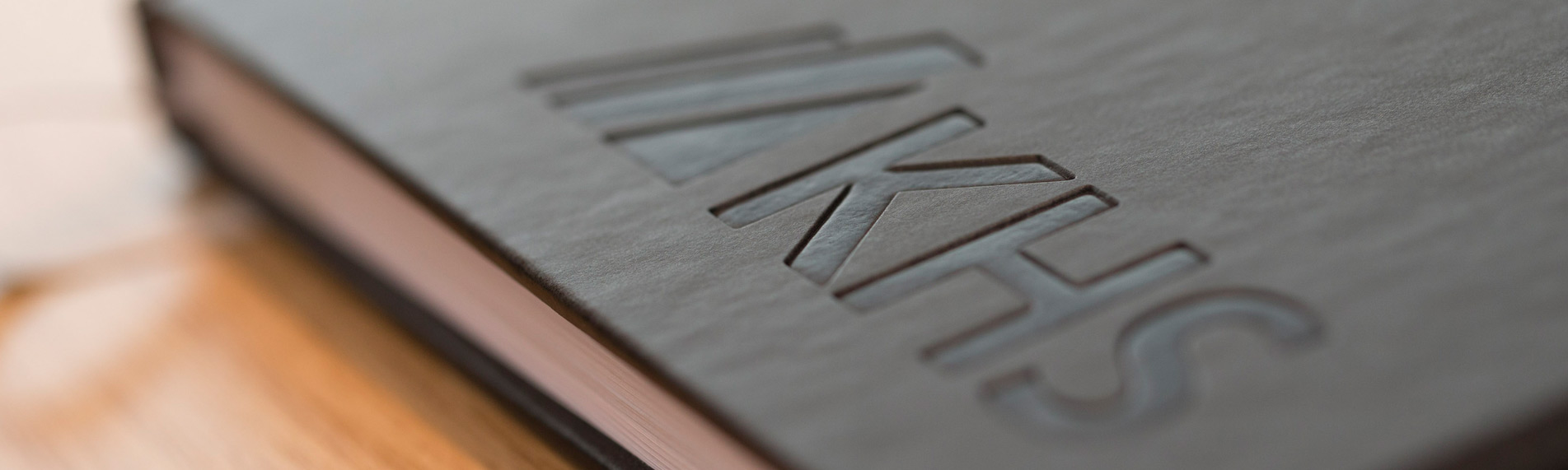
Einfachheit im Vordergrund
Hygienic Design in der Fülltechnik
Ludwig Clüsserath* Gemäß Definition der Deutschen Gesellschaft für Hygiene und Mikrobiologie ist Hygiene die „Lehre von der Verhütung der Krankheiten und der Erhaltung und Festigung der Gesundheit.“ Ursprünglich stammt der Begriff Hygiene aus dem Griechischen und geht auf Hygeia, Göttin der Gesundheit, zurück. Was unter anderem demonstriert, dass Hygiene bereits im Altertum ein bedeutendes Thema darstellte. Heute steht in Hinblick auf die Gewährleistung höchster hygienischer Maßstäbe im Betrieb vor allem die Lebensmittel erzeugende Industrie im Fokus. Eine wesentliche praktische Anwendung betrifft hier die Realisierung von Hygienic Design im Bereich der Maschinen- und Anlagentechnik. Zur Umsetzung von Hygienic Design unabdingbar: einfache Konstruktionsprinzipien; der freie Zugang zu sämtlichen Maschinenoberflächen zum Zweck der Reinigung, Desinfektion und Kontrolle; der Verzicht auf Maschinenoberflächen wo immer machbar; die Eliminierung versteckter Konstruktionsbereiche, in denen sich Ablagerungen und Biofilme bilden können sowie ein freier Ablauf von Flüssigkeiten. Wie sich gelungenes Hygienic Design im Praxisbetrieb darstellen kann, beleuchtet dieser Artikel beispielhaft für den Bereich der Getränke-Abfülltechnik. Dabei geht es sowohl um grundlegendes Wissen als auch um gelungene technische Lösungen, die sich ganz an Hygienic Design-Maßstäben orientieren. Wesentliches Kriterium im Wettbewerb Hygienic Design ist in Bezug auf die Wettbewerbsfähigkeit von Unternehmen ein wichtiges Kriterium. Bedeutendstes Ziel bei der Umsetzung von Hygienic Design bildet stets der optimierte Verbraucherschutz. Ein weiterer Aspekt betrifft den Gesundheitsschutz der Mitarbeiter in den Produktionsbetrieben. Aus wirtschaftlicher Sicht lohnt sich Hygienic Design nicht nur, weil mikrobiologische Risiken ausgeschaltet sind, sondern auch aufgrund der einfachen und zügigen Reinigungsmöglichkeit von Maschinen und deren Bauteilen. Denn kurze Reinigungszyklen schlagen sich in verlängerten Produktionszeiten und schließlich in einer erhöhten Effizienz von Anlagentechnik direkt nieder. Definition unterschiedlicher Hygienebereiche Die europäische Norm DIN EN 1672-2 (Hygieneanforderungen an Nahrungsmittelmaschinen) definiert für Maschinen und Anlagen, die mit* Leiter Competence Center Prozesstechnik, KHS AG, Bad Kreuznach, Tel.: 06 71/8 52 25 01 Lebensmitteln in Kontakt kommen können, eine klare Einteilung in unterschiedliche Hygienebereiche. Dieser Einteilung haben technische Lösungen Rechnung zu tragen. Zone A betrifft den unmittelbaren Lebensmittelbereich, von dem aus kontaminiertes Produkt zurück in den Hauptproduktstrom gelangen können. Tritt dort eine Kontamination auf, ist Produkt direkt mit einbezogen und die Sicherheit des Verbrauchers gefährdet. Auf die Getränkeindustrie übertragen zählen zur Zone A beispielsweise Rohrleitungen und Behälter, in denen Produkt fließt oder auch der