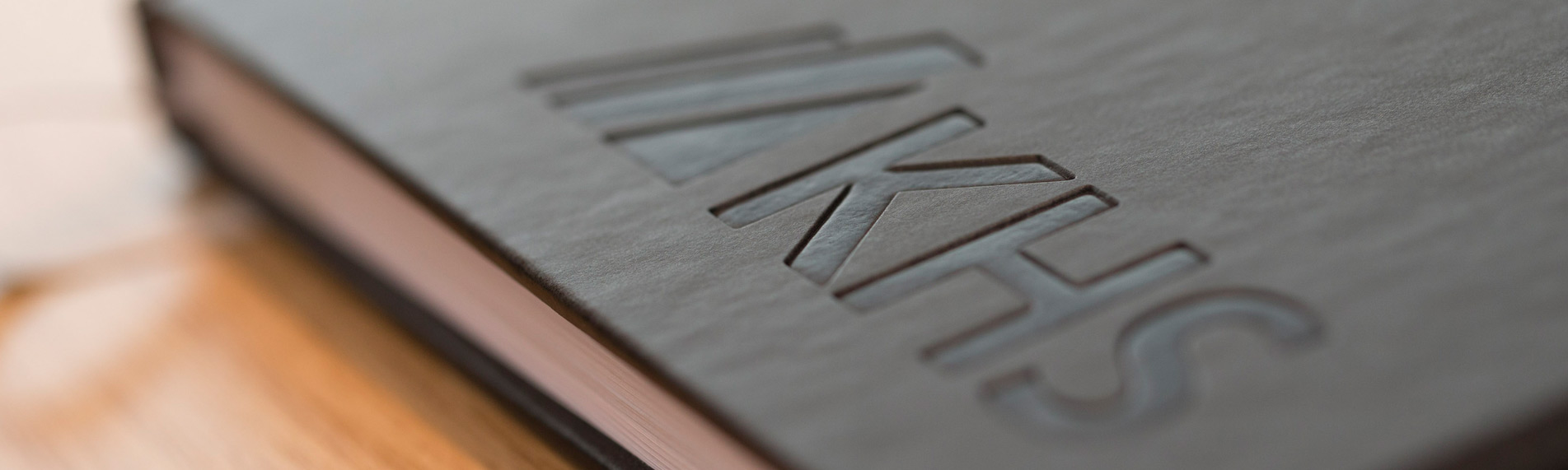
The sign of the lion
Boon Rawd Brewery, Thailand, strictly adheres to its policy of quality for Singha beer and water brands
Latest investment in three KHS water lines Frank Hollmann*Detlef Mette**
Phiphat Poonphatanapreecha***
For several decades Boon Rawd Brewery in Thailand has relied on KHS as its partner for innovative filling and packaging technology. Only recently the company invested in no fewer than three water filling systems. One KHS PET line went to the bottling plant in Wang Noi in the center of Thailand, with a PET and a glass line being delivered to the Surat Thani site in the south of the country. First brewery in Thailand and the only one with royal permission Boon Rawd Brewery is one of the giants of both the beer and the water segments in Thailand. It was the first brewery in Thailand to be founded in 1933 by Phraya Bhirom Bhakdi (Boonrawd Sreshthaputra). Based on experience amassed on his past travels to Germany and Belgium, Boonrawd initially created three different beers which were all market tested. Singha Beer was the brand to come out on top and is still brewed according to the original recipe with 100% barley malt. Thailand's royal family was also convinced by Singha's excellent quality, granting it royal permission in 1939 – now the only brand of beer in Thailand to have this privilege. Many activities in the beverage and food sectors Shortly after the production of Singha Beer started Singha soda water was launched, a highly carbonated water which was and still is chiefly used to mix various alcoholic beverages. In the early 1980s Boon Rawd Brewery entered the still water segment with its Singha drinking water. The newest addition to its range of waters is Purra, a mineral water. B-ing and Sanvo are two of the several other beverage brands in the Boon Rawd portfolio, introduced about two years ago. B-ing is a series of functional drinks enhanced with vitamins and nutrients, where Sanvo is an energy drink available in various flavors. The company very recently extended its range of activities to include food, where it markets the brands Masita (seaweed snacks), Pun Dee (rice), Boon Rawd Farm (tea, jams, fruit juices, etc.), Fine Food Capital (packaged ready meals) and Hesco (Japanese rice crackers). *Head of Market Zone Asia Pacific, KHS GmbH, Bad Kreuznach, Germany. Phone: +49 671 852 2888
**Project manager for Market Zone Asia Pacific, KHS GmbH, Bad Kreuznach, Germany. Phone: +49 671 852 2584
***Head of the KHS office in Bangkok Beer and water the company mainstays Boon Rawd's mainstay has always been (and still is) the beverage segment, with beer and water in particular. The company now has three breweries in Thailand and six bottling plants for non-alcoholic beverages, all of which are strategically placed throughout the country. While beer consumption in Thailand is stagnating, according to various prognoses water still holds great potential for growth. This is something Boon Rawd Brewery would like to exploit to its advantage through targeted expansion of its filling capacities for carbonated and non-carbonated water. Very strong growth for still water in PET bottles While carbonated water at Boon Rawd is only filled into glass bottles, sales of still water in PET especially are continuing to grow. Debhakam Rojrit, executive vice president and director of Boon Rawd Brewery Co., Ltd., states, “This was also why we invested in not one but two new KHS PET lines – one at Wang Noi Beverage and one at Surat Thani Beverage." Both lines have the same system components and output up to 36,000 bottles per hour. This means that they have been designed to take up as little space as possible at each plant and are both operator friendly. Boon Rawd currently has four sizes of PET bottle in its range, holding 330, 500 and 750 milliliters and 1.5 liters. The biggest sellers are the 500-ml and 1.5-liter bottles, with about 80% of all PET bottle sales attributable to these variants. In order to meet the great demand for these containers, the new KHS line in Surat Thani only produces and fills these sizes. An InnoPET Blomax Series IV ... The PET bottles are manufactured by an InnoPET Blomax Series IV stretch blow