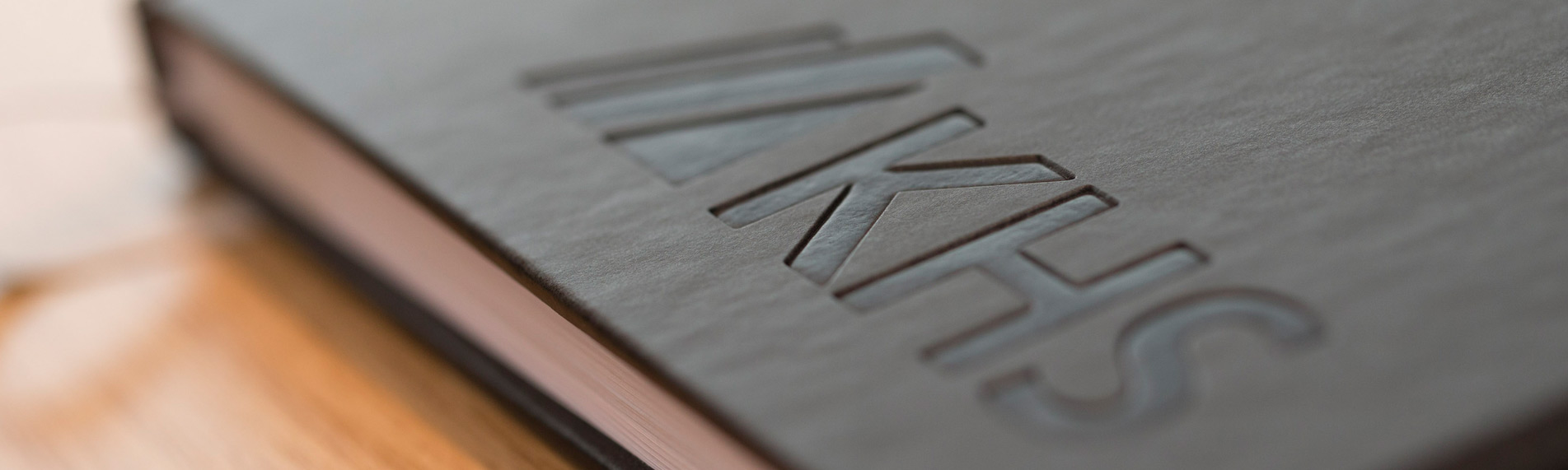
Tradition and Innovation
Stiegel brewery invests in KHS bottle washing technology with many innovations, including the new Everjet spraying system
Knut Soltau**
Daniel Wald**
At the Stiegl brewery in Salzburg, Austria, the "beer of the Austrians" is brewed with a great passion for the trade. First mentioned in 1492, the brewery has been in private ownership for over 500 years. Since 1990 the company has been headed by Dr Heinrich Dieter Kiener, who personally guarantees the quality of 'his' beers. Both the personality and philosophy of this family enterprise are what have turned the tiny Salzburg tavern located on the steep, narrow street of An der Stiege (hence the name "Stiegl") into what it is today, namely Austria's leading privately owned brewery. Stiegl combines quality, innovation, and responsibility towards the environment to make up a recipe for success that is mirrored in part in its new, modern bottle washing technology. In this respect Salzburg's popular private brewery has opted for a single-end Innoclean SE bottle washer from KHS. Equipped with many innovations, the machine was chosen not just for reasons of sustainability but also for its savings potential and adherence to the highest standards of hygiene. Among other features, incorporated in the Innoclean SE are the new Everjet spraying system that is especially hygienic and also extremely low maintenance; the innovative Liquid Efficiency Spraying System (LESS) which specifically saves energy at the spray pumps; automatic internal washing, energy-saving bottle carriers, and Triple-i-Drive technology. Engineer Karl Sigl, plant maintenance manager at the Stieglbrauerei, to give it its Austrian title, says, "The many highlights of our new bottle washer are totally convincing on all counts. Our absolute top priority is that the quality of the cleaned bottles is right. This becomes even better if in this conjunction we can also talk about environmental friendliness, energy savings, and ease of operation."