Bereich der Füllventile in unmittelbarer Nähe zur offenen Flasche oder Dose. Zone B stellt den so genannten „Spritzbereich“ dar. Von diesem Bereich aus kann Produkt nicht mehr auf direktem Wege in den Hauptproduktstrom zurückgelangen. Da Produktspritzer aber ebenfalls mikrobiologisches Wachstum initiieren können, besteht allerdings die Gefahr, dass durch Eingriffe oder Manipulationen innerhalb der Zone B Keime in die Zone A eingetragen werden. Beispielsweise gehören der Zone B Maschinenverkleidungen und Sternwellen an. Außerhalb genannter Gefährdungszonen liegt schließlich die Zone C, die sich als „Nicht-Lebensmittelbereich-Zone“ definiert. Getränkeindustrie-Beispiele für die Zone C: der Außenbereich der Füllereinhausung oder auch die vor der Füllereinhausung befindlichen Flaschentransporteure. Von Grund auf einfach Die Umsetzung von konsequentem Hygienic Design ist insbesondere in den Bereichen der Zone A und der Zone B erforderlich. Wobei das Grundprinzip von konsequentem Hygienic Design stets konsequente Einfachheit bedeutet. Das Beispiel eines Trichters verdeutlicht dies. Trichter sind hygienegerecht, weil sie über schräg aufeinander zulaufende glatte Flächen verfügen, mit deren Hilfe Flüssigkeit zügig und auf hygienische Art und Weise in Gefäße einzubringen ist. Ecken und Kanten, die hygienische Risiken darstellen, kommen hier erst gar nicht vor. Ein einfacher Zugang für die Reinigung ist machbar. Ähnlich einfach gestaltet sich auch die Logik bei der Konstruktion von Fülltechnik gemäß Hygienic Design. Beispielhafte Lösungen Beispielsweise hat bei der Konstruktion von Fülltechnik gemäß Hygienic Design die Anordnung von Dichtungen durchdacht stattzufinden. Ob Verbindung in Füllventilteilen, Verbindung von Rohrleitungsflanschen oder Anschluss von Armaturen oder in Behältern – überall sind Dichtungen oder Membranen erforderlich. Betrachtet man speziell den Bereich der Dichtungen, erfüllen übliche O-Ringe zwar die Dichtfunktion, bedingt durch ihre O-förmige Gestaltung ergeben sich bei ihrem Einsatz in klassische Nuten jedoch in der Regel Spalten. Ein ideales Reservoir für Produktreste und Mikroben. Die Hygienic Design-Lösung lautet hier: O-Ring Nuten werden derart gezielt ausgeformt, dass sich O-Ringe direkt an sie anlegen. Spalten kommen nicht vor. Hygienic Design ist gegeben. Dieses Prinzip gilt natürlich auch für andere Dichtungsgeometrien. Ein weiteres einfaches Beispiel für die perfekte Umsetzung von Hygienic Design in der Fülltechnik ist das hygienegerechte Verschweißen von Rohrleitungen und Blechkonstruktionen. Die glatte Verschweißung ist hier ein Muss. Jede Unebenheit und jeder Versatz birgt ganz klare Kontaminationsrisiken in sich. Ebenfalls eine einfache Hygienic Design-Lösung für den Füllerbereich: die Ableitung von Flüssigkeiten mit Hilfe von Schrägen nach dem Trichterprinzip. Unterhalb von Produktabläufen entstehen auf diese Art und Weise erst gar keine Sümpfe. Von Konstruktionsbeginn an die gleichwertige Berücksichtigung von Funktion und Hygienic