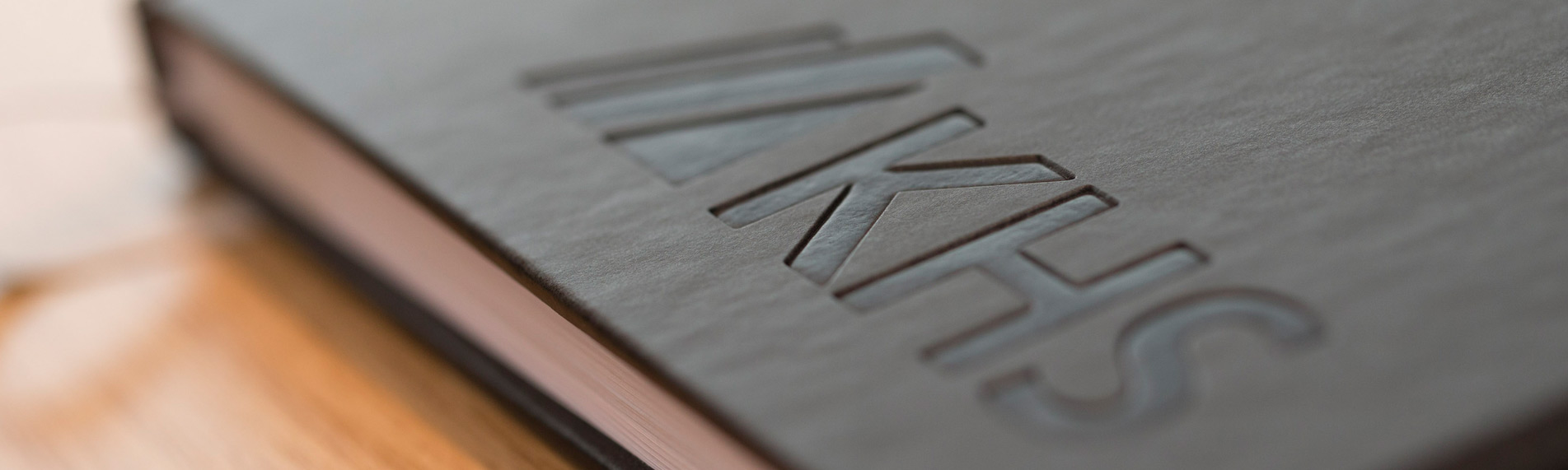
Für Premium-Spirituosen die Premium-Verpackungstechnik
Beam, größtes Spirituosenunternehmen in den USA, setzt auf KHS-Verpackungstechnik
Georg Zuzok*Steve Humbert** Es war im Jahr 1795 als der deutschstämmige Johannes Jacob Böhm, der sich in Jacob Beam umbenannt hatte, in Kentucky, USA, sein erstes Fass Whiskey verkaufte und damit den Grundstein zu einer bis zum heutigen Tag andauernden Erfolgsgeschichte der Whiskeymarke Jim Beam legte. Jim Beam agiert derzeit als weltweite Nummer Eins unter den Bourbon Whiskeys und wird mittlerweile in siebter Generation von dem Unternehmen Beam produziert. Zur ursprünglichen Marke Jim Beam White Original gesellen sich innerhalb des Beam-Sortiments zwischenzeitlich nicht nur zahlreiche weitere Jim Beam Bourbon-Varianten, sondern auch viele andere Spirituosenmarken. Hergestellt und abgefüllt werden die Markenprodukte auch heute noch zu einem großen Teil in Kentucky. Die bedeutendste Produktionsstätte von Beam ist hier das im Jahr 1901 gegründete und in Frankfort angesiedelte „Old Grand Dad“-Werk. Von hier aus gehen jährlich ca. 12 Millionen mit Spirituosen befüllte Kartonverpackungen (ein Karton Spirituosen enthält im Durchschnitt 9 Liter) an Handel, Gastronomie und Verbraucher. Somit werden in Frankfort über die Hälfte aller in Kentucky und etwa 30 Prozent der weltweit hergestellten Beam-Spirituosen abgefüllt und verpackt. Byron DuBois, Leiter des Werks Frankfort: „Um den vorgegebenen hohen Output zuverlässig zu erreichen, benötigen wir technische Lösungen, auf die wir uns 100-prozentig verlassen können. Daher entschieden wir uns bei unseren jüngsten Investitionen in Verpackungstechnik auch für Wrap-Around-Packer von KHS. Seit 2010 ordern wir ein KHS-Verpackungssystem nach dem anderen. Mittlerweile sind wir in unserem Werk bei vier KHS-Wrap-Around-Packern angelangt, die unsere hochwertigen Produkte nicht nur perfekt verpacken, sondern die gleichzeitig höchst effizient arbeiten. Wir sind hier äußerst zufrieden.“ * Leiter Market Zone Americas, KHS GmbH, Bad Kreuznach, Tel. 06 71-8 52-22 02 ** Direktor Verpackungstechnik, KHS USA, Inc., Tel: +1/5 13 – 2 88 89 31
50 Prozent des in Kentucky produzierten Bourbons gehen auf das „Jim Beam-Konto“ Generell gilt Bourbon Whiskey in den USA als heimische Spirituose mit Geschichte. Das bestätigte im Jahr 1964 der US-Kongress. Noch heute sind 98 Prozent aller Bourbon Destillerien in den USA im Staat Kentucky angesiedelt. Landläufig wird behauptet, dass es hier mehr Bourbon-Fässer als Einwohner gibt. Etwa die Hälfte des jährlich in Kentucky produzierten Bourbons verbucht die Markenfamilie Jim Beam auf sich. Zu ihr zählen neben dem Klassiker Jim Beam White Original zwischenzeitlich Jim Beam Rye, Jim Beam Black, Jim Beam Devil’s Cut sowie Red Stag by Jim Beam in den Geschmacksvarianten „Black Cherry“, „Honey Tea“ und „Spiced“. Weltweiter Jim Beam-Spirituosenabsatz bei mehr als 7 Millionen Kartons 2012 