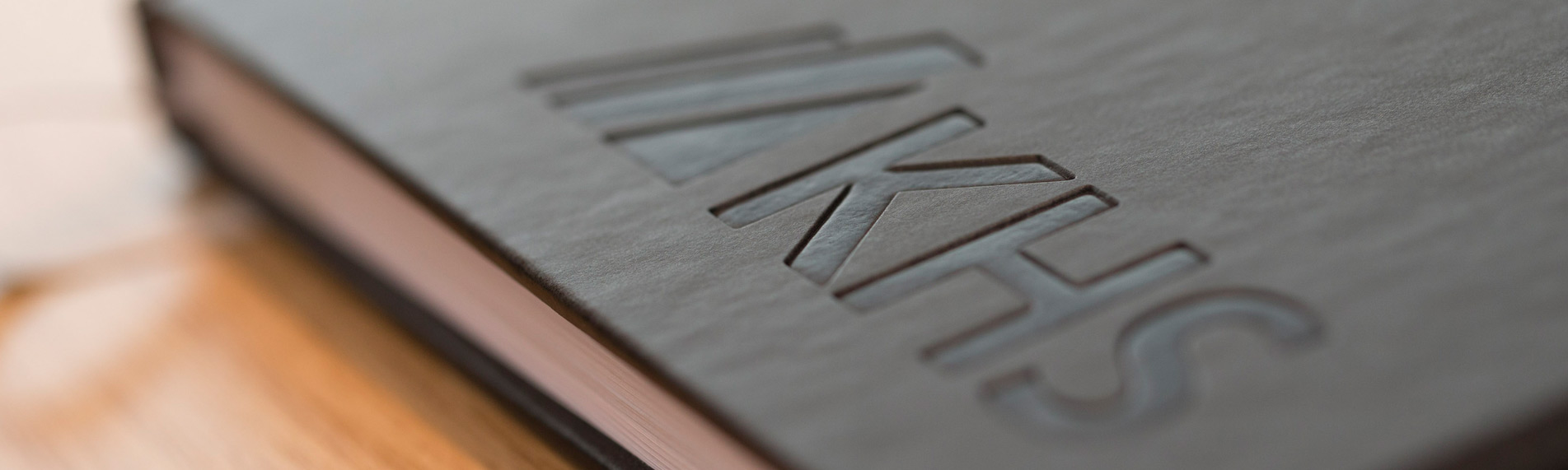
Reliable, flexible, easy to operate, and extremely popular
KHS Innoket Variant 1 labeler convinces the beverage, food, and non-food industries
With its robust design, ease of operation, high reliability, and excellent labeling quality KHS' Innoket Variant 1 has proved convincing for several decades now. To date, over 1,200 Innoket Variants have been sold to over 40 countries of the world, with the labeling machine processing up to 10,000 containers per hour. What's new is the greater flexibility this extremely popular piece of plant technology can now offer above all small and medium-sized companies. In the past the Innoket Variant was able to process cylindrical containers with a diameter of between 40 and 120 mm. It now has the option of labeling containers that are up to 160 mm in diameter. The label height is also more variable, with labels up to 250 mm tall now optionally processable as opposed to the previous 200-mm height limit. The minimum size is 40 mm, with the minimum application height at 2 mm. Label widths may vary from 80 mm to 325 mm. The new label and overlap correction unit on the label box also helps to further boost the labeling quality, allowing corrections to be made in next to no time. These new options can be retrofitted onto existing labeling machines – and the reworked generation of machines is of course CE conform. The Innoket Variant 1 is predestined for labeling all kinds of container, processing plastic and glass receptacles, and cans. The sole prerequisite for perfect label application is that the container is stable and robust enough. One great advantage of inline labeling technology is that considerably fewer format parts are needed than on a rotary machine. Infeed stars, discharge stars, guide curves, and turntables are all bottle guide parts the inline machine doesn't need. The label box can also be adjusted to suit various sizes of label. The reduced number of format parts means that changeovers on this labeler are faster, the maintenance effort is minimized, and costs for individual sets of format parts are cut. After just five minutes the Innoket Variant 1 is ready to start processing new labeling options. There are also no limits to the number of formats that can be run on this system. The Innoket Variant 1 has been designed as a cold glue labeler, applying both patch and wrap-around labels. Before they enter the machine, as an option the containers can be fed past a flowgate. Here, sensors reliably detect if a predefined number of bottles is ahead of the machine. If not, the flowgate automatically closes. This ensures that the accumulation of containers is defined, maintaining a steady flow of the same through the machine. The containers entering on the infeed conveyor are correctly spaced by the feed screw. A sensor then triggers the labeling process. The gluing roller shell takes a label from the box, applies a horizontal strip of glue to it, and moves it towards the container to be labeled in the designated position. The label is pressed onto the container by a rotating repressing belt which is made of plastic foam, thus handling the containers extremely gently. The simple design of the Innoket Variant 1 means that commissioning times are very short. Its uncomplicated construction also allows operators to become quickly familiar with it. All told, the Innoket Variant 1 labeler is destined to continue making a name for itself as a reliable and flexible master of endurance.