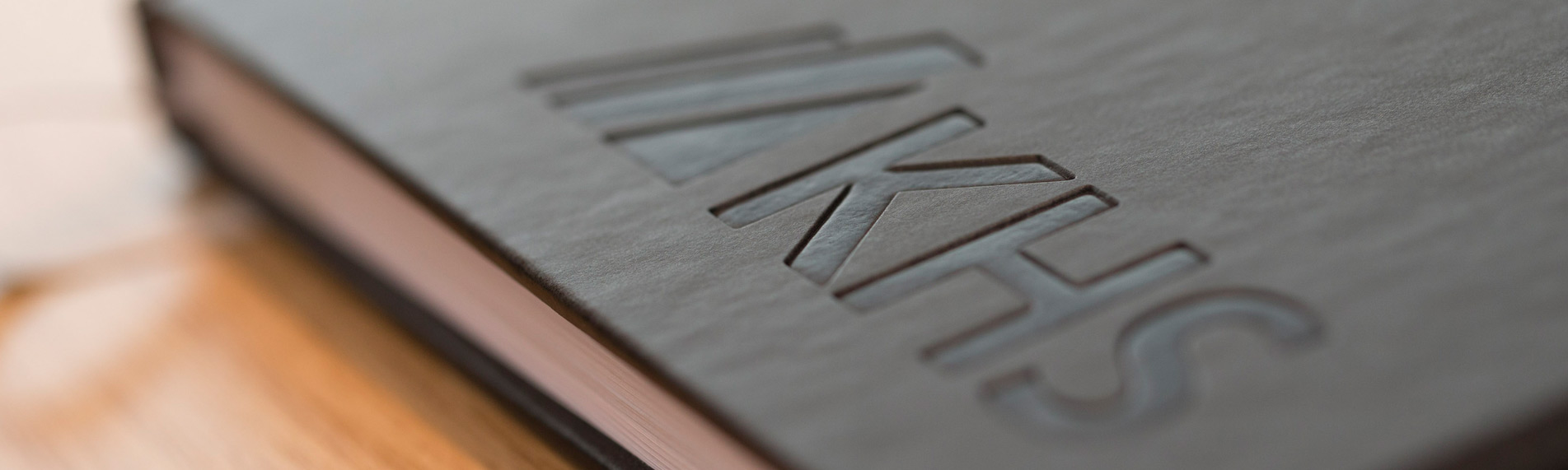
For the bottling of still water under ultraclean conditions
KHS presents new mini hygiene housing
With the launch of a new mini hygiene housing for the ultraclean filling of water in PET bottles KHS is meeting a major demand voiced by the beverage sector. Whereas the glass hygiene housing usually found in ultraclean applications is open to the floor, the base of the mini hygiene housing is closed. This means that the filling area is completely sealed and thus protected from any outside influences. Another advantage of the new mini hygiene housing is that the system takes up very little space, thus cutting costs and generally saving over 30% of space compared to standard systems. The consistent implementation of hygienic design creates perfect conditions for fast and efficient cleaning where the amount of air and cleaning agents consumed is also lower than in conventional sanitary rooms. The mini hygiene housing is chiefly destined for equipment where the stretch blow molder is monoblocked with a filling machine. If required, it can also be used where bottles are fed in by an air conveyor. In the monoblock concept the bottles first pass through an airlock after being stretch blow molded. This airlock ensures that the wet area of the filler is kept completely separate from the dry area of the blow molder, thereby eliminating the risk of corrosion in the blow molder. When using the mini hygiene housing sterile air is permanently applied to the transfer stars leading to the filler section. Here, HEPA (high-efficiency particulate air) filters are integrated into the system to provide a constant supply of sterile air. In the filler and capper area the flow of sterile air, which is kept at a slight overpressure, is conducted parallel to the bottle flow up to the point where the bottles leave the system. Pressure control and pressure monitoring equipment can be included as options. The air in the system is removed through strategically positioned openings in the upper and lower area of the machine which are created by the overlap of the rotating machine carousel and the static components. After the capping process the sterile air can be optionally extracted and discharged. This is especially recommended if water containing ozone is scheduled for filling. The setup includes an Innofill NV filling system which processes various sizes of bottle holding from 0.1 to 3 liters at rates of between 15,000 to 72,000 bottles per hour. There are also systems for different types of bottle mouth available. The Innofill NV non-contact filling process with a free-flow filling valve gives customers microbiological and hygienic safety; the bottle mouths are neither pressed nor sealed against the filling valves and there is no contact between the valve components and the bottle mouths. As a result, there is no question of product wetting. The Innofill NV also uses volumetric impeller flow metering. This is a very simple, proven system of measurement based on the volumes of liquid transported in the impeller areas. These measurement devices have been specially developed to measure beverage volume flows, taking all aspects of hygiene into full account. Signals are transmitted without contact to an integrated sensor that derives the relevant fluid flow rate from the measurement signals. Impeller flow metering enables demineralized water to be filled that does not have a significant measurable level of conductivity. Electromagnetic inductive flow metering can also be implemented if desired. The closure system used here is an Innofill SV-ACF, a computer-controlled screw capper which fully adjusts to the individual specifications of the closures used. The distinct separation of capping movements into rotational and vertical motions and a sophisticated hygienic design that provides perfect cleaning conditions are in full keeping with the concept of hygienic filling. Cleaning nozzles have been installed in the mini hygiene housing that are specifically aimed at the transfer stars, filling valves, capper elements, and all interior surfaces for perfect results, ensuring automatic, absolutely reliable sanitizing. Specifically fitting the system with glass doors also gives customers absolute transparency and fast access to individual elements in the interior of the machine. This makes maintenance an easy task. Both the transfer stars and filler and capper have separate servo drives that are located in hygienically designed columns. This means that not only the housing is engineered according to hygienic design criteria but also the entire machine as well. The filler/capper monoblock encased in the mini hygiene housing and stretch blow molder are controlled by the multi-award-winning KHS operator panel (red dot award and iF award) with an integrated RFID system. The KHS panel excellently combines ergonomics, navigation, and design. The result is user-friendly machine operator prompting that makes use of buttons, colored graphics, easy-to-remember icons, and interactive handling instructions, all of which are self-explanatory.