verkaufte Beam mehr als 7 Millionen mit Jim Beam-Spirituosen befüllte Kartons in die ganze Welt. Für 2013 wird mit einem nochmaligen Absatzplus kalkuliert. Auch weil die Nachfrage nach Bourbon sowohl in den USA als auch international – hier insbesondere in Stamm-Märkten wie Deutschland und Australien – kontinuierlich wächst. Hohe Jim Beam-Absätze werden von gezielten Marketingkampagnen weltweit unterstützt, die sich vor allem an Erwachsene unter 30 Jahren richten. Äußerst vielfältiges weiteres Spirituosenspektrum Zwar hält die Markenfamilie Jim Beam mit einem Anteil von knapp 20 Prozent nach wie vor den Löwenanteil am Beam-Absatz. Jedoch gesellt sich mittlerweile ein äußerst breites weiteres Markenspektrum zu diesen Bourbon-Varianten. Darunter finden sich sogenannte „Power Brands“ wie Maker’s Mark Bourbon, Pinnacle Vodka, Sauza Tequila, Courvoisier Cognac, Canadian Club Whisky, Teacher’s Scotch. Als Aufsteiger im Sortiment gelten beispielsweise Skinnygirl Cocktails, Knob Creek Bourbon, Hilbeggan Irish Whiskey, Hornitos Tequila oder auch Cruzan Rum. Dazu kommen zahlreiche landestypische Spezialitäten wie DeKuyper Cordials (USA), Larios Gin (Spanien) oder auch Sourz Liqueur (Großbritannien). Größtes Spirituosenunternehmen in den USA und weltweit auf Rang 4 Mit allen diesen und vielen weiteren Marken hält Beam die Position des größten Spirituosenunternehmens in den USA und steht unter den internationalen Premium-Spirituosen-Anbietern auf Rang 4. Beam beschäftigt weltweit 3.400 Mitarbeiter. Der Gesamtabsatz des Unternehmens belief sich 2012 auf 38 Millionen Kartons, der Umsatz lag bei 2,5 Milliarden US-Dollar. Unterteilt ist die „Beam-Welt“ in drei Verkaufsregionen. Nach wie vor wird mit 58 Prozent der bedeutendste Anteil am Absatz in den USA getätigt. An zweiter Stelle stehen mit 22 Prozent die Region Europa/Mittlerer Osten/Afrika, dicht gefolgt von dem Bereich Asien Pazifik/Südamerika (verbleibende 20 Prozent). Größtes Beam-Werk in Frankfort, Kentucky, mit gleich vier neuen KHS-Wrap-Around-Packern Von den innerhalb der USA produzierten 21 Millionen Kartons an Beam-Produkten realisiert das Werk in Frankfort, Kentucky, 12 Millionen Stück. Abgefüllt und verpackt werden hier etwa 100 verschiedene Spirituosenmarken. Sie verlassen das Werk in ca. 1.600 unterschiedlichen Verkaufseinheiten. Beschäftigt sind in Frankfort um die 350 Mitarbeiter. Das Betriebsgelände fasst ca. 350.000 Quadratmeter, die Lagerkapazität beträgt etwa 21 Millionen Liter (175.000 Barrel). Die Produktionsstätte ist in den letzten Jahren besonders zügig gewachsen. So verdoppelte sich deren Ausstoßvolumen innerhalb von nur fünf Jahren. Das Werk produziert heute im Zwei-, teilweise auch im Dreischichtbetrieb mit insgesamt neun Linien. Vier davon sind mit jeweils einem Wrap-Around-Packer von KHS ausgestattet. Bei diesen Wrap-Around-Packern handelt es sich um zwei Innopack Kisters WP A-H aus der Baureihe Advanced für Hochleistungs-Linien (Leistung bis zu 70 