* Product Management, Bottle Washing Machines & Pasteurizers Competence Center, KHS GmbH, Dortmund. Phone: +49 (231) 569-1887
* Product Development Manager, Bottle Washing Machines & Pasteurizers Competence Center, KHS GmbH, Dortmund. Phone: +49 (231) 569-1195
Largest private brewery in Austria makes highest demands of quality
"I personally vouch for the quality of our beers. This starts with our strict adherence to the purity law of 1516, through the use of first-class raw materials and ingredients to the expert brewing skills of our master brewer," says brewery boss Heinrich Dieter Kiener, who employs around 750 people. Top quality has always been of the utmost concern at Stiegl, which is why the brewery naturally also insists on using the best possible raw materials, quality production processes – and of course state-of-the-art technology.
The new KHS Innoclean SE bottle washer cleans 44,000 bottles an hour
The new KHS Innoclean SE bottle washer easily meets the Stiegl standard. It is able to process 44,000 bottles per hour, currently cleaning both 0.5-liter NRW and Stiegl's special 0.33-liter glass bottles.
The bottle washing process
As far as the bottle washing process within the Innoclean SE is concerned, the first step is the draining of residual liquids. Bottles are tilted for a short time in order to remove any beverage residue. Residual liquids are reliably discharged from the machine by a special system of ducts. The draining of residual liquids is followed by several stages of pre-soaking to pre-heat the bottles. Another important aspect is the pre-softening of any dried beverage residue clinging to bottle walls.
The ensuing pre-washing procedure takes place at an increased pressure with two rotating spray tubes. Like all of the other spray tubes in the bottle washer, these meet the specifications of the new Everjet spraying system. Rotating sprays move synchronously with the travel of the bottle pockets and thus with the bottle mouths. The resulting long spray time ensures a maximum cleaning effect in the bottle in conjunction with a turbulent distribution of liquid.
In the caustic bath, specific flow regulation combined with submerged caustic flushing ensures that removed labels are quickly discharged. This effectively reduces pulping of paper labels. The upper caustic flushing stage provided at the end of the caustic immersion bath removes any remaining labels which, like the labels removed earlier, are discharged by a sieve belt. These 'remaining labels', for example, include those stuck to bottle bases.
In the post-caustic bath the bottle exteriors are rinsed by two fixed sprays while two rotating sprays wash out the insides of the bottles. The fixed sprays of Stiegl's bottle washing machine are primarily responsible for washing bottle exteriors and rotating sprays for washing bottle interiors. Next, the bottles travel on to the three water zones. From zone to zone the focus is switched from combined bottle interior and exterior washing to interior bottle treatment only. A final interior spray with fresh water completes the rinsing and recooling process in the water zones.
Newly developed Everjet spraying system with plenty of extras
A very special highlight to be included for the first time in the Innoclean SE delivered to the Stiegl brewery is a newly developed, particularly hygienic version of the spraying system. In the past, the spray box and spray tubes were quadratic. This had the disadvantage that the many horizontal surfaces were especially susceptible to soiling, making maintenance a time-consuming undertaking. The new Everjet spraying system now features a tubular frame whose dividing rails ensure that the spray tubes are precisely aligned. The cylindrical design also means that no dirt is able to accumulate right from the start. Maximum hygiene is also provided by protecting the fastening units with covers and thereby reducing the number of components to an absolute minimum.
Another benefit of the new system is that after removing and reinstalling the spray tubes for cleaning, for example, they do not have to be readjusted to provide perfectly regulated spraying. The tubes are sealed using the so-called Thermos bottle principle. All this means that opening and closing for cleaning and maintenance can be done quickly by hand, without the need for any tools whatsoever. Another positive aspect of the new system is that spray nozzles and spray tubes are no longer screwed together but joined by a snap-on fitting. This greatly reduces the number of corners and recesses where dirt can collect. This also simplifies installation – and especially any necessary maintenance measures.
Another improvement lies in the increased service life of the driver stars. In place of the classic roller bolts used to date, the new spraying system uses mounted rollers for the driver stars which, as opposed to the sliding friction of previous setups, generate a much lower rolling friction between the bottle pocket carrier and star. This greatly reduces the amount of wear.
