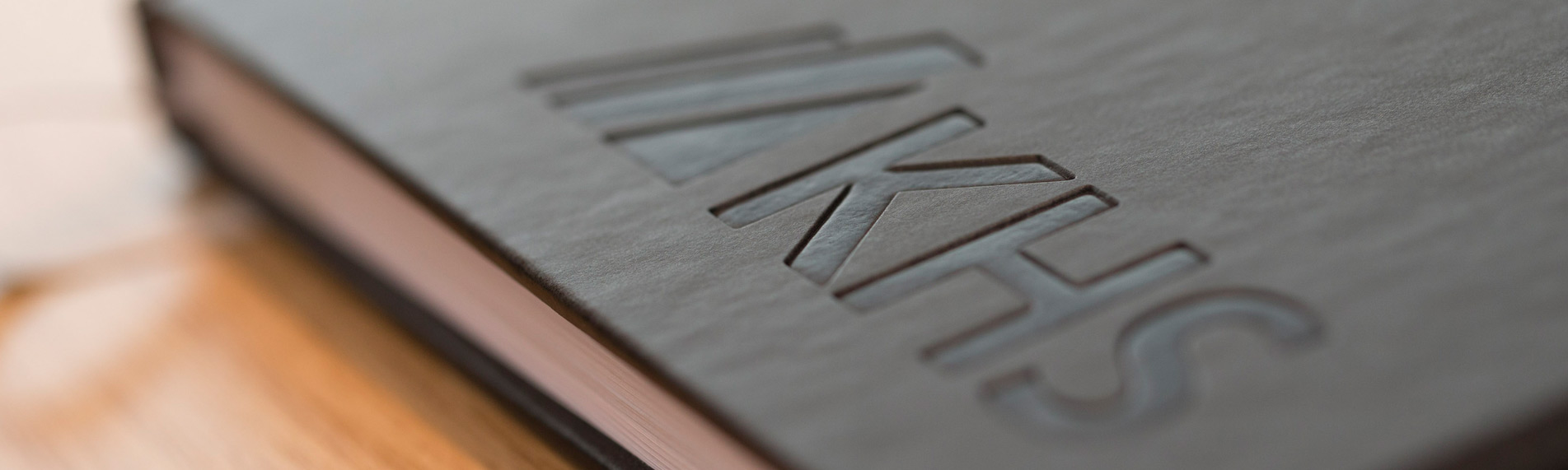
Qualität als oberstes Gebot
Australische Brauerei Coopers investiert in KHS-Turnkey-Linie und setzt deutliche Zeichen für weiteres Wachstum
Frank Hollmann* Kurt Hofmann** Es war das Jahr 1862, als der ehemalige Schuhmacher und Steinmetz Thomas Cooper sein erstes Bier herstellte. Grund: Seiner Frau Ann wurde aus gesundheitlichen Gründen empfohlen, Bier zu trinken, und das war in Australien damals schwer erhältlich. Der englische Schwiegervater sorgte für das Bierrezept, Thomas Cooper braute und das machte ihm so viel Spaß, dass er bis 1881 als Hausbrauer agierte und schließlich eine eigene Brauerei im Heimatort Adelaide aufbaute. Könnte er sehen, was aus ihr geworden ist, wäre er sicherlich sehr stolz. So steht die Brauerei Cooper unter den australischen Brauereien im Ranking heute auf Platz drei, befindet sich als einzige Großbrauerei im Land zu 100 % in australischem Besitz und wird nach wie vor von der Familie Cooper geführt. Über die Jahrhunderte hinweg blieb das Unternehmen seinem hohen Anspruch an Bierqualität treu. Dr. Tim Cooper, Managing Director Coopers in fünfter Generation: „Wir legen allergrößten Wert auf beste Zutaten, den handwerklichen Brauprozess und hervorragende technische Lösungen.“ Da verwundert es nicht weiter, dass Coopers bereits seit Jahrzehnten auf KHS-Technik setzt und erst kürzlich in eine KHS-Turnkey-Glas-Linie investierte, die laut Nick Sterenberg, Operations Manager Coopers, „qualitativ exakt das abbildet, was der Coopers-Unternehmensphilosophie entspricht.“ KHS-Technik seit den 1960er Jahren Erste Erfahrungen mit KHS-Fülltechnik sammelte Coopers bereits in den 1960er Jahren. Damals investierte die Brauerei in gleich zwei KHS-Füllsysteme, die mehr als 30 Jahre lang treue Dienste leisteten. Ersetzt wurden diese „Schätze“ 1996 durch einen mechanisch gesteuerten KHS-Hochleistungsfüller mit 100 Füllstellen. Nahezu parallel zu dieser Investition begann bei Coopers ein deutliches Absatzwachstum, das bis heute andauert. Lagen Bierverkäufe 1996 bei etwa 150.000 Hektoliter, waren sie fünf Jahre später bereits bei ca. 270.000 Hektoliter angelangt. In den letzten 20 Jahren ein durchschnittliches jährliches Absatzplus von knapp 10 % Um der permanent steigenden Nachfrage Rechnung zu tragen, bezog Coopers 2001 eine neu errichtete Braustätte mit Platz für umfassendes, weiteres * Leiter Market Zone Asia Pacific, KHS GmbH, Bad Kreuznach, Tel. +49 6 71/8 52-28 88 ** Leiter KHS Pacific PTY LTD, Tullamarine, Australien, Tel. +61/3 93 35-13 31 Wachstum. KHS organisierte den Umzug der kompletten Abfüllanlage, lieferte gleichzeitig einen Pasteur und ersetzte in die Jahre gekommene vorhandene technische Lösungen am neuen Standort sukzessive. Sterenberg: „Nach und nach tauschten wir unsere Maschinen durch neuere und schnellere KHS-Lösungen aus und erhöhten unsere Abfüll- und Verpackungskapazitäten damit kontinuierlich.“ So investierte Coopers 2005 in eine Innokeg Transomat Keg-Linie und in das rechnergesteuerte, pneumatische Druckfüllsystem Innofill DRS-ZMS, 2007 in eine Etikettiermaschine vom Typ Innoket SE, 2010 in einen mechanisch gesteuerten Innofill DMD-Dosenfüller und den Wrap-Around-Packer Innopack Kisters WP A-H. Die Verkaufszahlen wuchsen mit. Dr. Cooper: „Innerhalb der letzten 20 Jahre realisierten wir eine durchschnittliche Absatzsteigerung von 9,8 % pro Jahr. 2014 wurden Bierverkäufe von rund 750.000 Hektoliter erzielt . Für die nächsten 10 Jahre rechnen wir mit einem weiteren jährlichen Plus von etwa 7 %.