Takte/Minute) und zwei Innopack Kisters WP 030, die innerhalb von Anlagen mit geringerer Leistung bis zu 30 Takte/Minute realisieren. Während die beiden Innopack Kisters WP A-H im Werk Frankfort unterschiedliche Glas- und PET-Flaschen in 6er und 12er Packs verpacken, sind die beiden kleineren Maschinen ausschließlich für die Verarbeitung jeweils einer PET-Flaschengröße in 12er Packs vorgesehen. Generell werden im „Old Grand Dad“-Werk in nahezu gleichem Umfang Spirituosen in PET- bzw. Glasflaschen abgefüllt. DuBois: „Die Popularität von Spirituosen in PET-Flaschen steigt weiter. Das liegt an den zahlreichen Vorteilen wie der Leichtigkeit und der Unzerbrechlichkeit, die mit PET einhergehen. Dazu kommt, dass unsere PET-Markenflaschen auf den ersten Blick kaum von Glasflaschen zu unterscheiden sind und sie sich folglich auch optisch hervorragend präsentieren.“ Erster positiver Eindruck blieb genau so erhalten Ob Verarbeitung von Glas- oder PET-Flaschen – laut John Ballard, Leiter Instandhaltung, war die Investition in jeden einzelnen der Innopack Kisters Wrap-Around-Packer eine hervorragende Entscheidung. Ballard: „Kaum in unserem Betrieb aufgebaut, produzierten sie alle bereits zu unserer vollsten Zufriedenheit. Unser erster positiver Eindruck hat sich auch über die Zeit hinweg so gehalten. Da liegt es förmlich auf der Hand, dass wir – wann immer eine Ersatzinvestition in Packmaschinen anstand – in jüngster Vergangenheit kontinuierlich auf KHS-Technik setzten.“ Die Entscheidung für den ersten Innopack Kisters WP A-H fiel im Jahr 2010. DuBois: „Damals betrachteten wir das System bei Brauereien, die es bereits seit längerem einsetzten. Sie zeigten sich sehr zufrieden, wir hörten ausschließlich Positives und konnten die technische Lösung vor Ort genauer ansehen. Dabei stellten wir fest, dass es sich hierbei um ein in jeder Hinsicht durchdachtes Gesamtkonzept handelt, das uns durch seine hohe Flexibilität für die Zukunft bestens rüstet. Schließlich zögerten wir nicht lange und platzierten unsere Order bei KHS.“ Wrap-Around-Packer der neuen Verpackungsmaschinen-Baureihe Advanced überzeugen im Hochleistungsbereich Verarbeiten die beiden Innopack Kisters WP A-H derzeit auch ausschließlich vorgegebene Flaschenvarianten in 6er und 12er Packs, muss das in Zukunft nicht so bleiben. Ob Glas-, Metall- oder Kunststoff-Behälter, Dosen oder Kartonverpackungen – die Verpackungsmaschinen sind für alle diese Produkte in verschiedensten Formen, Höhen und Breiten prädestiniert. Grundsätzlich eignen sie sich sowohl für den Einsatz in der Getränkebranche als auch in der Food- und Nonfood-Industrie. Ein weiterer Flexibilitätsvorteil, der für Advanced-Technik greifen kann: die Ergänzung der Maschine durch zusätzliche Module ist machbar. Ballard: „Auch wenn wir es nicht vorhaben unser Konzept zu verändern, es ist gut zu wissen, dass es möglich wäre. Denn wer kann heute schon ganz genau sagen, was die nächsten Jahrzehnte bringen.