Clüsserath. In practice this not only makes fast, targeted repairs possible and relieves operator workloads but also provides a basis for preventive maintenance. This data enables results to be statistically evaluated, with the help of which future sources of error can be eradicated in advance. This in turn ensures consistent quality and the continuation of ongoing operation.
Another significant feature is the camera-controlled OPTICAM HPI control system. The foam generated by HPI3 displaces the residual oxygen from the bottle and is thus of great importance for the quality of the beer. As the foaming is dependent on various parameters in the filling process, however, with its new OPTICAM system KHS enables the head of foam to be constantly monitored and regulated irrespective of the machine operator. This means that Rothaus can not only prevent undue beer loss due to excessive foaming but also detect and reject bottles with insufficient foaming. If the beer error rate becomes too high, production is stopped and the operators can read off the cause of the fault from a clear analysis report.
With the inclusion of the SOFTSTOP, DIAS und OPTICAM options the entire KHS system at Rothaus safeguards the quality of the beer throughout the entire filling process with these mechanical and digital system solutions.
1 In the beverage industry “scuffing” describes the visible marks left on the widest part of a bottle. It occurs on conveyor belts or in crates.
2 Bottles which burst or break during filling are detected and removed from the production process by a fixed routine to prevent other containers from being contaminated by any fragments of glass, for instance.
3 To reduce the amount of residual oxygen in the bottle a fine jet of water is sprayed into the beer to make it foam. This is known as high-pressure injection or HPI.
About the KHS Group
KHS is one of the leading manufacturers of filling and packaging systems for the beverage, food and non-food industries. The KHS Group includes the following companies: KHS GmbH, KHS Corpoplast GmbH, NMP Systems GmbH and numerous subsidiaries outside Germany.
KHS GmbH manufactures modern filling and packaging systems for the high-capacity range at its headquarters in Dortmund, Germany, and at its factories in Bad Kreuznach, Kleve and Worms. The KHS Group's PET expertise is pooled at KHS Corpoplast GmbH in Hamburg, Germany, where innovative PET packaging and coating systems are developed and produced. NMP Systems GmbH, a wholly-owned subsidiary of KHS GmbH based in Kleve in Germany, designs and markets new, resource-saving packaging systems.
In 2017 KHS and its 5,070 employees achieved a turnover of around €1.137 billion. The companies in the KHS Group are 100% subsidiaries of the MDAX-listed Salzgitter AG corporation.
50,000 bottles per hour
The flexible machine with its 132 filling stations for up to 50,000 bottles per hour provides hygienic filling with low CO2 and product consumption.
Download image (JPG, 4 MB)132 filling stations
The unique DIAS diagnostic assistance system carefully logs the filling process. Pressure sensors in every single filling valve monitor the pressure, time and step sequences without interruption.
Download image (JPG, 2 MB)KHS Innofill Glass DRS glass bottle filler
Rothaus has opted for the KHS Innofill Glass DRS filler and is now benefitting from a number of important new features.
Download image (JPG, 7 MB)Rothaus Tannenzaepfle
Rothaus fills 0.5-liter and 0.33-liter bottles on its new investment.
Download image (JPG, 2 MB)Satisfied partners
Mike Herrmann (sales manager for KHS), Daniel Schnitzer (filling operations inspector at Rothaus) and Ludwig Clüsserath (head of Filling Technology Development at KHS).
Download image (JPG, 4 MB)