“ Fünf Erfolgsfaktoren Interessant: Während Coopers wächst und wächst, sinkt der Pro-Kopf-Konsum an Bier in Australien kontinuierlich. In den 1970er Jahren noch bei ca. 140 Liter, war er Mitte der 1990er Jahre bei etwa 100 Liter angelangt und beträgt heute nur noch um die 75 Liter. Vor allem fünf Aspekte sind laut Dr. Cooper für das marktuntypische Wachstum der Brauerei mitverantwortlich: Zum Ersten die kompromisslose Qualitätsstrategie. Zum Zweiten die Tatsache, dass Lion Nathan, im australischen Biermarkt die Nummer eins, Anfang der 1990er Jahre seine Hotelbetriebe veräußerte, was Coopers die Möglichkeit bot, mit seinen Bieren hier einzusteigen. Zum Dritten erweiterte Coopers sein Distributionsgebiet vom südlichen Australien auf das ganze Land und baute Exportaktivitäten aus. Zum Vierten produziert Coopers Premium-Biere und genau diese Bierkategorie ist es, die in Australien ein besonders starkes Wachstum verzeichnet. Zum Fünften – und das ist für viele Australier ein ganz entscheidender Aspekt – punktet das Unternehmen als die einzige Großbrauerei Australiens, die sich ausschließlich im heimischen Besitz befindet. Ein Plus, das permanent kommuniziert wird und sich unter anderem auch auf allen Verpackungen wiederfindet. Dort steht deutlich geschrieben: „Australian made, Australian owned“. In ganz Australien und im Export wachsend Betrachtet man die regionale Verteilung des Bierabsatzes, entfallen 27 % auf Südaustralien, 26 % auf New South Wales, 17 % auf Victoria, 14 % auf Queensland, 11 % auf Westaustralien, 3 % auf das Northern Territory und 2 % gehen in Richtung Export. Exportland Nummer eins ist Neuseeland, gefolgt von Großbritannien und den USA. Dr. Cooper: „Mittelfristig kalkulieren wir mit einem Exportanteil von 5 %. Des Weiteren möchten wir die Präsenz unserer Biere in Australien außerhalb unseres südaustralischen Stammgebiets noch stärker ausbauen. Momentan bestreitet Coopers knapp 5 % am australischen Bierabsatz. Wir gehen davon aus, dass wir bis Anfang der 2020er Jahre bereits um die 7 % auf unser Konto verbuchen.“ Insgesamt 14 eigene Biere, dazu die Lizenzproduktion internationaler Premium-Biermarken Produziert werden in der Brauerei insgesamt 14 eigene Biere. Dazu kommen in Lizenz gebraute internationale Premium-Biermarken wie Carlsberg, Kronenbourg, Sapporo, Mythos, Holsten und Birell. Ungefähr 80 % der Gesamtbierproduktion gehen in der Einweg-Glasflasche an den Verbraucher, weitere 16 % im Keg und 4 % in der Dose. Wobei sowohl im Keg als auch in der Dose nicht das komplette Sortiment zur Verfügung steht. Meint Sterenberg: „Das bedeutet auch, dass unsere ehemals einzige Glas-Linie eine große Vielfalt an unterschiedlichen Produkten zu verarbeiten hatte und durch Umrüstungen viel an wertvoller Produktionszeit verloren ging. Daher trafen wir die klare Entscheidung, auf der neuen KHS-Hochleistungs-Glas-Linie ausschließlich die Bestseller abzufüllen und zu verpacken. Damit erreichen wir sowohl für diese, als auch für die bereits vorhandene Linie eine sehr gute Anlagenverfügbarkeit.