“ Hohe Bedienerfreundlichkeit Von besonderer Bedeutung für DuBois ist das Konzept der bedienergeführten Formatumstellung. Hier wird bei einem Produktwechsel bereits über das Bedienpult der Maschine mitgeteilt, welche Parameter wo neu einzustellen ist. Papierlisten zu Einstellparametern und eine Prüfung sämtlicher Bereiche, in denen Neueinstellungen notwendig sein könnten, entfallen. Wo und wie Neueinstellungen durchzuführen sind, kommuniziert eine elektronische Anzeige genauestens. Eventuelles Spiel in Zahnrädern und Ketten ist dabei bereits mit berücksichtigt. Außerdem wesentlich: die hervorragende Zugänglichkeit der Maschine sowie deren hygienisches Design. Identische Servomotoren mit integrierten Servoreglern bieten zahlreiche Vorteile Zugeführt werden den Packern die Wrap-Around-Verpackungen per Drängelprinzip und Verteilung in Gassen. Es folgt die Produktgruppierung mittels Multi-Servo-Abteileinheit. Von großem Vorteil ist, dass bei gemäß der Baureihe Advanced gestalteten Packern generell identische Servomotoren mit jeweils integrierten Servoreglern zum Einsatz gelangen. Die Verbindung von Servomotor und Servoregler in einer Einheit erleichtert die Fehlersuche im Fall einer Störung sowie den Austausch im Wartungsfall. Außerdem wird die Ersatzteilbevorratung reduziert. Dazu kommt: Da sich die Servoregler nicht mehr – wie bislang üblich – im Schaltschrank befinden, ist der Verkabelungsaufwand innerhalb der Verpackungsmaschinen minimiert und der Schaltschrank lässt sich kleiner auslegen. Ballard: Den Punkt „identische Servomotoren mit jeweils integrierten Servoreglern“ nahmen wir bereits im Vorfeld der Investition als sehr positiv wahr. In der Tat profitieren wir hierdurch unter anderem auch durch eine erhöhte Maschineneffizienz.“ Vorgeschaltete Zuschnitt-Transportbahn verringert Bedienerbindung In den Innopack Kisters WP A-H findet unterhalb der Gruppierstation die Vereinzelung von Wrap-Around-Zuschnitten statt. Der automatische Abzug einzelner Zuschnitte geschieht über ein Riemensystem. Für ein perfektes Eintakten der Zuschnitte in die Transportkette sorgen mittels Servomotor angetriebene Spezialriemen, die über eine besonders griffige Oberfläche verfügen. Die hohe Produktionssicherheit gewährleisten optoelektronische Sensoren innerhalb des gesamten Zuschnitt-Transports. Beam traf die Entscheidung, den Packern jeweils eine Zuschnitt-Transportbahn vorzuschalten. Ballard: „Die Bediener beladen den Transporteur und können sich dann so lange weiteren Aufgaben widmen bis die Zuschnitte abgearbeitet sind. Diese reduzierte Bedienerbindung sehen wir ebenfalls als einen wesentlichen Pluspunkt an.