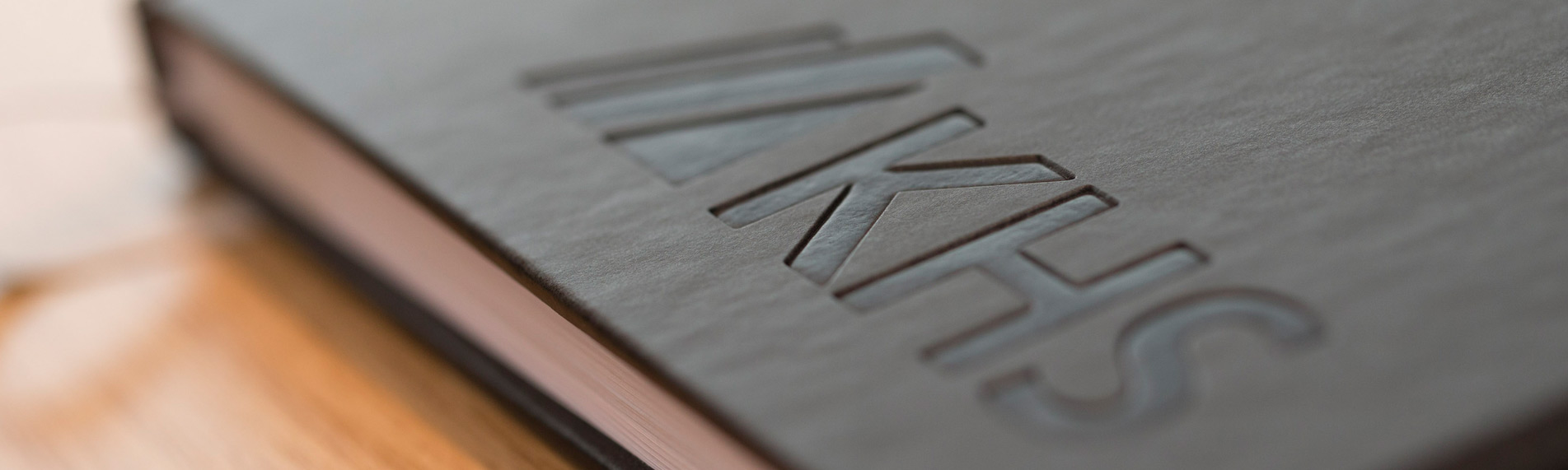
Unique Position on the Market
Monoblocked KHS InnoPET BloFill system now with half load
The demand for beverages in PET bottles is on the increase worldwide. Predictions for the future also reckon with further growth. Cutting down on costs in the manufacture of PET bottles and in the field of filling and packing technology as a whole is also a topic of increased discussion. With this in mind, KHS has now developed InnoPET BloFill, a monoblocked stretch blow molder/filler/capper system that has a whole host of advantages. Using an InnoPET BloFill setup as opposed to traditional PET bottle manufacturing and processing equipment incurs lower costs for investment and production. There are also the added benefits of increased line efficiency, minimized space requirements, and lower operator involvement. Another innovation that speaks for the InnoPET BloFill system is the ability to only half load the stretch blow molder even within the monoblock concept. This enables even more flexible coordination of the various components in the monoblock. Another important plus point is that the half-load option can also lead to a marked decrease in investment costs. The half-load concept is of particular interest to beverages companies who mainly process smaller PET bottles but occasionally also larger sizes, such as 1.5-liter PET containers, for example. If, for example, the 0.5-liter PET bottle is the container type of choice and the half-load option is selected, the filler can be set for a capacity of 36,000 0.5-liter PET bottles, and is thereby considerably smaller than with a suboptimum capacity of approx. 26,000 1.5-liter PET bottles. In this case, the filler can be equipped with 25% fewer filling valves. This results in a significant reduction in the cost of investment. At the same time, 1.5-liter blow molds only have to be invested in for every second blow station on the stretch blow molder. It goes without saying that filling systems require much longer to fill 1.5-liter PET bottles than 0.5-liter containers. The number of 1.5-liter PET bottles the stretch blow molder – the lead machine in the monoblock – passes on to the filler under the given conditions is thus correspondingly lower. And this is where the half-load concept comes into play. Running at half load, preforms are assigned to every second position on the stretch blow molder. When 1.5-liter PET bottles are passed on to the filler, a transfer wheel with special gripper arms accesses every second stretch blow station. The bottles are then transported to the filler transfer star so that all filling positions are assigned and filling can commence without further ado. The given example is just one of many conceivable variations. The InnoPET BloFill system can process all sizes of bottle from the 0.2-liter to the 2-liter PET. On request, special formats can also be processed. An alternative to the half-load concept would be to replace the stretch cams in the blow molder and set the stretch blow molder to a lower output capacity. The resulting conversion would take several hours, however – each and every time this was done. Frank Haesendonckx, Product Manager, Stretch Blow Molders, KHS Corpoplast, says, "With the half-load option, the monoblocked stretch blow molder/filler/capper InnoPET BloFill system has a unique position on the market. The decades of KHS Corpoplast stretch blow molder and KHS filler competence that have been poured in full into the monoblock concept wholly endorse the new system. The InnoPET BloFill monoblock is an extremely efficient system." Within the InnoPET BloFill concept, InnoPET Blomax stretch blow molders can be monoblocked with all KHS filler and capper systems designed for the filling of PET bottles. As KHS has the right PET filler and capper system for every type of beverage, the InnoPET BloFill monoblock concept can be used to process a very diverse range of beverages. Whether carbonated or still beverages, beer or sensitive fruit and milk beverages are to be bottled in PET, practically every product destined for filling can be processed. With its Life Cycle Solutions, KHS partners the beverages industry throughout the entire operating life of a customer's machinery and plant equipment, with the aim of achieving ceaselessly efficient and economic operation of plant equipment throughout its entire life cycle.