“ Original Pale Ale – der Renner Zu den Sortimentsrennern zählen Coopers Original Pale Ale, Coopers Sparkling Ale, Coopers Mild Ale, Coopers Dark Ale und Best Extra Stout. Gemeinsam mit etwa 80 % des Produktionsvolumens. Bedeutendste Biermarke in der Reihe: Original Pale Ale mit einem 60-prozentigen Anteil. Es folgen Sparkling Ale (13 %), Mild Ale (4 %) und Best Extra Stout (3 %). In Anbetracht dieser Verteilung wird eines schnell klar: Australien ist „Ale-Land“. Erste Turnkey-Linie der Geschichte Bei der neuen Abfüll- und Verpackungsanlage handelt es sich um die erste Turnkey-Linie in der Geschichte der Brauerei. Dr. Cooper: „Wir sahen einen deutlichen Vorteil darin, von unserem Lieferanten des Vertrauens alles aus einer Hand zu erhalten.“ Ergänzt Sterenberg: „Wesentlich war für uns in diesem Zusammenhang auch, dass wir über Jahrzehnte hinweg sehr gute Erfahrungen mit unserem KHS-Equipment und dem KHS-Service sammeln konnten. Gerade „Down Under“ ist robuste, zuverlässige Technik und die Sicherstellung einer schnellen Serviceleistung das A und O. Von KHS sind wir genau das gewohnt und darauf möchten wir auch in Zukunft auf keinen Fall verzichten.“ Mit 3D die maßgeschneiderte Planung Die neue KHS-Turnkey-Linie ist für eine Leistung von bis zu 66.000 Flaschen/h ausgelegt und wurde in 3D geplant. In die Planung integrierte KHS als Turnkey-Anbieter nicht nur Abfüll- und Verpackungstechnik, sondern auch sämtliche Randgewerke. Die 3D-Ansicht erfolgte mit Hilfe einer Powerwall. Mit 3D-Brille und einem sogenannten „Fly Stick“ ausgestattet, navigierten sich die Betrachter direkt in die Anlage hinein. Sterenberg: „Dadurch konnten wir die Linie im Vorfeld besonders genau überprüfen und Änderungswünsche noch gezielter einarbeiten lassen.“ Alles auf einer Ebene Erste Station innerhalb der Anlage ist der Entpalettierer Innopal ASN, dem Neuglaspaletten auf einer Palettentransportbahn zur Verfügung gestellt werden. Die Entscheidung für diesen Abräumer fiel bei Coopers auch, weil er vollautomatisch mit Niveauausgleich arbeitet und so die gesamte Linie auf einer Ebene auszulegen war. Zudem bietet das vierseitig geschlossene Schiebesystem des Innopal ASN höchste Sicherheit beim Abräumvorgang. Produktschonend sind alle Flächen des Entpalettierers, die mit den Glasflaschen in Berührung kommen, mit Kunststoffplatten belegt. Dadurch entstehen keine Vibrationen und Kontakt-Impulsgeräusche. Mit in das Konzept eingeschlossen: ein vollautomatisch arbeitender Handling-Roboter. Er nimmt Stülpdeckel von jeder einzelnen Palette mit Vakuumgreifern ab und realisiert auch das Abheben und Verteilen von Zwischenlagen und Leerpaletten. Sterenberg: „Im Gegensatz zu den anderen in unsere neue Linie integrierten KHS-Maschinen hatten wir mit KHS-Ent- und Bepalettierern noch keine Erfahrungen gesammelt. Daher besuchten wir vor deren Order das KHS-Werk Worms, um uns ein Bild davon zu machen, ob auch diese Technik dem von uns gewünschten „KHS-Standard“ entspricht. Wir hatten einen sehr guten Eindruck von der dortigen Fertigung und die Performance unserer Palettierer ist seit Inbetriebnahme der Anlage hervorragend.“ Ergänzt Robin Howe, Engineering Manager Coopers: „Das schonende Ent- und Bepalettieren hat auch einen entscheidenden Einfluss auf den besonders geringen Glasverlust in der Linie. Während er in unserer vorhanden Anlage bei schon guten 0,45 % liegt, registrieren wir hier 0,2 %.