Design Soll Hygienic Design bei technischen Lösungen in vollem Umfang integriert werden, gilt es diesen Punkt bei Konstruktionen von Neumaschinen von Anfang an mit zu berücksichtigen. Und das konsequent, denn ohne eine ganzheitliche Betrachtung kein perfektes Hygienic Design. Maschinenfunktionen sind in jeder Phase ihrer Entwicklung nach Hygienic Design-Tauglichkeit und damit verbunden nach einer zügigen Möglichkeit der Reinigung und Sterilisation zu hinterfragen. Nur so kann schließlich eine Maschine entstehen, bei der sich Funktionen ebenso perfekt darstellen wie deren hygienische Gestaltung. Betrachtet man die heute im Markt befindlichen modernen rechnergesteuerten Füllsysteme, ist der Hygienic Design-Gedanke dort in der Regel gelungen berücksichtigt. Glatte und wenig komplexe Oberflächen, ein freier Zugang für Reinigungs- und Desinfektionsmaßnahmen, der freie Ablauf von Flüssigkeiten – all’ das erfährt höchste Beachtung. Vom mechanischen … Die Historie der Fülltechnik zeigt, dass einige Entwicklungsstufen nötig waren, um zu heutigen Hygienic Design-Möglichkeiten zu gelangen. Beispielsweise erfolgt bei mechanischen Füllsystemen die Regelung des gesamten Füllprozesses noch über mechanische Elemente wie Schalthebel, Schaltstößel, Kurven und Steuerungen. Diese Elemente werden in der Regel über die Rotation des Füllsystems geschaltet. Was heißt, dass eine hohe Komplexität innerhalb des Zone A-Bereiches herrscht und Spalten und Ecken vorhanden sind, in denen sich Schmutz sammeln kann. Unter anderem sind hier aufwändige manuelle Reinigungsschritte, die bis hin zur Demontage einzelner Bauteile gehen, zur Gewährleistung einer hohen Produktsicherheit notwendig. …über das pneumatische… Aus dem Blickwinkel von Hygienic Design betrachtet war die Entwicklung pneumatischer Füllsysteme ein bedeutender Schritt. Schalthebel und Stößel wurden bei pneumatischen Füllsystemen durch pneumatische Zylinder ersetzt. Die Kraftübertragung von den Zylindern in den Hygieneraum geschieht mittels Membranen. Was bedeutet, dass sich keine Bauelemente mehr von außen nach innen bewegen. Nach wie vor Tatsache: Füllventilbauteile, Federn und auch Führungsteile befinden sich im Getränkeweg. Kritische Bereiche sind hier also noch vorhanden. …bis hin zum rechnergesteuerten Füllsystem Moderne rechnergesteuerte Füllsysteme stellen aus Sicht des Hygienic Design im Vergleich zu bislang Vorhandenem die optimale Lösung dar. Hygienic Design erfährt hier sowohl im Innen – im Bereich der Füllventile – als auch im Äußeren die konsequente Umsetzung. Unter anderem beispielhaft für gelungenes Hygienic Design ist das rechnergesteuerte volumetrische KHS-Füllsystem Innofill DRV, das von der 0,1-l- bis hin zur 5-l-Kunststoff-Flaschen-Variante die Verarbeitung sämtlicher Kunststoff-Flaschengrößen und -formen realisiert. Eine große Vielfalt an Hygienic Design-Komponenten ergeben hier das gelungene Gesamtpaket. Gleichermaßen hygienisch aufgebaut ist auch das Sondenfüllsystem Innofill DRS zur Abfüllung von Bier und