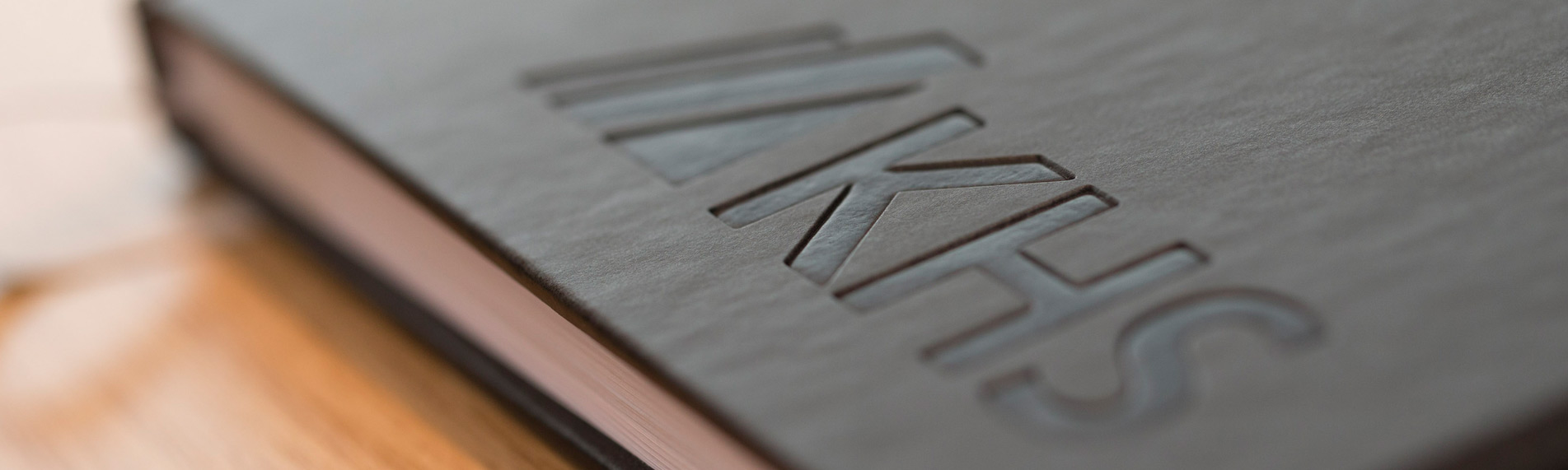
Maximum flexibility through direct digital PET bottle printing
KHS launches new KHS-Innoprint bottle dressing technology to market
With the new KHS-Innoprint machine KHS now enables beverage companies to print labels and logos directly onto their PET bottles. This direct digital printing process provides much more flexibility than classic roll-fed labeling technology, with the required print image transfered straight from the computer to the machine's control unit. This enables new bottle printing ideas to be implemented at great speed, as the KHS-Innoprint's control unit processes the data it receives very quickly. As a result, the smallest batches – or in extreme cases even each individual PET bottle – can be adorned with a different image. With their brilliant color and outstanding optical resolution of 1,080 x 1,080 pixels the ensuing prints are totally convincing.Another advantage of KHS' new digital printing process are the recipe-controlled format changes which make for very fast changeovers. If new bottle types are scheduled for printing, the print head is adjusted to the relevant position for the new bottle diameter and/or height within the space of a few minutes. The machine is able to process a large number of different PET bottles, with containers holding from 0.33 to 1.5 liters all doable. Container diameters can vary between 40 and 120 mm. UV inks are the only consumables required in the KHS-Innoprint process; the elaborate logistics involved in procuring labels – common to roll-fed labeling, for example – is thus now a thing of the past. This in turn considerably reduces CO2 emissions.
In its standard version the KHS-Innoprint machine operates with five color carousels, each of which applies a designated color to the PET bottles. In order these are white, cyan, magenta, yellow, and black. Other color carousels can also be inserted, such as those loaded with spot colors, to print a special, true-color logo.
The standard is to have an air conveyor feed empty bottles into the machine yet in the future it will also be possible for the printer to be monoblocked with a stretch blow molder. On the KHS-Innoprint each PET bottle is handled by its neck and held in a separate clamp (puck) driven by a direct drive. The bottle mouth remains sealed through the entire printing process and for stability either nitrogen or sterile air can be inserted into the bottle. The puck conveys the bottle from color carousel to color carousel, locking it into place magnetically. There is no need for bottle transfers, and very high precision printing is a given.
The UV inks used in the direct print system meet KHS' extremely demanding specifications. They have a low viscosity, set within a few milliseconds, have a good opacity, can be overprinted, and have an outstanding adhesion to untreated PET bottles. The applied ink is briefly dried by UV light in each printing station (pinning). Once the print has been hardened or cured by UV light the labeled bottle is able to withstand all handling inline, in store, and by the consumer. The UV inks specially developed for KHS for this new piece of plant equipment are extremely suitable for use on PET food packaging. Investigations into the inks' migration characteristics have revealed that they are suitable for use on food packaging. Directly printed PET bottles can also be bottle-to-bottle recycled.
The KHS-Innoprint is designed to output 36,000 PET bottles per hour. Each color carousel on the machine has 12 printing segments. If required these color carousels can be equipped with fewer segments, meaning that customers can start out with a lower printing capacity and gradually increase this if and when needed. Where the KHS-Innoprint setup is implemented, between 0.1 and 0.25 ml of UV ink is needed per bottle print, depending on the degree of coverage and size of the printing area.
To sum up, the KHS-Innoprint is distinguished by its as yet unrivaled degree of flexibility, minimized warehouse logistics, reduced changeover times, and lower CO2 consumption thanks to less shipping of materials. This is truly a phenomenal innovation with a full range of added benefits.
KHS Microsite - drinktec