Yet another important point to note in the recently introduced Everjet spraying system is that the spray tubes are supplied on both ends. The standard practice to date was to feed the water used to wash the bottles to just one end of the spray tube. The disadvantage of this was that the flow rate ebbed towards the end of the spray tube. Despite the presence of venting holes, this meant that particles could accumulate at the end of the tube. As perfect spraying is no longer guaranteed to its full extent when the nozzles are clogged, regularly cleaning of the spray tubes fed on one end only was thus inevitable for reasons of hygiene.
The situation is very different with the new two-end spray tube feed. A hole integrated in the center of each spray tube encourages the controlled discharge of particles. This causes swirling in the middle of the spray tube that prevents particles from accumulating. Marco Kaulas, manager of filling and packaging technology at Stieglbrauerei, elaborates. "Our new KHS bottle washer has been in operation for over a year now. In this time we haven't once found any blocked nozzles. This not only saves us a great amount of time for removal and cleaning but also gives us the added security that all bottles are perfectly sprayed at all times in accordance with our high standards of quality."
The opening of the nozzles on the individual spray tubes has also been well engineered in the Innoclean SE spraying system, with each opening precisely timed to coincide with the other. When the nozzles on one spray tube close, the nozzles of the next one open. This keeps the pressure uniform within the system and rules out the eventuality of pressure surges. This ensures gentle treatment of all mechanical components.
Liquid Efficiency Spraying System for even greater energy savings
Targeted energy savings are possible with the Innoclean SE thanks to its new savings highlight, namely the Liquid Efficiency Spraying System with the appropriate acronym of LESS. This is a system with the aid of which the frequency control of the spray pumps is constantly geared towards the actual operational status of the bottle washer. Here, the pumps are not switched off should the washer come to a standstill; instead, the pump speeds are greatly reduced. This ensures that the bottles are always covered with water. Energy savings of around 75% can thus be expected should the bottle washer come to a temporary halt due to a backup of containers in the system. At the same time, LESS helps the Innoclean SE to restart quickly and thus rapidly reach its nominal capacity.
Automatic instead of manual internal cleaning
In place of classic manual internal cleaning the Innoclean SE makes use of automatic internal sanitization at the end of production. This additional feature helps to save water and also ensures a more efficient cleaning process as opposed to the former manual setup.
Energy-saving bottle carriers reduce heat and water consumption
During the cleaning process the bottles are conveyed by energy-saving bottle carriers patented by KHS that are equipped with plastic bottle pockets. Thanks to the improved rinsing capabilities of the energy-saving bottle carrier only a minimum amount of cleaning solution and heat is carried over from zone to zone. Compared with conventional steel carriers, using energy-saving bottle carriers can save 10–15% of heat, 15–20% of water, and a considerable amount of chemicals. The reduced amount of drive energy needed is yet another positive aspect of the energy-saving bottle carrier. A further important factor is that in spite of its lighter weight, the energy-saving bottle carrier is capable of handling all conceivable loads in the bottle washer equally as well as the closed steel version. Furthermore, the plastic bottle pockets can be quickly replaced as required.
Maximum flexibility thanks to the Triple-i-Drive concept
The Innoclean SE at the Stiegl brewery is equipped with Triple-i-Drive technology. In this system each drive has its own servo motor and converter. During operation, slight deviations in the synchronization can thus be automatically corrected, providing the drive system with maximum protection. Proactive maintenance is possible by trimming the current consumption at each drive. Triple-i-Drive technology also ensures high availability, with short product changeover times made possible by decoupling the main drive and the infeed and discharge. Optimum bottle handling results in a reduction in intervention and conversion times. The time and effort required for maintenance is also considerably cut by using fewer parts and specially configured control functions.
Strong environmental awareness taken into account
"Innoclean SE's economical use of resources takes Stiegl's strong awareness of the environment into full account," says Kaulas. "We are naturally also pleased about the savings potential this gives us. However, the definitive reason for Stiegl reinvesting in KHS bottle-washing technology – and I can't say this often enough – is the high washing quality this investment offers us."
Master brewer Christian Pöpperl confirms this. "As the largest privately owned brewery in Austria we want to continue to brew Austria's favorite beer. For this reason we attach great importance to the art of brewing at its highest level and thus to consistent high quality at all levels."
And that just about says it all.