Softdrinks in Glasflaschen. Das Innofill DRV „Hygienic Design-Paket“ Das Füllsystem Innofill DRV verfügt über einen Rohrringkessel mit außen an einem separaten Ventilträger angeflanschten Füllventilen. Hygienischer Hauptvorteil des Rohrringkessels: Im Gegensatz zum Rechteck-Kessel gibt es keine Ecken und Kanten und die Flüssigkeiten laufen immer zum tiefsten Punkt – für den CIP und SIP-Prozess gestaltet sich das geradezu ideal. Neben der Hygiene ist der vergleichsweise geringere Materialeinsatz ein weiterer Pluspunkt des Rohrringkessels. Das bedeutet eine gezielte Kostenreduzierung. So ist der Energieeinsatz bei Aufheiz- und Abkühlphasen des Ringkessels reduziert. Gleichzeitig benötigen Aufheiz- und Abkühlphasen weniger Zeit als beim Rechteck-Kessel üblich. Dazu kommt: Die Leichtbauweise des Rohrringkessels verringert die notwendigen Antriebskräfte, was wiederum den Stromverbrauch sowie Wartungskosten mindert. Geringe Anzahl an Schaltelementen Ebenso mit in das Füllsystem Innofill DRV integriert: ein einfaches Steuerungskonzept, das mit einer geringen Anzahl an Schaltelementen arbeitet. Ist beispielsweise ausschließlich die Abfüllung von klassischen kohlensäurehaltigen Getränken gefordert, kommt das Innofill DRV-VF-Füllventil mit gerade einmal zwei pneumatisch gesteuerten Membranzylindern aus. Diese beiden pneumatischen Funktionen regeln den kompletten Füllprozess – einschließlich Anpresshub und Abdichtung der Flaschenmündung am Füllventil. Möglich wird der Einsatz dieser geringen Anzahl an Schaltfunktionen sowie der Verzicht auf ein Hubelement, weil sich die Kraft, die aus dem Vorspann- und Abfülldruck resultiert, über einen nach aseptischen Kriterien gestalteten Faltenbalg direkt auf den Neckringhalter überträgt. Nicht nur die Flaschen-Hubelemente entfallen, sondern auch die damit verbundenen Baueinheiten und Regeleinrichtungen zur Luft- und Schmierstoffversorgung. Generell gilt: Je weniger pneumatisch gesteuerte Membranzylinder für die Schaltung von Füllventilen nötig sind, umso geringer ist auch die Anzahl der für das Füllsystem wesentlichen mechanischen Elemente und Schlauchverbindungen. Schlauchverbindungen sollten stets außerhalb des Hygienebereichs untergebracht sein. Pneumatische Pilotventile befinden sich idealerweise ebenfalls außerhalb des Hygienebereichs in geschlossenen und leicht zu reinigenden Gehäusen aus Edelstahl. Beides ist für den Innofill DRV so realisiert. Füllung mittels Drallkörper Hygienic Design-Gesichtspunkte standen auch bei der Füllventil-Entwicklung für den Innofill DRV im Vordergrund. Die äußere Gestaltung gewährleistet hier eine effiziente Außenreinigung – mit glatten Flächen an den Gaszylindern, Schrägen für den gezielten Produktablauf und offenen Stangenführungen für den Anpresshalter. Im Inneren des Füllventils finden sich ausschließlich aseptische Dichtungssysteme. Innerhalb des Getränkewegs kommen keine Federn und Führungsteile vor. Eine einzige Sitzdichtung öffnet und schließt das Füllventil. Räume, die Ablagerungen ermöglichen