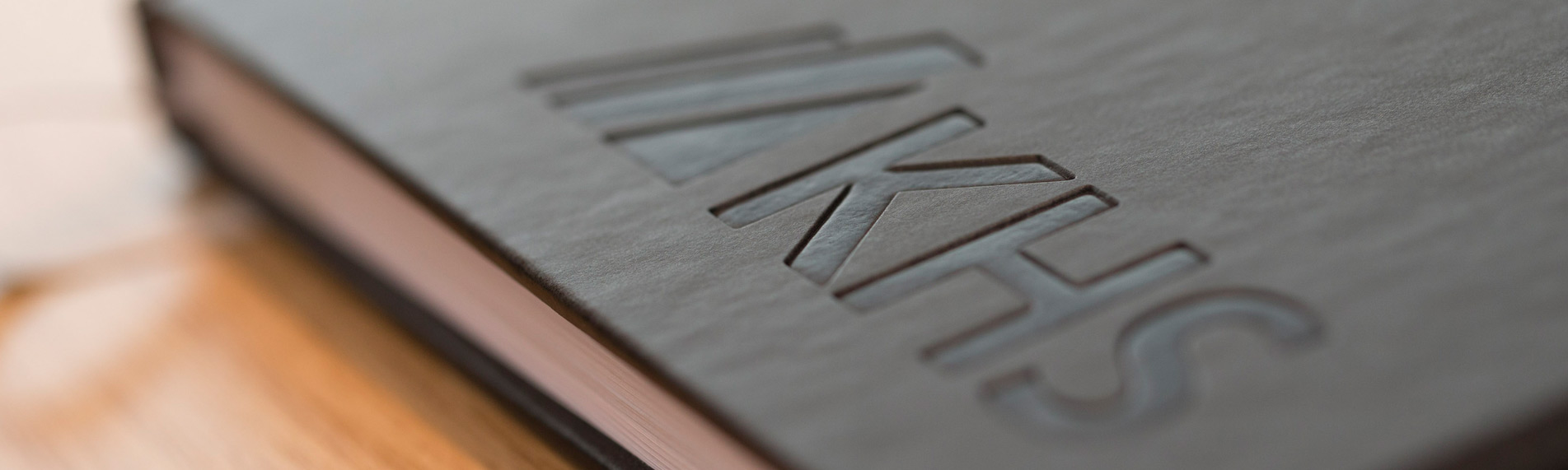
Beste Verpackungsqualität, höchste Flexibilität, minimierte Bedienerbindung
WrapAround- und WrapAroundShrinkPacker vervollständigen neue Verpackungsmaschinen-Baureihe Advanced
Werner Ageling*
Werner Oster**
Die Verpackung von Produkten ist es, die am Point of Sales mit dem Verbraucher kommuniziert. Ist sie attraktiv gestaltet, verlockt sie den Konsumenten idealerweise dazu zuzugreifen. Im Gegenzug bleiben schlecht verpackte Produkte oft Ladenhüter. Diese Gesetzmäßigkeit vor Augen erscheint es für Unternehmen umso wichtiger, bei anstehenden Investitionen in Verpackungstechnik auf beste Maschinenqualität zu setzen. Ebenfalls von hoher Bedeutung: die Investition in technische Lösungen, die höchste Flexibilität beinhalten und die auch für künftige Verbraucherwünsche gerüstet sind. Mit der neuen Baureihe Advanced bietet KHS der Getränke-, Food- und Nonfood-Branche Verpackungstechnik, die den genannten Kriterien Rechnung trägt. Die neue Baureihe Advanced stellt eine Weiterentwicklung von bislang vorhandener modular gestalteter KHS-Verpackungstechnik dar. Das Konzept der Modularität bleibt hier erhalten. Je nach Anforderung werden die Maschinen im niedrigen, mittleren und Hochleistungsbereich mit den optimalen Funktionsmodulen ausgestattet. Bei Bedarf lassen sich auch im Nachhinein noch weitere Funktionsmodule wie z. B. Leaflet- oder Gefacheinserter in die vorhandene Verpackungsmaschine integrieren oder austauschen. Kriterien der neuen Baureihe Advanced wurden bereits für ShrinkPacker, TrayPacker, TrayShrinkPacker und PadShrinkPacker umgesetzt. Als jüngste Mitglieder im „Advanced-Reigen“ präsentiert KHS nun den WrapAroundPacker (Innopack WP) und den WrapAroundShrinkPacker (Innopack WSP).
