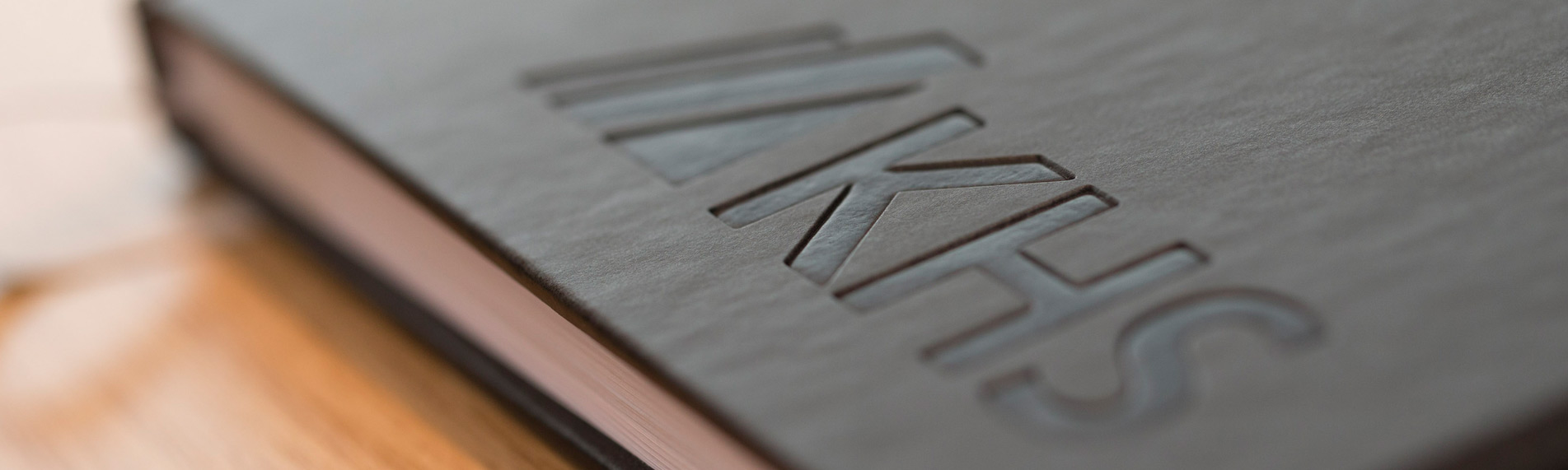
Seventh Place among Russian Breweries in Just Two Years
Moscow Brewing Company on the way up – with KHS technology
Natalia Nikashina* Ulrich Steinert** For over ten years, up until the end of 2007 sales on the Russian beer market steadily increased. In 2008 this upward trend began to reverse slightly for the first time, with beer production in Russia falling by 0.6% to 114 million hectoliters. In 2009 figures dropped further – by more than 10%. The Russian market for beer currently chalks up a much reduced sales volume of over 90 million hectoliters a year and per-capita consumption has fallen to around 65 liters per annum. These facts and figures do not exactly suggest that setting up a new brewery in Russia at present could prove to be a successful enterprise. Nevertheless, the Moscow Brewing Company refused to be intimidated and at the end of 2008, at a time when most experts would have strongly advised against it, they started up production at their new brewery in Mytishchi just outside Moscow. And in doing so, along the lines of "We don't do things by half", it gave no less than three new KHS filling lines the go-ahead. These were a glass line with a capacity of 50,000 0.5-liter bottles an hour, a PET line processing 22,800 1.5-liter bottles an hour, and a keg line that was initially programmed to rack 80 kegs an hour but that can be expanded to cope with 120 kegs an hour. Courage is often well rewarded – and this is certainly the case with the Moscow Brewing Company (MBC), its success ongoing to this very day. In early 2011, the company looks back on beer sales of 1.65 million hectoliters and non-alcoholic beverage sales of 150,000 hectoliters for 2010. In order to meet heavy market demand, hot on the heels of its first three lines MBC then invested in a KHS canning line that produces 40,000 0.5-liter cans an hour and in another KHS glass line which outputs 48,000 0.5-liter glass bottles an hour. Yuri Lobanov, plant manager at the Moscow Brewing Company, says, "Our success on the market is based on the fact that we offer our consumers the best product quality. In our opinion, this goes hand in hand with outstanding technical systems. And it's precisely for this reason that KHS technology is used in our company." * Manager of RC CIS, General Director of KHS Russia.Phone: +7 (495) 783-8100 ** Technical Line Support, KHS GmbH, Bad Kreuznach, Germany. Phone: +49 (671) 852-2327 Eighty-percent sales increase within one year MBC naturally hoped it would be successful right from the start of its business activities. "However, we couldn't possible foresee that we would experience such a rapid increase in sales," says Lobanov incredulously. In 2009, just one year after its launch, MBC's sales of beer and alcohol-free beverages totaled one million hectoliters. If you add to this the 1.8 million hectoliters of beer and non-alcoholic beverages sold in 2010, MBC has notched up a sales increase of over 80% since its start. Further growth is expected. "By 2012 we would like to have sold at least four million hectoliters of beer and one million hectoliters of alcohol-free beverages," states Lobanov. The secret of success: quality at a reasonable price and sophisticated brand politics This is an ambitious but realistic goal, looking at MBC's success to date. "We are sticking to the secret of our success," Lobanov claims, "one that effectively combines top quality with sophisticated brand politics and a reasonable price for the consumer." Extensive range of licensed brands Besides manufacturing its own brands MBC also concentrates on the bottling and sale of products filled under license. Within the beer sector the company bottles licensed brands Oettinger, Faxe, Breznak, and Coors Light, for example. Non-alcoholic beverages currently include brand names Pago, Orangina, and effect. Right combination of tradition and innovation MBC's chief beer brand is without a doubt its own Zhiguli