molder which has 16 blow stations, each of which outputs up to 2,250 PET bottles per hour. The standard InnoPET Blomax Series IV produces bottles holding between 0.2 and 2 liters. Rojrit is pleased. "This generates plenty of flexibility for the future," he smiles. One striking feature of the machine which helps to reduce energy consumption is the heater area. With it, preform heating times are just about halved compared to the previous series. In Series IV stretch blow molders preforms are heated by near infrared (NIR) or shortwave infrared radiation, the use of which results in an extremely intense heat penetration of the preform walls. The stretching process within the blowing stations is controlled by servomotor, enabling preforms to be optimized down to the last tenth of a gram of PET material. Outstanding bottle qualities are a given and changeover times are especially low when swapping from one bottle variant to another. Promna Panupong, plant manager at Surat Thani, is equally happy. "We appreciate the bottle qualities and the performance of the InnoPET Blomax and also the fact that it's directly blocked with the Innofill NV filling system." ... blocked with the Innofill NV filling system After the stretch blow molding process the finished PET bottles are passed on to a transfer wheel. An airlock strictly separates the dry area of the blow molder from the wet area of the filler. The bottles are filled with water by an electronically controlled Innofill NV normal pressure filling system with 60 filling stations. The Innofill NV operates according to the principle of volumetric filling using electromagnetic induction flowmetering. Non-contact filling through a free-flow filling valve ensures maximum microbiological and hygienic safety. The bottle necks are not pressed and sealed against the filling elements, with the result that the valve components do not come into contact with the bottle neck. Product wetting is therefore not a matter of concern. All passages are smooth-surfaced throughout the Innofill NV from the ring bowl to the filling valves. As in all other product-conducting channels and passages, aseptic membranes and sealing techniques are used within the filling valves. The filling process in brief is as follows: the filling phase is initiated after the bottle has been guided by the neck ring and positioned under the filling valve. The bottle is then filled with the exact quantity of product and the filling process subsequently stopped. A simple filling process takes place which is microbiologically extremely safe. The capping system implemented here is the proven, classic Innofill SV screw capper. The filling system is located in a sanitary room fitted with filter systems, again ensuring maximum filling quality. Innoket 360 roll-fed labeler with integrated tamper-evident sleever An Innoket 360 roll-fed labeling machine decorates the full PET bottles. Here, the endless plastic label material is supplied on a roll. The label web runs from the roll over a controlled feed mechanism to the labeling station where it is cut to the exact length according to markings printed on the web. The cutting unit with its self-sharpening cutter is one of the machine highlights. The cut label is transferred from the vacuum drum to the container using hot melt. An innovative, induction-based gluing system ensures precise and efficient gluing. The labeling station can be swiveled out to perform mismatch corrections during the ongoing production process. The Innoket 360 is ergonomic in design and provides excellent accessibility to all areas. A segmented vacuum drum allows quick and easy changeovers. The integrated tamper-evident sleever on the Innoket 360 is an optional extra and applies and shrinks sleeves across the bottle neck, which is important if forgeries are to be prevented. Packing and palletizing The PET bottles are wrapped in film by an Innopack Kisters SP 050 Basic shrink wrapper which forms 1.5-liter PET bottles into packs of 6 and smaller bottles into packs of 12. An Innopack Kisters CSM then applies handles to the six-packs before these travel on to the palletizer. Packs of 12 are generally supplied without handles and thus pass directly to the Innopal PB1N2 