Leistung bis zu 100 Takte/Minute
WrapAroundPacker sowie WrapAroundShrinkPacker der Baureihe Advanced sind für den Einsatz in der Getränke-, Food- und Nonfood-Branche gleichermaßen geeignet. Die Verpackungsmaschinen verarbeiten
* Leiter Produktmanagement, Competence Center Verpackungstechnik,
KHS AG, Kleve, Tel.: 0 2 821/5 03-2 37
**Leiter Product Support, Competence Center Verpackungstechnik,
KHS AG, Kleve, Tel.: 0 2 821/5 03-1 52
die verschiedensten Produkte aus der Getränke- Food- oder auch Nonfood- Industrie und realisieren eine Leistung von 40 bis hin zu 100 Takten/Minute. Ob Glas-, Metall- oder Kunststoff-Behälter, Dosen oder Kartonverpackungen – alles lässt sich hier perfekt verpacken. Durchmesser von einzelnen Behältern dürfen zwischen 48 und 120 Millimetern, Höhen zwischen 110 und 360 Millimetern variieren. Gebildete Produktgruppen können in der Länge 160 bis 540 Millimeter, in der Breite 130 bis 340 Millimeter für sich einnehmen.
Verarbeitung von unterschiedlichstem Kartonmaterial
Höchste Flexibilität ist auch in Hinblick auf das zu verarbeitende Spektrum an Kartonmaterial gegeben. Ob unterschiedliche Kraft- oder Wellpappekartons – WrapAroundPacker und WrapAroundShrinkPacker der neuen Baureihe Advanced sind dafür gerüstet – angefangen vom 0,6 Millimeter starken Kraftboard bis hin zur 5 Millimeter starken Wellpappe.
Kraftkartons contra Wellpappekartons
Generell verfügen Kraftkartons gegenüber Wellpappekartons über bessere Feuchtigkeitseigenschaften. Was Kraftkartons als so genannte „Fridge Packs“ geradezu prädestiniert. Bei „Fridge Packs“ handelt es sich um Wrap-Around-Verpackungen aus Kraftkarton – in der Regel für Dosen und PET-Flaschen –, die nach einem Einkauf inklusive verpackter Produkte üblicherweise direkt in den Kühlschrank gelangen. Meist ist in das „Fridge Pack“ eine Perforation mit integriert, welche die Öffnung der Verpackung und damit verbunden den direkten Zugriff auf die Produkte zulässt. Beliebt sind „Fridge Packs“ insbesondere in den USA sowie in den Märkten Lateinamerikas. Für einen Einsatz von Kraftkartons für Wrap-Around-Verpackungen spricht auch deren glatte Oberfläche. Sie begünstigt die Aufbringung von Werbebotschaften und die perfekte Kommunikation der Verpackung mit dem Verbraucher.