Barnoje, designed to remind consumers of the bygone days of Russia. The label in particular helps to create a certain sense of nostalgia. At the same time Zhiguli Barnoje also seems highly innovative, especially looking at the chosen bottle shape and high-quality dressing. "It's this combination of tradition and innovation that makes Zhiguli Barnoje so successful," explains Lobanov. Zhiguli Barnoje is MBC's number one brand with a 70% sales share Zhiguli Barnoje is indeed successful, with around 70% of MBC's total beer sales attributable to this particular brand. The MBC beer brand Mospivo makes up a further 10%. The remaining 20% is yielded by the licensed brands. The marriage of nostalgia with new values is also what makes Mospivo so popular. The Mospivo label depicts the people of Moscow dressed in the fashions of the 1970s and 1980s engaging in various pastimes. Lobanov explains that "Many Muscovites feel transported back to their youth when they see the Mospivo labels. And they like it." Surprisingly, this not only applies to the older generation. Young adults also find the concept – new to the Russian beer market – of showing people engaged in past activities on beer labels extremely exciting, prompting them to choose Mospivo with growing frequency. Young people are also increasingly drinking another beverage that combines the traditional with the innovative: Moskvas, the classic Russian bread-based beverage. Brands for Moscow As a beer brand "with and for the citizens of Moscow", Mospivo and kvass brand Moskvas are almost exclusively distributed in the Moscow region. As its name would suggest, the Moscow Brewing Company is strongly centered on the Russian capital as far as distribution is generally concerned. Of its total sales, 60% currently remain in and around Moscow. If we remind ourselves that MBC has only been up and running for just over two years, it's hardly surprising that the initial focus of their sales activities is on their neighboring capital city. More extensive distribution within Russia and CIS planned With a company as dynamic as MBC, it's no wonder that a more extensive area of distribution within Russia is planned for next year. At the same time the company is to systematically build up an export network with other members of the Commonwealth of Independent States. Incidentally, MBC already ranks seventh among all of Russia's breweries. It remains to be seen whether things might soon change, enabling the newcomer to climb further up the top ten. Now producing its own brand soft drinks This rise in the brewery hit parade could also be promoted by soft drinks. In this segment MBC bottles licensed brands and also its own beverages that went into production just a few months ago and are now in the market launch phase. These include fruit beverage Afrika, for example, and Gorilla, an energy drink. New KHS glass line for many types of beer, alcohol-free beverage, and glass bottle MBC's own and licensed beer and non-alcoholic beverages are bottled and packaged on the recently installed KHS glass line that is able to process a wide variety of glass bottles ranging in size from 0.2, 0.25, and 0.33 liters to 0.75 liters to 1 liter. The heart of the system – an Innofill DRS-ZMS The heart of the glass line is an Innofill DRS ZMS filling system that is immediately preceded by a rinsing system. "This filling system has already proved its worth in our existing glass line," Lobanov says. "In our eyes KHS filling technology is the Mercedes of filling technology. Everything's just perfect – from the filling accuracy to the efficiency to the low-oxygen filling process." Extremely gentle filling process The Innofill DRS-ZMS operates with fill level probes. The pressurizing process is preceded by triple pre-evacuation and double CO2 purging. After pressurization, the liquid valve opens and conducts the product over a swirler to the inner walls of the bottle. High valve filling output is achieved during the fast