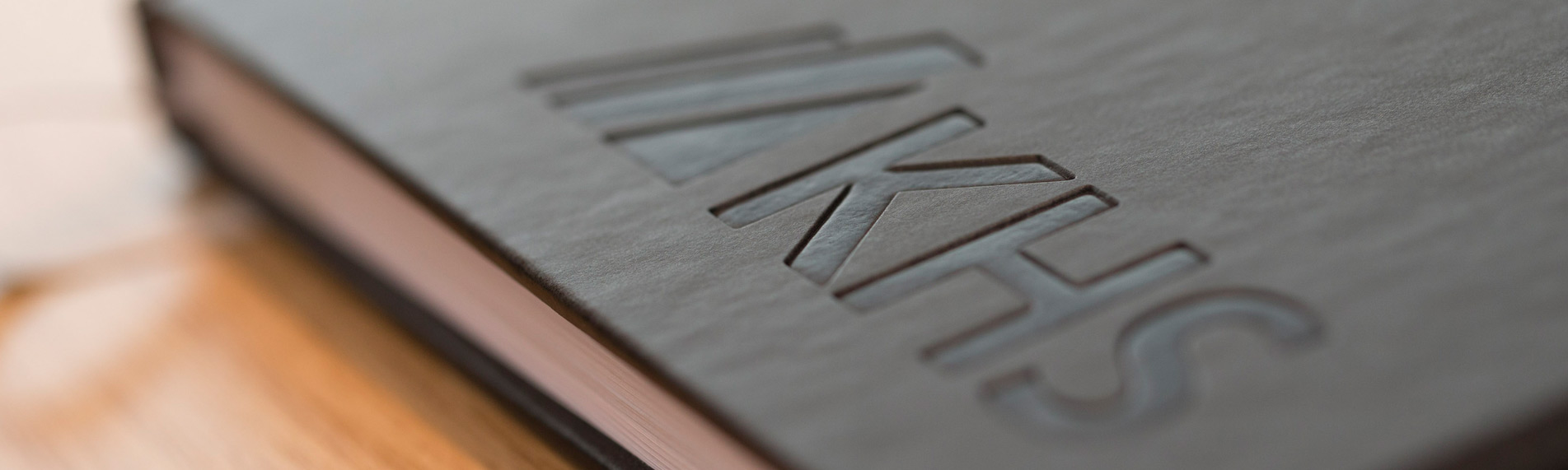
New KHS development: sustainable, cost-effective film processing in the shrink packer
With two new developments for the shrink packer KHS is meeting industry demands for economy and sustainability. To be more precise, these are a film spreader that requires about 90% less compressed air than previously used, and an innovative distance sensor that greatly saves on film material.
Before packaging units are wrapped in film, in the shrink packer this film is unwound from the reel, spread, and then cut to the specified length. On Innopack Kisters packaging machines film is spread with the help of air-covered diverter rails. Here the air acts as a lubricating film so that the wrapping film is conveyed with as little friction as possible, meaning that no damage can occur. To date the air was supplied through several holes in the rails, each about 1 mm in diameter. The disadvantage of this procedure was the relatively high consumption of compressed air.The new development now operates with diverter rails made of a microporous material where the air flows through very fine hairline cracks. The resulting air lubricating film is much more even than in the previous setup and a lot less compressed air is needed. The friction on the film is also greatly reduced and the film is conveyed extremely gently. Practical tests have shown that where the new system is utilized compressed air consumption drops by up to 90%. As no creases can be formed in the film with the newly designed diverter rails, the film no longer has to be respooled when requirements change, for example when switching over from twin-lane to single-lane film processing. This cuts down on changeover times. It's not just new machines that profit from the new diverter rails made of microporous metal; this innovative system can also be retrofitted. The time taken to do so is minimal and comparable to that needed to change a format part. The return on investment is about 1 1/2 years.
Another important advance in KHS shrink packer technology is that the amount of film left on the reel has now been minimized. A newly developed distance sensor ensures that as little film as possible remains on the finished reel, thus helping to make significant material savings. The distance sensor is calibrated to the size of the reel center before the machine is started. Should the thickness of the reel center alter when the film reel is changed, the sensor must be recalibrated. The distance sensor contains a laser with the help of which the film can be processed until a layer about 2 mm thick remains on the reel. To date it was common for about 1 kg of film around 1 cm in thickness to remain on each reel. If we assume that production runs in two shifts on 300 days of the year, this means that a single-lane machine working at 80 cycles a minute can save up to 12 metric tons of material. Assuming the film costs €3.20 per kilogram (the price of printed film), this means a cost reduction of approximately €38,400 per year.
The new KHS distance sensor can also be quickly and easily retrofitted into existing machinery. To this end the light barrier is removed, a new sensor plus bracket installed, and the new software loaded.