Wellpappekartons sind in der Regel dickwandiger gestaltet als Kraftkartons. Wrap-Around-Verpackungen aus Wellpappe werden daher besonders gerne eingesetzt, wenn ein erhöhter Produktschutz z. B. bei Glasflaschen gefordert ist. Gerade in Zeiten der Globalisierung sind Lieferungen über den gesamten Erdball hinweg keine Seltenheit. Ob ein Transport per Seeweg, mittels LKW oder per Luftfracht – Gefahren, denen Produkte ausgesetzt sind, lauern überall. Entsprechend gestaltete Wrap-Around-Verpackungen fangen diese Gefahren ab und gewährleisten, dass verpackte Produkte am Bestimmungsort nichts an Attraktivität verloren haben. Bei zu erwartenden besonderen Strapazen bieten der zusätzliche Einsatz von Gefachen bzw. Stegen in die Wrap-Around-Verpackung ein noch weitergehendes Plus an Transportsicherheit. Üblicherweise verfügen Wrap-Around-Verpackungen aus Wellpappe über Aufreißperforationen, die im Handel geöffnet werden. Dadurch ist die direkte Zugriffsmöglichkeit auf in Wrap-Around-Verpackungen enthaltene Produkte für den Konsumenten gegeben.
Neben optimierter technischer Lösung die perfekte Beratungsleistung
Lassen sich mit WrapAroundPacker und WrapAroundShrinkPacker der neuen Baureihe Advanced auch unterschiedlichste Kartonmaterialien verarbeiten, bedeutet das auf der anderen Seite, dass jedes Unternehmen hier die „Qual der richtigen Auswahl“ hat. Aus diesem Grund liefert KHS neben optimierter technischer Lösung stets auch das entsprechende Know-how zu Verpackungsmaterial. Angefangen bei der Art und Stärke des Kartonmaterials für definierte Vorhaben bis hin zu Know-how in Hinblick auf Kartonform, Perforationen, Gefache und und und. Vor dem Einsatz ausgewählter Materialien im Produktionsbetrieb steht in der Regel der Testbetrieb im KHS-Werk. So ist von Beginn an Verarbeitungssicherheit gegeben. Investitionen in unzulängliches Verpackungsmaterial kommen erst gar nicht vor.
Auch Tray- und Tray-Shrink-Verpackungen sind machbar
Maximale Flexibilität – ein Aspekt, der sich durch die Konzeption von WrapAroundPacker und WrapAroundShrinkPacker gemäß Advanced Baureihe wie ein roter Faden zieht. So überzeugt das Konzept unter anderem auch, weil sich innerhalb jeder der beiden Verpackungsmaschinen neben Wrap-Around- und Wrap-Around-Shrink- auch Tray- und Tray-Shrinkverpackungen bilden lassen. Einzige Einschränkung: Eine Tray-Randhöhe von 40 Millimetern darf nicht unterschritten werden. Was bedeutet, dass etwa 90 Prozent aller im Markt gängigen Tray-Applikationen auf den neuen Maschinengenerationen zu verarbeiten sind.
Produktgruppierung per Multi-Servo-Abteileinheit
Steht eine Verpackung von Produkten in Wrap-Around-Verpackungen an, werden WrapAroundPacker bzw. WrapAroundShrinkPacker die Produkte per Drängelprinzip zugeführt und in Gassen verteilt. Es folgt die Produktgruppierung mittels Multi-Servo-Abteileinheit. Diese Abteileinheit ermöglicht je nach Anforderung durch das zu verarbeitende Produktspektrum den Einsatz von bis zu vier Servomotoren. Das bietet höchste Flexibilität und lässt Geschwindigkeiten von über 100 Takten pro Minute bei der Gruppierung von kleinen und großen Produktgruppen sowie äußerst schonendes Produkthandling zu. Besonders vorteilhaft ist der Einsatz dieser neu entwickelten Multi-Servo-Abteileinheit bei der Bildung einer Vielzahl an Produkteinheiten unterschiedlicher Größen auf einer Maschine. Das kommt der Effizienz der Maschine direkt zugute und bewirkt gleichzeitig, dass die dem WrapAroundPacker bzw. WrapAroundShrinkPacker nach- und vorgeschalteten Maschinen jederzeit bei voller Leistung produzieren können.