“ Rins- und Fülltechnik aufgrund hoher Zufriedenheit beibehalten … Entpalettierte Glasflaschen werden dem Rinser-Füller-Block zugeführt. Dem Füllsystem vorgeschaltet ist der mechanisch gesteuerte Zweikanal-Rinser Innoclean FR-ZM. Das Rinssystem ist für eine Behandlung der Glasflaschen mit zwei Rinsmedien ausgelegt. Bei Coopers folgt auf den Rinsprozess mit UV-behandeltem Wasser die Spülung der Flaschen mit Kaltwasser. In der Flasche befindliche Verunreinigungen wie beispielsweise Staub oder auch Glaspartikel werden zuverlässig entfernt. Spezielle Rinsprogramme sind für sämtliche Produkte fixiert und im System hinterlegt. Bei Produkt- bzw. Flaschenwechsel geschieht die Umstellung des Rinsvorgangs wenn nötig am Bildschirm auf Knopfdruck. Bezogen auf das Füllsystem, orderte Coopers ganz gezielt den Innofill DRS-ZMS. Dr. Cooper: „KHS empfahl uns die innovative Füllervariante Innofill Glass DRS-ZMS. Wir entschieden uns dennoch für das Vorgängermodell. Ganz einfach, weil wir mit diesem Füllsystem in unserer vorhandenen Anlage derart zufrieden sind, dass wir uns genau die gleiche Lösung noch einmal wünschten. Ob Abfüllqualität oder robuste Gestaltung, an diesem Füller überzeugt einfach alles.“ Der Innofill DRS-ZMS arbeitet mit Füllhöhensonde. Das dreifache Vorevakuieren und die zweifache CO2-Spülung gehen dem Vorspannprozess voraus. Nach dem Vorspannen öffnet sich das Flüssigkeitsventil und leitet das Produkt über einen Drallkörper an die Flascheninnenwand. Durch die Schnellfüllphase im unkritischen zylindrischen Bereich der Flaschen werden hohe Ventilleistungen erreicht. Zur präzisen Füllhöhenmessung findet im engen Flaschenhals eine langsame Füllphase statt. Ein Sondenimpuls schließt das Flüssigkeitsventil. Vor- und Restentlastung folgen. Die druckgesteuerte Entlastung geschieht schaumarm. Der Füllprozess verläuft drehzahlunabhängig. Das elektronisch gesteuerte pneumatische Druckfüllsystem sorgt für eine besonders sauerstoffarme Abfüllung von Bier in Glasflaschen und den niedrigen CO2-Verbrauch. Ein mit dem Füller geblockter Kronkorken-Verschließer übernimmt den Verschlussvorgang. Über Puffertische geht es für die Flaschen im Anschluss daran in Richtung Etikettiermaschine. … das gilt auch für die Etikettiertechnik … Hierbei handelt es sich um die Innoket SE 2090, eine modulartig aufgebaute KHS-Etikettiermaschine, die mit einem Teilkreis von knapp 2,40 Meter die Ausstattung von bis zu 72.000 Flaschen/h vornimmt. Sterenberg: „Mit der identischen Hochleistungsetikettiermaschine sammelten wir in unserer bestehenden Linie nur gute Erfahrungen. Die hohe Maschineneffizienz stimmt hier genauso wie die Ausstattung. Zudem ist dieser Typ Etikettiermaschine höchst flexibel und damit besonders zukunftsfähig aufgestellt.“ Generell ist die Grundausstattung der Etikettiermaschinen-Generation Innoket SE gezielt einfach gehalten und besteht ausschließlich aus einer Tischkonstruktion und einem zentralen Etikettierkreisel. Dieser Etikettierkreisel lässt sich flexibel mit unterschiedlichsten Etikettierstationen bestücken. Nassleim-, Haft-, Heißleim-, Rollfed-Aggregate oder auch ein Kameramodul sind hier in beliebiger Kombination anzudocken. Momentan praktizieren die Coopers-Etikettiermaschinen in beiden Linien ausschließlich die Kaltleim-Etikettierung und sind hierfür mit jeweils drei Kaltleim-Stationen versehen, die Rumpf-, Brust- und Rückenetikettierung managen. Howe: „Sollte auf dem australischen Markt beispielsweise einmal die Haftetikettierung „in“ werden, lässt sie sich durch einen Austausch von Etikettierstationen am zentralen Etikettierkreisel realisieren. Machbar ist auch eine Kombination der Etikettierverfahren. All das ermöglicht uns die besonders zügige Reaktion auf wechselnde Verbrauchervorstellungen.