System solutions for milk beverages in PET bottles
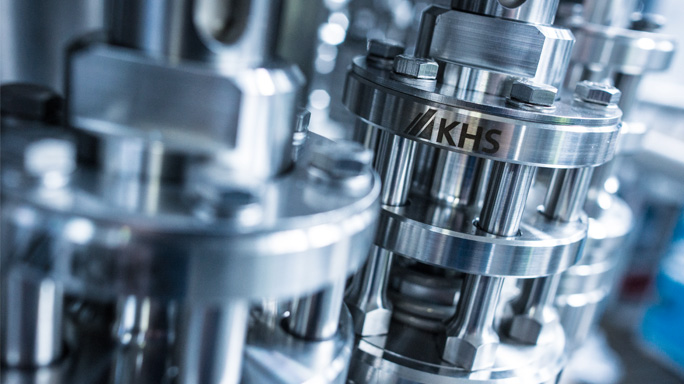
Good to know
Mixed milk beverages are becoming increasingly popular. Due to their high product sensitivity, however, these invigorating sources of protein present a particular challenge to bottling plants. Our proven system solutions for milk, mixed milk, coffee, and yoghurt beverages have been specifically designed to meet these market requirements, providing you with reliable, cost-effective support.
Designed for multi-shift operation, this machinery gives you high availability. The setup is flexible, filling 0.1–2-liter PET and HDPE bottles at rates of up to 24,000 bottles per hour.
From the stretch blow molding process through filling, labeling, packaging, and palletizing to the necessary inspection equipment, we give you an entire line from a single source.
The heart of the line is the highly professional, linear Innosept Asbofill ABF 611 TWIN/ABF 711 TWIN aseptic filler. The extremely small aseptic zone is perfectly safeguarded, allowing you to process high and low-acid products without restriction. The non-contact, free-flow filling system enables products to be bottled gently and in a sterile manner – and with the utmost flexibility when it comes to bottle shape and size. Linear neck handling avoids the need for bottle transfers within the aseptic zone. Both the extended capacity range and choice of bottle material (PET or HDPE) give bottlers a diverse range of applications.
With its high process precision and low energy consumption, the InnoPET Blomax IV stretch blow molder ensures that your PET and/or HDPE bottles are manufactured reliably and according to your expectations.
Well thought out
The aseptic filler's compact, linear design makes it especially suitable for use where there are frequent product changes and small product batches. It also takes up very little space and provides maximum aseptic safety while requiring a very small aseptic zone. The carefully conceived, fully automatic sterilization and filling processes make this machine very easy to operate and the process easy to learn and manage. Our aseptic filler can be supplied with a screw capper or film/foil sealer as required. Another option is to integrate a combination of the two into the machine, enabling you to react to market demands with the utmost flexibility.
Our aseptic fillers have a predefined maintenance concept:
- High production reliability and availability of the system
- Fewer life cycle costs with a longer service life
- Minimized unscheduled failures and faults.
Convincing
- The highest aseptic safety standards are reliably adhered to
- Great flexibility with respect to the bottle shape, size, closure, and product
- Fully predefined maintenance concept.
Sustainable
- Profit long term from low operating costs while enjoying a high level of production reliability
- Our full maintenance program ensures high efficiency and investment profitability
- Opt for a future-proof investment with individual retrofitting options.