Identische Servomotoren mit integrierten Servoreglern im Einsatz
Äußerst vorteilhaft ist zudem die Tatsache, dass bei gemäß der Baureihe Advanced gestalteten Verpackungskonzepten generell identische Servomotoren mit jeweils integrierten Servoreglern zum Einsatz gelangen. Die Verbindung von Servomotor und Servoregler in einer Einheit erleichtert die Fehlersuche im Fall einer Störung sowie den Austausch im Wartungsfall. Nicht zuletzt wird hierdurch auch die Ersatzteilbevorratung deutlich reduziert.. Nachdem sich die Servoregler nun nicht mehr – wie bislang üblich – im Schaltschrank befinden, ist der Verkabelungsaufwand innerhalb der Verpackungsmaschinen deutlich verrringert. Zudem lässt sich der Schaltschrank kleinflächiger auslegen und es kann – außer in tropischen Regionen – auf ein Klimagerät zur Kühlung verzichtet werden. Das wiederum verhilft dazu, Strom- und Wartungskosten zu senken.
Durchdachte Zuschnittzuführung, geringe Bedienerbindung
Direkt unterhalb der Gruppierstation findet die Vereinzelung von Wraparound- oder Trayzuschnitten statt. Die Vereinzelung der Zuschnitte kann auf unterschiedliche Art und Weise vonstatten gehen. Bei vertikaler Anordnung der Zuschnitte innerhalb des Magazins werden diese über ein Saugsystem abgezogen und taktweise in die Transportkette eingelegt. Dabei handelt es sich um eine Vorgehensweise, die insbesondere für WrapAroundPacker und WrapAroundShrinkPacker im niedrigen und mittleren Leistungsbereich zum Tragen kommt. Für hohe Leistungen unabdingbar: die horizontale Anordnung von Zuschnitten innerhalb des Magazins und der automatische Abzug einzelner Zuschnitte über ein Riemensystem. Für ein perfektes Eintakten der Zuschnitte in die Transportkette sorgen bewährte Spezialriemen mit einer sehr griffigen Oberfläche, angetrieben durch einen Servoantrieb. Eine hohe Produktionssicherheit gewährleisten optoelektronische Sensoren innerhalb des gesamten Zuschnitttransports. Insbesondere für Höchstleistungs-Maschinen besteht die Möglichkeit, über 2.000 Zuschnitte auf einer dem Zuschnittvereinzelungssystem vorgeschalteten Transportbahn zu magazinieren. Zugeführt werden dem Zuschnittvereinzelungssystem die gelagerten Zuschnitte mittels automatischer Beladung. Geht man von einer Maximalleistung des WrapAround- bzw. WrapAroundShrinkPackers aus, die bei 100 Takten/Minute liegt, kommt die Maschine bei vorgelagerten 2.000 Zuschnitten 20 Minuten lang ohne Bedienperson aus. Soll in diesem Bereich keine Bedienerbindung mehr stattfinden, gibt es auch die Möglichkeit einer Roboterbeladung an der Transportbahn.
Produktgruppen zu jedem Zeitpunkt fest gehalten und sicher geführt
Ob ein Abziehen von Zuschnitten mittels Saugeinheit oder per Riemensystem vorgesehen ist – stets werden Zuschnitte exakt in eine Mitnehmerkette getaktet, so dass sie mit den innerhalb der Gruppierstation gebildeten Produktgruppen zeitgleich zusammentreffen. Besonderheit dieses Verpackungsprozesses: Die Produkte sind zu jedem Zeitpunkt fest gehalten. Fehlende Behälter im Karton werden ausgeschlossen. Dafür sorgen unter anderem Faltketten an denen spezielle Faltmitnehmer befestigt sind, welche über Kurven gesteuert werden. Sobald eine Produktgruppe in den Zuschnitt einläuft, regelt einer der Faltmitnehmer, dass der vordere Bereich des Wrap-Around-Zuschnitts nach oben gefaltet wird. Gleichzeitig sind hintere Produkte der Formation über einen Stab fixiert. Ist die Produktformation perfekt auf dem Zuschnitt positioniert, verschließt ein weiterer Faltmitnehmer den hinteren Zuschnittbereich. Ein beiderseitiges leichtes seitliches Anheben der Zuschnitte geschieht während der Zusammenführung von Zuschnitt und Produktgruppe über spezielle Faltkurven.