“ Besonders schonender und äußerst passgenauer Verpackungsvorgang Die Zuschnitte treffen nach einem Eintakten mit den innerhalb der Gruppierstation gebildeten Produktgruppen zeitgleich zusammen. Die Produkte sind zu jedem Verarbeitungszeitpunkt fixiert und sicher geführt. Dafür sorgen im vorderen und hinteren Kartonbereich Faltketten, an denen Faltmitnehmer befestigt sind, die über Kurven gesteuert werden. Gleichzeitig geschieht ein beiderseitiges seitliches Fixieren während der Zusammenführung von Zuschnitt und Produktgruppe über spezielle Faltkurven. Der Verpackungsvorgang im Detail: Sobald eine Produktgruppe in den Zuschnitt einläuft, regelt ein Faltmitnehmer, dass der vordere Bereich des Wrap-Around-Zuschnitts nach oben gefaltet wird. Währenddessen werden hintere Produkte der Formation durch einen Stab fixiert. Ein weiterer Faltmitnehmer übernimmt danach das Verschließen des hinteren Zuschnittbereiches. Es folgen der Leimauftrag durch spezielle Heißleimauftragsköpfe und der endgültige Verschluss von Vorder- und Hinterseite der Verpackung. Ein nächster Schritt betrifft die Faltung und Verklebung des Deckelbereiches. Anschließend durchfährt die fertig gebildete Kartonverpackung eine Andrückstrecke. Das schließt beste Produktionssicherheit und hohe Maschineneffizienz mit ein. Hohe Flexibilität Verarbeitet Beam derzeit auch ausschließlich Wellpappekartons, ist das System für Kraftkartons gleichermaßen vorbereitet. Ein weiterer Aspekt der für die künftige Flexibilität spricht. Zudem berät KHS auch in Hinblick auf besonders geeignete Kartonmaterialien. Die Beratungsleistung beginnt hier bei der Art und Stärke des Kartonmaterials für definierte Vorhaben und geht bis hin zur Kartonform, zu integrierenden Perforationen und denkbaren Gefachen. Ebenfalls ein Flexibilitätsplus: Jeder Innopack Kisters WP A-H ist bei Bedarf auch in der Lage, Tray-Verpackungen zu bilden. Einzige Einschränkung hier: Die Tray-Randhöhe muss mindestens 60 Millimeter betragen. Die jüngste Investition betrifft zwei Innopack WP 030 – und auch hier herrscht höchste Zufriedenheit Meint DuBois: „Die Verpackungsmaschinen-Baureihe Advanced überzeugt in unseren Hochleistungslinien in jeder Hinsicht. Das teilen wir allen interessierten Besuchern auch aus tiefer Überzeugung genau so mit.“ Ballard: „Äußerst zufrieden sind wir auch mit den beiden zuletzt georderten Innopack WP 030. Die Advanced-Technologie kommt hier ganz einfach aus dem Grund nicht zum Einsatz, weil wir die mit ihr verbundenen zahlreichen Vorteile bei der Einbringung von nur einer Flaschengröße in den 12er Wrap-Around-Karton nicht nutzen könnten.“ Ergänzt DuBois: „Auch die zwei Innopack WP 030 arbeiten ganz so, wie wir es uns wünschen. Die hervorragende Produktqualität ist hier genauso gegeben wie die Bedienerfreundlichkeit und das geräuscharme Arbeiten. Für Linien mit geringer Leistung und einem kleinen Verarbeitungsspektrum, würden wir uns immer wieder für diese Lösungen entscheiden.“ Die gesamte Beam-Gruppe profitiert Die positiven Erfahrungen mit KHS-Wrap-Around-Packern wurden vom Old Grand Dad-Werk übrigens innerhalb der Beam-Gruppe deutlich kommuniziert. DuBois: „Generell ist ein gegenseitiger Erfahrungsaustausch viel wert. Das kommt der Produktqualität und Anlageneffizienz in sämtlichen Beam-Werken weltweit sehr zugute.“