filling phase in the uncritical, cylindrical part of the bottle. A slow filling phase takes place in the narrow bottle neck for exact fill level measurement. A pulse from the probe closes the liquid valve. This is followed by pre-snifting and final snifting. Pressure-controlled snifting takes place with little foam. The filling process is carried out independently of speed. The filling phase setpoints and thus the fill levels for all valves can be changed centrally even during the filling process. Closures are applied by a crown cork capper. The filling system has a heat retention function especially designed for fruit beverages which have to be hot filled. Double-deck pasteurizer pasteurizes and cools Hot-filled non-alcoholic beverages are then gently cooled in the double-deck Innopas PII SC pasteurizer downstream of the filling and capping system, and quality beers pasteurized if required. Energy drinks and carbonated soft drinks use the pasteurizer as a conveying segment. The Innopas PII SC has an integral PU control system and is specifically designed for exceptionally gentle product handling. The heat exchange between the heating and recooling zones reduces the energy and water consumption in continuous pasteurizer operation to a minimum. Active spraying on each deck is a standard feature for a uniform pasteurization process. Additional temperature increments can be achieved by using several pumps and separate water tubs in one heating or recooling zone. Fresh water spraying at the discharge is used for rinsing off containers and to replenish water lost through carryover and evaporation. Labeling equipment for all labeling requirements There is one particular feature of the line Lobanov thinks is a real highlight: the Innoket SE 2090 labeling machine. The basic version of this generation of labelers has been kept deliberately simple and consists of a table structure and the central labeling carousel which can be equipped with a wide variety of labeling stations. The Innoket SE 2090 installed at MBC is currently equipped with four docking stations. One is for the self-adhesive labeling station, one for cold glue labeling, the third for roll-fed labeling jobs, and the fourth for the camera-based alignment module. (The latter is required for the Zhiguli Barnoje bottle which is aligned with the embossing on the bottle prior to labeling.) This setup can be changed at any time – to include hot melt labeling, for example. If this additional labeling process is required, the only necessary investment would be in a fifth labeling station. Labeling station changeover is also quick and easy, as the stations are simply docked and undocked to the Innoket SE 2090. If a labeling station is changed, all stations can be automatically resynchronized by software and computer. Says Lobanov, "The Innoket SE – which we've incidentally had very good experience with on our lines previously ordered from KHS – gives us maximum flexibility with the highest labeling accuracy. This is so important because, as we see it, to the outside world a perfectly applied label is an indication of a quality product." Canning line processes 0.5-liter and 1-liter cans As with all of the company's KHS filling and packaging lines, Lobanov is also extremely pleased with the KHS canning line installed soon after MBC's first KHS systems. This line fills both MBC's extensive range of beers and its complete assortment of soft drinks. What's special about this particular line is that in addition to processing the classic 0.5-liter can it is also able to fill 1-liter cans which are currently used for the Faxe brand of beer. Electromagnetic inductive flowmetering for maximum filling accuracy The cans leave the Innopal ASH bulk depalletizer and an air conveyor feeds them over a vacuum bridge that checks and channels out any deformed cans. They then pass through the can rinser straight to the heart of the line: an Innofill DVD filler. Like the Innofill DRS-ZMS, this