Die über Kurven gesteuerten Faltmitnehmer erlauben ein flexibles Agieren. So veranlassen sie, dass sich Vorder- und Hinterseite jedes Zuschnittes direkt nach Einspeisung der Produktformation nochmals geringfügig öffnen, um das korrekte Einfalten der Klebelaschen zu ermöglichen. Es folgt der Leimauftrag über spezielle Heißleimauftragsköpfe und ein endgültiges Schließen von Vorder- und Hinterseite der Wrap-Around-Verpackung im 90 Grad-Winkel. Nächster Schritt ist die Faltung und Verklebung des Deckels. Der WrapAroundKarton ist geformt und verklebt und durchfährt nun die Andrückstrecke.
Während des geschilderten Prozesses sind Produkte zu jedem Zeitpunkt sicher geführt. Gerade bei einem Verpacken in die Wrap-Around-Verpackung ist dies von allerhöchster Bedeutung. Denn ist ein Wrap-Around-Karton erst einmal verschlossen, lässt es sich optisch nicht mehr nachvollziehen, ob wirklich alle vorgesehenen Produkte eingebracht sind. Eine Prüfung wäre nur über den Wiegevorgang machbar. Was neben dem erhöhten Arbeitsaufwand eine Steigerung von Investitionskosten bedeuten würde.
Ob Breit- oder Längsseite führend – für Tray-Verpackungen bestehen beide Optionen
Zu der Bildung von Wrap-Around-Verpackungen managen WrapAroundPacker und WrapAroundShrinkPacker bei Bedarf auch die Verpackung von Produkten in Tray- bzw. Tray-Shrink-Verpackungen. Hier bestehen generell zwei Möglichkeiten der Verarbeitung. Zum einen lassen sich Tray-Zuschnitte ebenso wie Wrap-Around-Zuschnitte mit der Schmalseite führend in die Maschine einbringen. Für diesen Fall sind identische Tray-Zuschnitte, die in TrayPackern bzw. TrayShrinkPackern zum Einsatz gelangen, auch für WrapAroundPacker bzw. WrapAroundShrinkPacker geeignet. Zum anderen lassen sich speziell für WrapAroundPacker bzw. WrapAroundShrinkPacker gestaltete Tray-Zuschnitte mit der Breitseite führend verarbeiten.
Vorteilhaft ist die Lösung „Breitseite führend“ vor allem dann, wenn die mit Produkt bestückte Tray-Verpackung noch geshrinkt werden soll. Breitseitig geführt geht es für die Tray-Verpackung direkt zum Folieneinschlag. Längsseitig geführt muss die Tray-Verpackung vor Einbringung in die Folienstation gedreht werden. Damit ist die Integration einer zusätzlichen Drehstation in das Maschinenkonzept notwendig. Gegenüber der „klassischen Lösung“ erhöht das Platz- und Zeitbedarf. Vorteile bietet diese Lösung auch bei der Gestaltung der Zufuhr von vorverpackten Produkten. Beispielsweise müssten auf einem vorgeschalteten ShrinkPacker produzierte, in Folie eingeschlagene Sixpacks nicht mehr gedreht werden bevor sie zum WrapAroundPacker gelangen.
Generell wird bei der Bildung von Tray-Verpackungen in WrapAroundPacker bzw. WrapAroundShrinkPacker eine ähnliche Vorgehensweise wie bei der Bildung von Wrap-Around-Verpackungen praktiziert. Wobei hier die obere Abbindestrecke nicht benötigt wird und Faltwerkzeuge sowie Heißleimdüsen in einer Art und Weise positioniert sind, die sich an Tray-Vorgaben anpasst.