“ Ebenso wie die vorhandene ist die neue Etikettiermaschine mit der elektronischen Drehteller-Steuerung VarioDrive versehen. Drehteller, Motor und Elektronik bilden eine Einheit. Die auf das jeweilige Flaschenformat und die Flaschenausstattung individuell abgestimmte Behälterdrehung findet statt. Sollte Coopers künftig neue Behälterformen und -ausstattungen planen, sind entsprechende Anpassungen zügig programmierbar. Wünscht die Brauerei in Zukunft die Integration von Relief- oder Formflaschen in ihr Flaschensortiment, sorgt VarioDrive in Kombination mit einem Kameramodul für die millimetergenaue Aufbringung von Etiketten an einer vorgegebenen Stelle. Dieses lässt sich ebenso wie die Etikettierstationen einfach und schnell an die Maschine andocken. Die Brauerei wünschte sich auch die gleichen Etikettenmagazine wie bei bestehender Etikettiertechnik. Jede Kaltleim-Etikettierstation wird daher von einem Magazin Innoket ALM (Automatic Label Magazine) beschickt, das bis zu 50.000 Etiketten fasst. Bediener müssen die Maschine folglich frühestens nach einer Arbeitszeit von 40 Minuten mit neuem Material versorgen. Howe: „Unsere beiden KHS-Etikettiermaschinen arbeiten bei hoher Leistung äußerst zuverlässig, sind bedienerfreundlich konzipiert und robust gestaltet. Wir sind von ihnen durchweg begeistert. Was die bewährten KHS-Kaltleim-Etikettierstationen betrifft, schätzen wir es sehr, dass für sie eine Überholung frühestens nach einer Laufzeit von 20.000 Stunden anfällt.“ Meint Sterenberg: „Zusammengefasst bilden hier Flexibilität, Qualität, Bedienerfreundlichkeit und die mit der Robustheit der Maschine verbundene lange Lebensdauer eine gelungene Symbiose.“ Ergänzt Dr. Cooper: „Von allerhöchster Bedeutung ist selbstverständlich, dass sich unsere Premium-Bierqualität in einer Premium-Ausstattung gelungen widerspiegelt.“ ... und den Wrap-Around-Packer Etikettierte Flaschen kommen in einem nächsten Schritt in Cluster Packs. Standardmäßig erfolgt die Bildung von 6er-Einheiten. Sie werden von einer Wrap-Around-Verpackungsmaschine Innopack Kisters WP A-H in der jeweils vier 6erPacks fassenden Wrap-Around-Packung zusammengefasst. Die Zuschnitte für die Wrap-Around-Packungen sind beim Innopack Kisters WP A-H innerhalb des Magazins horizontal angeordnet. Deren automatischer Abzug geschieht über ein Riemensystem. Stets werden Zuschnitte exakt in eine Mitnehmerkette getaktet, sodass sie mit den innerhalb der Gruppierstation gebildeten Produktgruppen zeitgleich zusammentreffen. Sobald eine Produktgruppe in den Zuschnitt einläuft, regelt ein Faltmitnehmer, dass der vordere Bereich des Wrap-Around-Zuschnitts nach oben gefaltet wird. Gleichzeitig sind hintere Produkte der Formation über einen Stab fixiert. Ist die Produktformation perfekt auf dem Zuschnitt positioniert, schließt ein weiterer Faltmitnehmer den hinteren Zuschnittbereich. Die über Kurven gesteuerten Faltmitnehmer erlauben ein flexibles Vorgehen. Unter anderem veranlassen sie, dass sich Vorder- und Hinterseite jedes Zuschnitts direkt nach Einspeisung der Produktformation nochmals geringfügig öffnen, um das korrekte Einfalten der Klebelaschen zu ermöglichen. Es