palletizer. Each complete layer is transferred from the layer preparation table to the pushover plate of the palletizer, with each layer being automatically centered before it is discharged onto the pallet. The result is perfect layer formations, gentle product handling and high overall stability of the load. The line inserter goes into action automatically after each layer is released. Outstanding acceptance results for the PET lines and glass line Rojrit again voices his approval. "We're just as happy with our new KHS PET lines as we are with our new glass line. All of our lines were accepted with over 95% line efficiency.” The glass line processes both returnable and non-returnable bottles which are filled with either still or soda water. Soda water is filled into 325-ml one-way and 400-ml returnable glass bottles, with still water bottled in the returnable glass 0.5-liter container. The line has a maximum output of 50,000 bottles per hour. Returnable and non-returnable glass bottles processed Non-returnable bottles are depalletized by an Innopal ASN with its four-sided, enclosed pushing system and passed straight on to the Innoclean DM bottle washer. Crates of returnable bottles are depalletized by an Innopal PK1EKN1 portal system and decrated by an Innopack PPZ. The Innopack PPZ is a twin-axis gantry robot that provides exceptional accessibility and ease of operation. It is flexible and suitable for use as both a decrater and a crater, which is why Boon Rawd decided to procure two Innopack PPZ machines. A second of these modern cyclic craters therefore handles the task of packing the filled returnables into prepared crates at the other end of the line. Double-end Innoclean DM bottle washer with extras In order to ensure maximum hygienic safety, both the returnable and non-returnable glass bottles (with a separate program in fast mode) are fed through an Innoclean DM bottle washing machine. Energy-saving bottle carriers provide targeted sustainability here, as the energy-saving bottle carrier weighs around 25% less than a conventional carrier. The lower carrier mass also means that less heat and caustic are carried over, which in turn directly affects the amount of energy and fresh water consumed by the bottle washer. Through the energy-saving carrier alone 10 to 15% less heat and 15 to 20% less water are usually used. The bottle washer has rotating sprays in the pre-wash area. These are crucial in the treatment of Boon Rawd's returnable bottles which often come back to the brewery in an extremely soiled condition. Rotating spray tubes move synchronously with the travel of the bottle pockets and thus with the bottle necks. The resulting long spray time and turbulent distribution of liquid ensure a maximum cleaning effect in the bottle, discharging coarse soiling residue with outstanding efficiency and therefore extending the service life of the caustic. Says Panupong, "The Innoclean DM gives us the good feeling that all of our bottles get a perfect wash. At the same time it saves us a lot of energy and water which means it perfectly adheres to our demands for sustainability." Filling system manages perfectly manages 'critical' soda water bottling process Boon Rawd also had high demands with regard to the filling system. The new setup had to be capable of filling highly carbonated water. KHS accepted the challenge, installing a number of updates on the Innopro DCX deaerating and carbonating system and making adaptations to the filling pressure on the Innofill DPG-VF filling system. Rojrit says, "After hearing from several other companies that our requirement couldn't be met, we weren't sure that the system would work – despite assurance from KHS. Looking back, there was absolutely no need to be skeptical. Filling of our 'critical' soda water and still water both ran smoothly and as we'd specified." The Innofill DPG-VF filler at Boon Rawd has 144 filling stations and at the closure end 18 capping stations apiece for crown corks and for ring pull tops, the latter destined for the 0.5-liter returnable glass bottles of still water. The non-tube filling system operates with return gas tubes. The fill level is determined by means of the gas tube and gas lock. The quick-change