Zügige Formatumstellung
Entgegen kommt einer schnellen Umrüstung von Verpackungstechnik von der Tray- bzw. Tray-Shrink- auf die Wrap-Around- bzw. Wrap-Around-Shrink-Verpackung (oder umgekehrt) die innerhalb des Advanced-Konzepts integrierte zügige Formatumstellung. Wählen lässt sich zwischen mechanischer und bedienergeführter Variante. Vorteil bei der bedienergeführten Formatumstellung: Der Bediener erhält bereits über das Bedienpult der Maschine Auskünfte dazu, wo genau neu eingestellt werden muss. Gleichzeitig wird bei der bedienergeführten Formatumstellung mittels elektronischer Anzeige exakt kommuniziert, wie an einzelnen Stationen zu verstellen ist. Eventuelles Spiel in Zahnrädern oder Ketten ist bei den entsprechenden Anweisungen – und das ist ein zusätzliches Plus – schon mit berücksichtigt. Wahlweise sind Verstellungen bei der bedienergeführten Formatumstellung manuell oder mittels Accu-drive zu realisieren. Neu ist auch die Verstellung der Faltstation in Laufrichtung, welche künftig einfach über die Formatauswahl am Bedienpult realisiert wird. Die Servomotoren stellen die Falt- und Andrückketten quasi per Knopfdruck auf die neuen Abstände für andere Formationen ein.
Folieneinschlag-Modul mit zahlreichen Besonderheiten
Einziger Unterschied zwischen WrapAroundPacker und WrapAroundShrinkPacker der Baureihe Advanced ist das beim WrapAroundShrinkPacker in das System mit integrierte Funktionsmodul Folieneinschlag und der dem Folieneinschlagmodul direkt nachgeordnete Schrumpftunnel. Neben dem Folieneinschlag einzelner Tray- und einzelner Wrap-Around-Verpackungen ist mit dem WrapAroundShrinkPacker auch der Einschlag mehrerer Wrap-Around-Verpackungseinheiten in Folie machbar. Praktiziert wird dies beispielsweise, wenn die Palettierkapazität für die Verarbeitung separater kleinerer Wrap-Around-Verpackungen nicht genügt oder für gesammelte Wrap-Around-Verpackungen der ganz besondere Schutz einer hochwertigen Bedruckung sein soll. Um ein „mehrfach Einpacken“ verwirklichen zu können, wird noch vor dem Folieneinschlag-Prozess ein Funktionsmodul „Sammelstation“ in das System integriert. Das Stapeln von zwei Trays vor dem Folieneinschlag lässt sich durch die Einbringung des Funktionsmoduls Stapeln in das Konzept durchführen. Hierdurch reduziert sich auch der Verbrauch von Verpackungsmaterial und die Anforderung an die Geschwindigkeit des Palettierers.
Verarbeitung von besonders dünnwandiger Folien ist möglich
In Bezug auf den Folieneinschlag-Prozess hat die Baureihe Advanced einmal mehr Besonderes zu bieten. Hier lassen sich wesentlich dünnere und breitere Folien verarbeiten als bislang möglich. Bis zu einer Folienstärke von 35 µm und einer Folienbreite von 950 mm sind perfekte Verarbeitungsergebnisse gewährleistet. Bewegungsabläufe regeln sich in der kontinuierlich arbeitenden Folienstation über eine elektronische Kurve. Folienabschnittslänge und Druckbildpositionierung sind innerhalb des Systems per Formatanwahl am Bedienpult elektronisch einzurichten. Ein über Servoantrieb angesteuertes Folienschneidemesser sorgt für den präzisen Folienschnitt. Denkbar ist bei der Baureihe Advanced auf Wunsch hin die Integration einer Folienrollen-Endkontrolle. Eine auf elektrostatischer Basis arbeitende Abfrage registriert die speziell hierfür in die Folie eingebrachte Perforation. Es folgt ein automatischer Maschinenstopp für den Wechsel der Folienrolle. Vorteil: die gezielte Einsparung an Folienmaterial von durchschnittliches 0,8 Kilogramm pro Rolle und damit verbunden die gezielte Einsparung von barem Geld.
