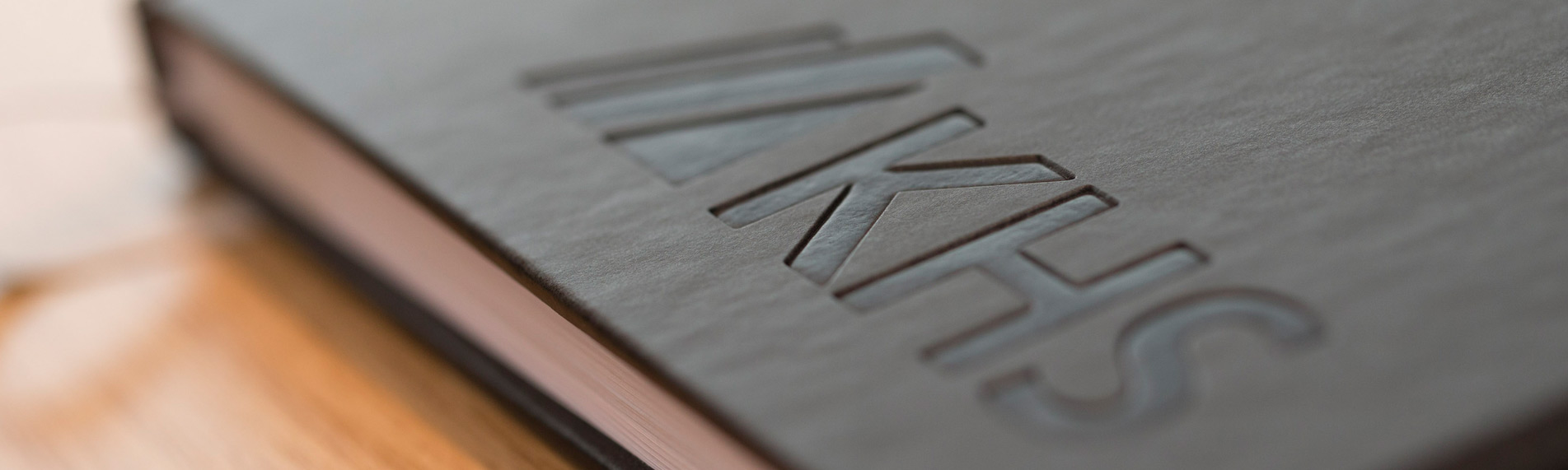
Top Packaging Criteria Met
New generation of modular KHS shrink tunnels centers on energy savings and packaging quality
Werner Ageling* Werner Oster** What's popular the world over and enhances the impact of brand name products at the point of sale in its own particular way? The shrink pack! Products shrink wrapped in clear, unprinted film make direct contact with the consumer. Wrapped in printed film, the advertising message is brought across by the many variations and permutations of film printing. What's vital for the optimum communication of all brands, however, whatever the type or design of film, is perfect shrink results. And this is what KHS achieves with shrink technology that has been meticulously planned right down to the last detail. So that it can better meet the individual requirements of beverage, food, and non-food companies who pack their products in film, KHS is now launching a new shrink tunnel concept to market that enables all kinds of specific demands to be catered for by a standard system which can be expanded at will using a series of modules. This not only enables the exact specifications stipulated by any one company to be complied with; at the same time, the new shrink tunnel concept that has now been standardized for both the Basic and Advanced series of KHS machines holds maximum potential for the future, as various additional functions can be subsequently incorporated at any time as and when the occasion arises. Six shrink tunnel sizes The new generation of KHS shrink tunnels is available in lengths of four, six, and eight meters (approx. 13, 20, and 26 feet) and widths of between 700 mm and 1,000 mm or approx. 28" and 40". There are thus six different shrink tunnel sizes in the program. With each planned investment in new shrink tunnel technology, KHS records the particulars of individual packing tasks. * Product Management Manager, Packaging Technology Competence Center, KHS GmbH, Kleve. Phone: +49 (2821) 503-237 * Product Support Manager, Packaging Technology Competence Center, KHS GmbH, Kleve. Phone: +49 (2821) 503-152 Based on this information KHS then makes recommendations to companies on the type of shrink tunnel best suited to their requirements. This consultancy service includes KHS providing detailed information on the many helpful options that can be incorporated on the basic platform. Improved flow principle During the development of the new shrink tunnel concept the heating system was thoroughly investigated. Optimizing the heating chamber and introducing new ventilators that work much more efficiently than those of the previous generation have resulted in an improved flow principle that permits energy savings of up to 15%. This optimized flow performance has also enabled the number of ventilators to be reduced, with each of the six shrink tunnel variants now only needing two heating chambers with one ventilator apiece. This also means that less maintenance is required – and that fewer spare parts are needed. The energy-saving package With the energy-saving package that can be integrated into the new shrink tunnel concept, energy savings of up to 20% as opposed to previous systems are possible. This energy-saving package includes a newly developed roller shutter system that automatically closes the product infeed and discharge openings of the shrink tunnel when the packaging machine has stopped, largely preventing any thermal energy from escaping. The energy-saving package also has electronically controlled standby operation, where the energy consumption of all functional units necessary to the shrink process is reduced to a minimum. All functions switch back to normal operation as soon as the production process requires that they do so. At the same time, the heater regulates the heat back up to operating temperature within a few minutes with the help of a booster function. If we consider that many production sites have long line downtimes caused by product changeovers and the use of different pack formations or containers, during which the shrink tunnel was in a constant state of operational readiness to date, investing in the energy-saving package not only promises to significantly cut energy consumption but also costs. Gas or electric heating – both are possible The new shrink tunnel concept also allows for the use of the Eco shrink tunnel that is heated by gas instead of the electricity ordinarily used in the past. The Eco shrink tunnel concept lives up to its name in that it uses up to 50% less energy versus the electrically heated shrink tunnel. This percentage is a rough estimate, since energy costs vary from country to country, and the energy cost savings are ultimately based on the difference in electricity and gas prices in the region in which the Eco shrink tunnel is installed. Another positive aspect of the Eco shrink tunnel is that the environment benefits from a reduction in CO2 emissions of up to 60%. All that's needed to operate the gas heater built into the Eco shrink tunnel is a gas connection – another important aspect of this option. Air supply and exhaust ducts are not necessary. The gas heater works using what is known as porous combustion technology. This means that a classic combustion chamber does not have to be provided because there is no open flame. The high power density of the porous burner of up to 3,000 KW/m² enables its design to be extremely compact. Combustion is so complete as a result of the porous combustion technology that no residue remains and no soot is formed. Compared with electric heaters, the temperature can be configured more quickly and accurately on the porous burner unit and heating times are much shorter. Hygienic design Yet another positive feature of the new generation of shrink tunnels is its cubic machine body, already established in the Advanced series, which creates more space in the shrink tunnel area, among other things. The larger outside surfaces of the