folgt der Leimauftrag über spezielle Heißleimauftragsköpfe und ein endgültiges Schließen von Vorder- und Hinterseite der Verpackung im 90-Grad-Winkel. Nächster Schritt ist die Faltung und Klebung des Deckels. Der Karton ist geformt, verklebt und durchläuft nun die Andrückstrecke. Für die Zukunft von Coopers ebenfalls angedacht: die Verpackung von Einzelflaschen in die Wrap-Around-Packung. Sie ist bei Ergänzung der Linie um einen Transporteur, der Flaschen von der Etikettiermaschine direkt zum Innopack WP A-H fördert, machbar. Schonender Palettiervorgang bei vorgeschalteter Inline-Roboter-Gruppierung Für die Palettierung der Wrap-Around-Packungen ist der Säulenroboter Innopal RS 3 zuständig. Ihm ist eine Inline-Roboter-Gruppierung, bei der ein Vierachs-Roboter Innopack RK 4 die exakte Lagenvorbereitung übernimmt, vorgeschaltet. Die exakte Positionierung der Gebinde findet durch eine Schiebebewegung statt, die ganz an die Geschwindigkeit der Kunststoff-Mattenketten angepasst ist. Verpackungen fahren daraufhin gegen einen Anschlag. Es folgt die Zentrierung der gebildeten Formation. Der Innopal RS 3 übernimmt die jeweils gebildete Lage und übergibt sie mittels Rollenkäfigkopf auf eine Palette. Eine vierseitige Zentrierung der jeweils letzten aufgebrachten Lage sorgt beim Abziehen des Rollenteppichs für das sichere und gleichzeitig schonende Palettieren. Mit in das Konzept integriert ist ein Zwischenlageneinleger. Gebildete Paletten erfahren die Ladungssicherung durch einen Wickler und werden schließlich von einem Gabelstapler in das Vollgutlager transportiert. Von KHS-Turnkey-Technik in jeder Hinsicht überzeugt und für die Zukunft perfekt gerüstet Dr. Cooper: „Mit unserer neuen KHS-Turnkey-Linie sind wir für die Zukunft perfekt gerüstet. Sie lässt weitere Absatzsteigerungen für unsere Premium-Biere zu und arbeitete schon nach kurzer Zeit – wie von KHS-Technik nicht anders erwartet – mit hoher Linieneffizienz. Wir sind sehr zufrieden.“ Noch vor Beginn des neuen Jahrzehnts plant Coopers nun die Überschreitung der eine-Million-Hektoliter-Absatzschwelle. Gleichzeitig rechnet das Unternehmen mit einer Ausweitung der Geschäftstätigkeit innerhalb der zwei weiteren – bereits traditionell betriebenen – Geschäftsfelder: „Home Brew Kits“ und Malzextrakt. Dr. Cooper: „Diese Bereiche bilden eine hervorragende Ergänzung zu unseren Brauaktivitäten. Mit ihnen bestreiten wir derzeit etwa 20 % unseres Gesamtumsatzes von 240 Millionen australischen Dollar (ca. 165 Millionen Euro).“ Aktiv im Markt ist Coopers mit „Home Brew Kits“ und Malzextrakt schon seit mehreren Jahrzehnten. Mittlerweile gilt das Unternehmen als der bedeutendste Anbieter von „Home Brew Kits“ weltweit und der größte australische Exporteur von Malzextrakt. Auch künftig zählt nur eins: Qualität, Qualität und nochmals Qualität Dr. Cooper: „Wir sind stolz auf unser Wachstum auf allen Ebenen, das wir unserer Meinung nach nur deshalb erreicht haben, weil bei Coopers vor allem eines im Mittelpunkt steht: Qualität, Qualität und nochmals Qualität.“ Die strikte Qualitätsphilosophie soll auch in Zukunft in jeder Hinsicht erhalten bleiben und ist durch die Coopers-Vision bereits vorformuliert. Sie lautet: Coopers wird anlässlich seines 200-jährigen Jubiläums feiern, dass hier immer nur beste Biere und Brauereiprodukte hergestellt und vermarktet wurden. Dem ist nichts hinzuzufügen.