Öko-Schrumpftunnel bietet Energiekosteneinsparung bei gleichzeitiger Reduzierung des CO2-Ausstoßes
Bares Geld lässt sich zudem einsparen, wenn nach dem Folieneinschlag-Funktionsmodul statt klassischem Schrumpftunnel mit Elektro-Beheizung der so genannte Öko-Schrumpftunnel zum Tragen kommt, der auf Gas-Beheizung setzt. Seinem Namen wird das Öko-Schrumpftunnel-Konzept gerecht, weil sich gegenüber der herkömmlichen Schrumpftunnelvariante eine Energiekosteneinsparung von bis zu 50 Prozent erreichen lässt. Zudem profitiert die Umwelt von einer deutlichen Reduzierung des CO2-Ausstoßes.
Das wandelbare Gesamtkonzept
Generell sind Verpackungslösungen der Advanced Baureihe dadurch gekennzeichnet, dass eine an individuelle Bedürfnisse angepasste Verpackungstechnik durch einfache Integration von Funktionsmodulen zu erreichen ist. So besteht für den WrapAroundPacker und den WrapAroundShrinkPacker der Baureihe Advanced jederzeit die Möglichkeit, vorhandene Verpackungstechnik durch weitere Funktionsmodule auszubauen. Im Gegenzug besteht die Option, nicht mehr benötigte Funktionsmodule aus dem System zu entfernen. Was zeigt, dass es sich bei der Advanced Baureihe um ein Konzept handelt, das in jeder Hinsicht wandelbar ist. Beispielsweise denkbar: die Integration eines Gefache-Inserters in das Maschinenkonzept. Vor allem, wenn auf weiten Transportstrecken ein ganz besonderer Produktschutz gefordert ist, ist dieses Funktionsmodul für Wrap-Around-Verpackungen gefragt. Positioniert wird ein Gefache-Inserter direkt über den Transporteuren der zu verarbeitenden Verpackungen. Zusätzlicher Platz für das System ist nicht erforderlich.
Kubischer Maschinenkörper für maximale Bedienerfreundlichkeit
Ebenfalls ein entscheidender Vorteil der Advanced Baureihe: die kubische Gestaltung des Maschinenkörpers. Für WrapAroundPacker und WrapAroundShrinkPacker, deren Arbeitsweise einbahnig ist, liegen die Pluspunkte dieser Bauweise in einer nochmals gesteigerten Bedienerfreundlichkeit begründet. So steht das kubische Maschinendesign für mehr Raum in der Maschine. Außerdem lassen die Schutzhauben während der Produktion einen hervorragenden Einblick in die Maschine zu. Dazu kommt: Nach oben schwingende Schutzhauben sind für Bediener leichter zu öffnen sowie zu schließen und ermöglichen den optimalen Zugang in jeden Bereich der Maschine.
Künftig das noch größere Multitalent?
Ist heute für WrapAroundPacker und WrapAroundShrinkPacker gemäß Advanced Baureihe mit Wrap-Around-, Wrap-Around-Shrink-, Tray- und Tray-Shrink-Verpackung bereits ein breites Spektrum an unterschiedlichen Verpackungsvarianten realisierbar, könnte dieses Spektrum in Zukunft sogar noch breiter werden. Aktuell prüft KHS, ob eine zusätzliche Verarbeitung von Pad-Shrink- und reinen Shrink-Verpackungen möglich ist. Was heißt, dass WrapAroundPacker und WrapAroundShrinkPacker gemäß Advanced Baureihe künftig als noch größere Multitalente im Markt auftreten könnten. Dank Modulbauweise profitieren – und das ist wohl das alles entscheidende Plus – auch in Zukunft sämtliche im Markt befindliche Advanced Verpackungssysteme von neuen Möglichkeiten direkt mit.