Filling systems for ESL (Extended Shelf Life) milk beverages in plastic bottles for sale in the cold chain
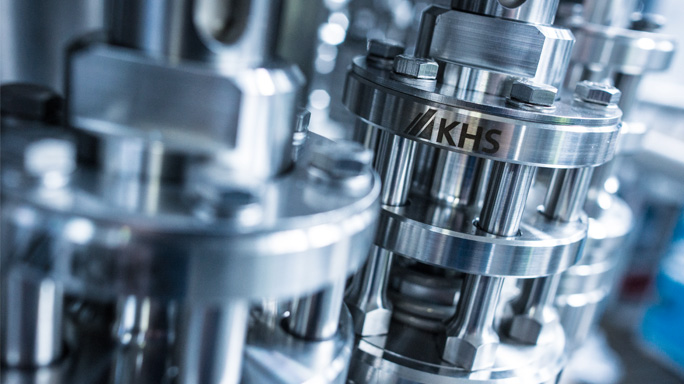
Good to know
In the production and bottling of these beverages high standards of hygiene must be ensured. Here, our cost-effective filling systems for ESL milk, mixed milk, and yoghurt beverages can offer you reliable support.
Designed for multi-shift operation, this system gives you high machine availability. The setup is flexible, filling 0.1 to 2-liter PET and HDPE bottles at rates of up to 24,000 bottles per hour.
From the stretch blow molding process through filling, labeling, packing and palletizing to the necessary inspection equipment, we can supply you with a complete line from a single source.
The heart of the line is the linear Innosept Asbofill ESL 611 TWIN/ESL 711 TWIN hygienic filler and its TWIN versions. The extremely small aseptic zone is perfectly safeguarded, allowing you to process high and low-acid products. The non-contact, free-flow filling system enables products to be bottled gently and with the utmost flexibility when it comes to bottle shape and size. Linear neck handling avoids the need for bottle transfers within the aseptic zone. Both the extended capacity range and choice of bottle material (PET or HDPE) give bottlers a diverse range of application.
With its high process precision (exact heating profile) the high-performance InnoPET Blomax IV stretch blow molder ensures that the PET bottles are reliably fed to the fillers using low amounts of energy. HDPE bottles are fed in by extrusion blow molders which are coupled with bottle silos, neck trimmers, and uprighters.
Well thought out
Thanks to the integrated automatic cleaning process you can work extremely cost effectively with the machinery in our Asbofill series. The bottles are disinfected with the help of an H2O2 aerosol which works reliably on very structured surfaces. The bottles are then dried by sterile hot air until they are practically free of any residue. The system’s compact design means that it takes up very little space on site. The two-stage screw capper provides optimum hygiene conditions.
Convincing
- The highest standards of hygienic safety are reliably adhered to
- Great flexibility with respect to the bottle shape, size, closure, and product
- Fully predefined maintenance concept
Sustainable
- Low life-cycle costs through scheduled maintenance
- High production reliability thanks to fully dependable system components
- Individual retrofitting options provided for a future-proof investment