sind nicht vorhanden. Der einfache Reinigungs- und Sterilisationsvorgang ist gegeben. Wege im Füllventil sind äußerst kurz gehalten. Auf diese Art und Weise haben nur wenige Teile und kleine Flächen Produktkontakt. Der Füllprozess geht mittels Drallkörper vonstatten. Das Füllprinzip hier: Nach Öffnung des Füllventils geschieht die Einleitung von Flüssigkeit in die Kunststoff-Flasche über die Flaschenwand. So kommen keine in die Flasche hineinragenden Abstrahlelemente vor. Einfachheit bei Produkt- und Gaswegen Gaswege innerhalb des Füllventils sind für den Innofill DRV ähnlich einfach gestaltet wie Produktwege. Gaszylinder mit spaltfreien Dichtungssystemen steuern den Füllprozess. Hygienisches Design ist unter anderem durch Einsatz von aseptischen Membrantechnologien innen wie außen realisiert. Die gezielte Reinigung der Prozesswege geschieht rechnergesteuert. Aseptischen Kriterien Rechnung getragen Sämtliche rechnergesteuerte KHS-Füllsysteme tragen in der Gestaltung aseptischen Kriterien Rechnung. Hier gehen Dichtungssysteme und Konstruktionsprinzipien mit den Anforderungen einer aseptischen Abfüllung direkt konform. Was einmal mehr demonstriert, dass KHS selbst bei konventioneller Technik nicht etwa auf hygienisch abgespeckte Systeme setzt, sondern hygienisches Design vom Feinsten realisiert. Jedes Teil zählt Die Entwicklung von Füllsystemen gemäß Hygienic Design kann immer nur dann von Erfolg gekrönt sein, wenn auch die in die Füllsysteme integrierten einzelnen Elemente in vollem Umfang Hygienic Design-Anforderungen genügen. Auch hier ist ein stetiges Hinterfragen von vorhandener Technik nötig. Es geht immer um die permanente Neu- und Weiterentwicklung von Lösungen, die sich in ein umfassendes Hygienekonzept perfekt einfügen lassen. Faltenbalg im Einsatz Beispiel für eine Neuentwicklung, die für den Innofill DRV ein weiteres Mehr an Hygiene bedeutet, ist der gemäß aseptischen Kriterien gestaltete Faltenbalg. Ihm ist es zu verdanken, dass Hubelemente und die mit ihnen verbundenen Peripherieelemente ersatzlos gestrichen werden konnten, überträgt der Faltenbalg doch den Druck innerhalb des Füllventils auf aseptischem Weg auf den Anpressmechanismus der Flasche. Der Faltenbalg besteht aus einem verschleißfesten und langlebigen Spezialwerkstoff PTFE, der sich durch hohe Temperaturresistenz, umfassende Beständigkeit gegenüber Reinigungs- und Desinfektionsmitteln und eine Schmutz abweisende Oberflächenstruktur auszeichnet. Während der CIP-Reinigung durchströmen Reinigungsmedien den Faltenbalg tangential. Die optimale Schmutzablösung und -austragung ist gegeben. Zahlreiche an EHEDG (European Hygienic Engineering & Design Group)-Vorgaben angelehnte Laboruntersuchungen bei denen eine Simulation von extremen Verschmutzungen durch Auftrag und Antrockung von beispielsweise Bier-Konzentrat oder Karottenpüree an den Faltenbalg praktiziert wurde, bestätigen dies ebenso wie die Praxis. Neue Sondenlösung Ein weiteres Beispiel für eine Einzelentwicklung, die nun für noch mehr