filler also has a heat retention function for the hot filling of fruit beverages. The Innofill DVD provides maximum filling accuracy through the use of electromagnetic inductive flow metering throughout the filling process. It is no longer of consequence whether the cans delivered by different manufacturers are identical or not. If filling quantities of 0.5 and 1 liter are programmed, then the cans filled by the Innofill DVD will actually contain 0.5 or 1 liter of beverage – no more, no less. In contrast, with conventional fill level systems possible tolerances of the cans as regards fill level selection must be taken into account, resulting in overfilling. The steps performed prior to the actual filling process include can placement, sealing, purging, and pressurizing. Purging cans with CO2 is important in order to meet the requirements of low-oxygen filling. The liquid valve opens when the CO2 purging and pressurization processes are completed. Pneumatic cylinders control both the liquid valve and gas passages. The filling process takes place under pressure. Once filling is completed, the existing pressure is reduced, pressure-controlled, to that of the surrounding atmosphere. Gas escapes through the snifting channel. Snifting takes place with little foaming. As on the newly installed glass line, an Innopas PII SC pasteurizer pasteurizes the cans filled with beer and recools those cans which have been hot filled with non-alcoholic beverages. Here, too, energy drinks and carbonated soft drinks use the pasteurizer as a conveyor. Tray shrink packs … An Innopack Kisters TSP Basic tray shrink packer packs the cans as follows: the 0.5-liter cans are shrink wrapped in trays of 24 and the 1-liter Faxe cans in trays of 12. … are gently handled to protect materials A fully automatic Innopal PL 1 BSN palletizer palletizes the tray shrink packs. Complete layers are transferred from the layer preparation table to the pushover plate of the palletizer. The palletizer's gantry-type design makes it possible to feed the packs to the palletizer at any height. The row and layer pusher is driven by toothed belts, which means gentle handling of materials as well as minimum servicing effort and low wear. A pallet wrapper installed after the palletizer secures the pallet loads. The success story continues – For the time being, MBC feels it is well equipped with KHS filling and packaging machinery to meet the ever-growing demand of the market. For the time being, that is. Investment in new equipment could soon be on the cards. For example, MBC is planning to extend its brewery capacity to up to 5 million hectoliters a year. If and when it does, it will probably retain its current assortment of packaging styles, i.e. 60% of total beer sales in glass, about 30% in cans, and the rest in PET bottles. There is also talk of a new plant being built solely for the processing of alcohol-free beverages which are to be chiefly filled in PET bottles and cans. MBC is also thinking about including mineral water in its range of products. "However much our company grows," declares Lobanov, "we will continue to pursue our aim to provide quality without compromise. And we will remain transparent for our consumers." transparent right down to the technical equipment This transparency is taken literally – as the company building demonstrates. Most of the filling and packaging technology is behind glass and thus clearly visible from outside. Visitors to MBC are also very welcome. "Do something interesting and talk about it" is the motto here. Small wonder, then, that the brewery has become something of a magnet for the people of Moscow keen to go on a guided tour of the plant, especially on weekends. These tours once again demonstrate how well the Moscow Brewing Company combines tradition and innovation. "During these tours," concludes Lobanov, "we also like to express our sense of pride in our KHS technology – and thus in our top-quality technical systems."