return gas tubes used on the Innofill DPG-VF enable the machine to be rapidly changed over to various bottle sizes. All told, the Innofill DPG-VF stands for high product quality, economical production and maximum flexibility. Panupong claims, "Our operators are especially impressed by the easy handling of this very powerful and robust system." The filler area at Boon Rawd is completely enclosed and the ceiling area fitted with filter units, again satisfying the company's demands for high levels of hygiene. Bottles printed or sent to the Innoket 360 Duo Up until now the returnable glass bottles at Boon Rawd have all been printed, meaning they do not need labeling. After being filled they are sent directly to the Innopack PPZ crater. In the future this could change if needs be, as in the Innoket 360 Duo the new glass line has a labeler which not only applies roll-fed labels to one-way glass bottles but can also dress Boon Rawd's returnable containers with plastic labels. The Innoket 360 Duo has all the benefits of the Innoket 360 used on Boon Rawd's new PET lines. In the duo version it has not one but two roll-fed stations and is thus more powerful, labeling up to 60,000 bottles per hour. Innopack Kisters Advanced packaging technology After labeling the non-returnable bottles are either first sent to the Innopack Kisters SP A-H shrink packer, where they are shrink wrapped into packs of six on two lanes and then passed on to the Innopack Kisters TSP A-H tray shrink packer which turns either two or four of the formed shrink packs into tray shrink packs, or they are conveyed straight to the Innopack Kisters TSP A-H. If required, the six-packs shrink wrapped on the Innopack Kisters SP A-H can be given a handle by the Innopack Kisters CSM. Loose bottles traveling straight into the tray shrink packer are formed into tray shrink packs of 12 or 24. Like all of the packing machines in the Advanced series the Innopack Kisters SP A-H and Innopack Kisters TSP A-H are cube-shape in design, giving operating personnel ample space to work with the machine and thus providing great ease of operation. Together with the new protective hood concept designed for this machine series, the cubic design also provides an excellent view of the inner workings of the packing machines. Another important aspect of these machines is that they can work with very thin film thanks to the recent development of a new film cutting and feed system. A vacuum belt of adjustable width perfectly positions the various widths of film on the conveyor belts. A sophisticated hole pattern enables the latter to discharge any static electricity automatically. In conjunction with an additional antistatic system, this offers maximum conveying stability even for extremely delicate film types. In order to achieve the best possible shrink result for each individual shrink pack using a minimized amount of energy, KHS has included adjustable hot air nozzles in the shrink tunnel area. This enables the air flow to be set exactly as required to fully suit the height and width of the individual pack format. The amount of air required for a perfect shrink result can also be configured for each individual nozzle. Nozzles can also be 'parked', which ensures that hot air is always precisely directed to where it is needed for optimum shrink results. "A professional job" The tray shrink packs or crates are palletized by the Innopal PB1N2 which is used on both the glass line and the brewery's new PET lines. Rojrit smiles. "I can only keep on emphasizing that KHS has made a professional job of our three new lines. For us it was also especially important here that these lines function sustainably and thus comply with our company philosophy with its accent on social responsibility." Best equipped for future growth in water sales With its new KHS plant engineering Boon Rawd is best equipped for further growth in the sales of Singha soda water and Singha drinking water. The chances here are good – not just because the sign of the lion (Singha) has been the strong emblem distinguishing Boon Rawd Brewery brand beers and waters from the very beginning, but also because for several generations of consumers it has been a hallmark of excellent quality.