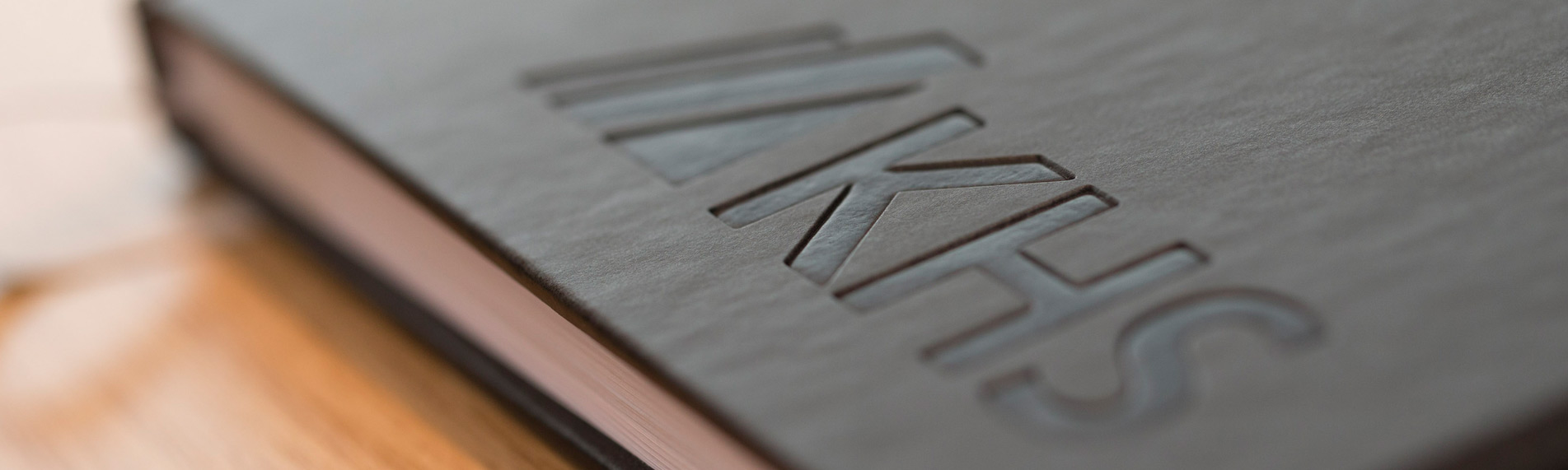
Even More Sustainability, Lower Operating Costs, and Greater Space Savings
The new KHS ultra-clean concept with the integrated mini hygiene housing offers numerous advantages
With its newly designed ultra-clean concept, KHS fully meets the demands of the beverage industry. Compelling are criteria such as increased sustainability, flexibility, cost reduction, and space savings coupled with maximum microbiological safety.Monoblocking the InnoPET Blomax Series IV stretch blow molder and the filler/capper system is prerequisite for this new system. The filler/capper system is integrated into what is known as a mini hygiene housing. What is special here is that unlike conventional glass hygiene housings, the floor area of the mini hygiene housing is enclosed which provides perfect protection from all outside influences. As its name suggests, the mini hygiene housing takes up very little space; about 40% less than the space required for classic hygiene isolators implemented in the past which also reduces detergent and sterile air consumption by approx. 20%.
The measures taken to meet the requirements for ultra-clean filling of sensitive beverages such as fruit spritzers, slightly sparkling health and sports beverages, fruit juices containing preservatives, and non-alcoholic beer already begin at the stretch blow molder. Here, the heater area is equipped with a sterile chamber module where preforms are sterilized separately by a newly developed preform sterilization system. A sterile air airlock reliably separates the sterile chamber at the preform infeed as well as the discharge from the remaining heater area. The preforms are held in place during the entire heating and sterilization process by an active mandrel that has side openings through which a mixture of hot air and hydrogen peroxide flows directly into the preform body. All interior surfaces of the preform are sterilized equally reliably as the preform mouth. Final treatment in the sterile chamber module involves blowing sterile air around the entire body of the preform.