Hygiene sorgt betrifft eine neue Sonde innerhalb des rechnergesteuerten KHS-Füllsystems Innofill DRS. Ehemals üblich: Komplexe Elemente und Dichtungen wurden zu der für den Erhalt eines Schaltsignals notwendigen Trennung der elektrischen Plus/Minus-Pole verwendet. Heute realisiert: Ein Stab in Edelstahl trennt Pole durch eine fest mit ihm verbundene Isolierschicht vollkommen spaltfrei. Maschinenvortisch nicht länger nötig Von hoher Bedeutung für zusätzliche Hygiene ist auch, dass sich heute ganz ohne konventionellen Maschinenvortisch abfüllen lässt. Möglich wurde dies durch die Etablierung von Servotechnik. Dank Servotechnik mit Einzelantrieben können Getriebekästen, große Zahnräder und Gelenkwellen entfallen. Schraubverschließer mit hygienischen Extras Höchste Hygiene im Verschließerbereich gewährleistet der KHS-Schraubverschließer Innofill SV-ACF. Er wurde für den Einsatz mit aseptischen Abfüllmaschinen entwickelt und ist so auch für alle anderen hygienischen Prozesse geradezu prädestiniert. Den hygienischen Anforderungen kommt dabei die grundsätzliche Trennung der Verschließbewegung in Rotationsbewegung des Verschlusses und Vertikalbewegung der Flasche zugute. Jedes Verschließelement verfügt hier über einen eigenen Servoantrieb, der unabhängig von der Maschinengeschwindigkeit ganz an den jeweiligen Verschluss angepasst arbeitet. Umstellungen geschehen beim Innofill SV-ACF auf Knopfdruck. Mechanische Eingriffe sind nicht notwendig. Dazu kommt: Selbst Führungen und Lager des Verschließers sind offen gestaltet und frei zugänglich für optimierte Reinigungsverfahren. Weitergehende Automatisierung von Prozessen Der Mensch als Kontaminationsrisiko – eine Tatsache, die eine immer noch weitergehende Automatisierung von Prozessen geradezu fordert. Beispiele, die dem Rechnung tragen: Statt einem manuellen Einsetzen von Spülhülsen vor dem Reinigungsprozess kommt die automatische Spülkappeneinbringung zum Tragen. Die Umrüstung auf ein neues Füllverfahren, beispielsweise von Normaldruck- auf Gegendruckfüllung, erfolgt vollautomatisch. Die Umschaltung zwischen Flaschen mit verschiedenen Mündungen passiert auf Knopfdruck. Alle diese Maßnahmen stehen nicht nur für maximale Hygiene und optimiertes Hygienic Design, sondern tragen gleichzeitig auch die erhöhte Anlagenverfügbarkeit mit in sich. Einfache Lösungen, große Wirkung Was wiederum demonstriert – und hier schließt sich der Kreis – dass Hygienic Design vor allem eines bedeutet: die Realisierung einfacher Lösungen, die zumeist sogar noch Kosten reduzierend wirken. Weil die Effizienz von Anlagen durch konsequent praktiziertes Hygienic Design in der Regel ansteigt. Einerseits bedingt durch einfachere und zügiger durchzuführende Reinigungsvorgänge. Andererseits bedingt durch eine geringere Komplexität von technischen Lösungen und einem damit verbundenen minimierten Einsatz von Verschleißteilen. Vorteile über Vorteile, die für die Getränkebranche ebenso wie für die Lebensmittelbranche letztlich klare Wettbewerbsvorteile bieten.