machine constructed in accordance with Hygienic Design make exterior cleaning easier. The twin-walled cladding allows cable routes to be used. Another plus point is that insulating the shrink hood with insulating elements means that there is no heat bridge from the inside to the outside of the shrink tunnel. Thermal energy thus remains where it should be, namely inside the tunnel hood. Variable hot air nozzles for optimum shrink results In order to achieve the best possible shrink result for each individual shrink pack, KHS uses adjustable hot air nozzles. The air flow can be set exactly as required to fully suit the individual pack format with regard to both height and width. The amount of air required for a perfect shrink result can be configured for each individual nozzle, either manually or electronically using servo motors. Nozzles can also be 'parked', a feature that proves especially useful when a product program requires operation both in a single and in multiple lanes. This ensures that hot air is always precisely directed to where it's needed for optimum shrink results. Format changeovers as required The nozzles are positioned for various pack formations manually by adjusting spindles and using a digital position indicator. The nozzles can also be positioned using electronic operator prompting. The advantage of spindle adjustment by the operator is that he or she is informed by the machine operator panel as to which stations of the machine have to be adjusted. At the same time, with operator-prompted format changeovers using an electronic display, information on what the operator must do at the individual stations is accurately communicated. Besides avoiding paper lists that are often not maintained, the electronic display also takes the mechanical play of gear wheels and chains into account. This ensures that shrink results for various formats are precisely reproduced and that operator errors are largely eliminated. If electronic operator prompting is used, it is of course possible to make use of AccuDrive at a higher level of configuration. Four steps to perfect shrink packs Packs are shrink wrapped in the shrink tunnel area in four steps. Firstly, hot air is directed at the base of the pack. This seals the overlapping film surfaces on the pack base. At stage two of the process the film is inflated; to this end, hot air is pumped into the pack which expands like a balloon. It is important to maintain this balloon-like state for as long as possible for an optimum shrink result. Thirdly, the pack is shrunk by the air supply slowly being decreased. The fourth and final stage at the shrink tunnel discharge involves the targeted cooling of the new shrink pack. An optional cooling unit is available for specific use in warmer climates. Safe conveying for maximum pack quality The type of conveying chain used in the shrink tunnel area depends on the stability of the product being conveyed. Packs with cardboard pads require a bar chain and film packs a wire link belt. The drive chains previously used have now been replaced by low-noise, maintenance-free toothed belts. Gentle transition points In designing the new generation of shrink tunnels great importance was attached to gentle pack transition points. Where the tempo varies on the packaging machine according to the production volume, in the shrink tunnel a constant speed is crucial for a perfect shrink result. For this reason a special functional unit has been installed between the packaging machine and the shrink tunnel which compensates for the difference in speed between these two machine sections. The transfer of the new shrink packs to accumulation conveyors downstream of the shrink tunnel has also been designed with the utmost care of the product in mind. Automatic conveyor chain cleaning Another shrink tunnel option is the integration of an automatic cleaning system for conveyor chains made of wire mesh. This system consists of a counter-moving stainless steel brush located underneath the conveyor chain which is engaged at fixed intervals. Film debris and particles of dirt removed from the conveyor chain are swept into a drawer that can be easily emptied, thereby eliminating the need for time and work-consuming manual shrink tunnel cleaning processes if this option is selected. Shrink tunnel lighting Optional hood lighting gives operators a clear view of the hood interior. This makes any fine adjustments that have to be made by operators or maintenance personnel to the shrink process immediately visible. Camera system for precise monitoring The lighting setup can also include a camera system integrated at the discharge of the shrink tunnel. This system transmits image files to a monitor installed next to the shrink tunnel; images can either be in black-and-white or color, depending on the option chosen, enabling the shrink process to be conveniently observed from outside. When camera technology is applied, an 'air curtain' is used in place of the standard hanging curtains in the shrink tunnel infeed and discharge for unobstructed viewing. This air curtain works on the same principle as those we are familiar with at the entrance and exit areas of department stores, acting as a barrier that encloses the temperature in the shrink tunnel just as reliably as the conventional hanging curtain system. Plenty of future potential included All considered, this new generation of shrink tunnels is a concept that can be tailored to meet very individual requirements. High security of investment is ensured by the extremely high quality of the machines – as to be expected where KHS is involved – and also by the fact that all functions can be retrofitted at a later date. The energy-saving package, the Eco shrink tunnel, automatic conveyor chain cleaning, additional pack cooling: should customers find they require the one or the other extra after initially operating the new shrink tunnel without, they can upgrade at any stage for even more future potential.