The preform is transferred from the active mandrel to the gripper system and finally to the blowing station after application of the preset heating profile within an enclosed area in which a continuous downward flow of sterile air prevails. The same principle is used when the freshly blown PET bottles are removed from the stretch blow molder and transferred to the transfer segment leading to the filler/capper system. The PET bottles first pass through a sterile airlock located inside the transfer area that keeps the dry area of the blow molder strictly separated from the wet filler area. The bottles pass through a cooling module in the next step. A new feature in this area: water with chlorine dioxide added is used that not only cools but also sterilizes the bottle bases. Perfect bottle sterilization is thus achieved in conjunction with the preceding preform treatment that focuses chiefly on sterilizing bottle interiors, bottle mouth areas, and bottle side walls.
Located above the enclosed transfer segment is a HEPA (high efficiency particulate air) filter that provides a constant supply of sterile air. Similar to the transfer area, a sterile air atmosphere is continuously maintained in the area of the mini hygiene housing that flows out of the system parallel to the bottle flow in the filler and capper area up to the bottle discharge where it is either finally discharged to the production shop or specifically extracted. In the mini hygiene housing, the air is additionally discharged through openings in the upper and lower areas of the devices created by the overlap of the rotating machine carousel and the stationary components.
Only the bottles, the bottle grippers, and the filling spouts are integrated into the mini hygiene housing in the area of the filling system while the filling valves, product bowl, electronics, and control systems are located outside the hygiene area together with the servo drives of the capping elements. Cleaning nozzles are installed in such a way that they perfectly reach the transfer stars, filling valves, and capper elements, as well as all interior surfaces. Exceptionally reliable automatic sanitizing is a given. The cleaning circuits are fed by a newly developed KHS hygiene center that, among other things, incorporates the chlorine dioxide preparation unit.
The filling system used to optionally fill carbonated or non-carbonated beverages is an Innofill DRV-UCF that operates according to the principle of volumetric, electromagnetic inductive flow metering. A special feature here is the twin control of certain functions in the filling valves, which eliminates a considerable number of gas valves with pneumatic and electrical control and thus reduces the cost of maintenance and repairs. Each of the filling valves can nevertheless be switched individually. A filler equipped with 140 filling stations, for example, now only requires 280 gas control valves instead of 420. When filling products in an inert gas atmosphere (e.g. using CO2), the proportion of inert gas in the pressurized bottle can be freely adjusted depending on the oxygen sensitivity of the beverage being filled. Adapting the filling atmosphere to the requirements of the particular type of beverage reduces CO2 consumption costs. The Innofill DRV is the only filling system that does not require separately controlled lifting elements to press bottle mouths against the filling valves. Bottle mouths are sealed against the filling valves by transferring the pressure inside the bottle to the neck ring holder via an aseptically designed expansion joint located inside the filling valve. For a filler equipped with 140 filling stations, for example, this eliminates yet another 140 pneumatic cylinders including the related pneumatic and electric control elements. At the same time, the contact forces are very exact. If the filling pressure is high, the bottles are pressed against the valves with the accordingly greater amount of force while lower contact pressure is required at low filling pressures. This method not only handles plastic bottles particularly gently, it also reduces the number of wear parts, lengthens the periods between maintenance intervals, and increases the efficiency of the filling system.
A drop of liquid nitrogen can be placed in the head space of each bottle when filling non-carbonated beverages to achieve exceptionally high bottle stability. The Innofill SV-ACF screw capper is the capping system of choice.
The InnoPET BloFill ultra-clean monoblock, equipped with an integrated mini hygiene housing capable of processing up to 60,000 plastic bottles per hour ranging in size from 0.1 to 3 liters, is controlled by the multiple-award winning KHS HMI operator panel (Red Dot Award and iF award).
KHS Microsite - drinktec