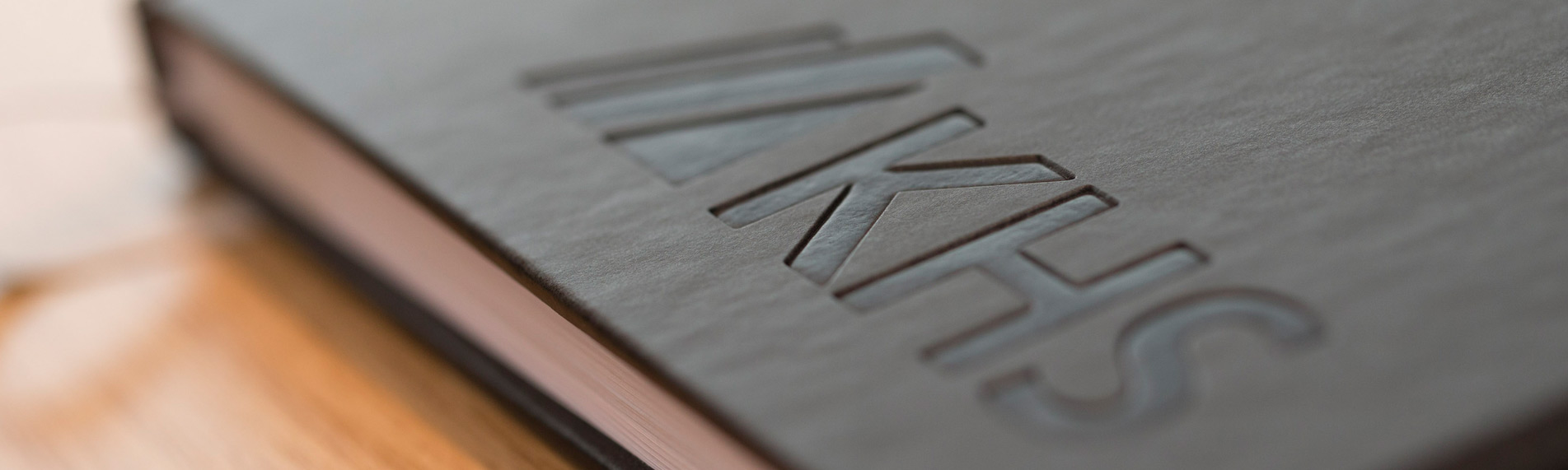
„Yes we can“
Höchste Anlageneffizienz trifft maximale Flexibilität
Coca-Cola Enterprises investiert am niederländischen Produktionsstandort Dongen in KHS-Turnkey-Dosenlinie
Hennie van der Graaf*
Herman Miseur**
„Yes we can“ – mit dieser Codierung versehen kamen die ersten bei Coca-Cola Enterprises (CCE) am Standort Dongen, Niederlande, abgefüllten Dosen beim Verbraucher an. Das zeigt Stolz. Stolz darauf, dass in Dongen erstmals eine Dosenabfüllung zum Tragen kommt. Und Stolz auf eine bis ins letzte Detail ausgeklügelte Abfüll-Linie, die eine perfekte Dosenabfüllung erst ermöglicht. Als Turnkey-Lieferant der neuen Linie agierte KHS. Kris Moortgat, Plant Director, CCE Dongen: „Mit KHS praktizierten wir bereits während der Anlagenplanung eine Teamarbeit wie sie besser nicht sein konnte. KHS setzte unsere Wünsche in jeder Hinsicht perfekt um und lieferte außerdem jede Menge an zusätzlichem Know-how. Die Aussage „Yes we can“ ist im Grunde genommen auch auf die gelungene Umsetzung von Ideen in ein technisches Komplettpaket anwendbar.“ In diesem Zusammenhang betont Moortgat explizit die hohe Effizienz, mit der die neue KHS-Dosenlinie in Dongen heute produziert. Sie liegt bei weit über 90 Prozent. Eine hohe Effizienz, die sich schon während der Abnahmephase erahnen ließ. Vorgabe von CCE Dongen: Ein Erreichen von mehr als 90 Prozent an Anlageneffizienz im Mittelwert. Real lagen Werte schließlich bei 98,2 Prozent. „Yes KHS can“ meint dazu Moortgat mit einem Augenzwinkern.
CCE – weltgrößter Produzent und Vermarkter von Coca-Cola-Produkten
Als Teil von Coca-Cola Enterprises (CCE) gehört der Standort Dongen dem weltgrößten Produzenten und Vermarkter von Coca-Cola-Produkten an. So operiert CCE in 46 US-Staaten ebenso wie in Kanada und ist als Coca-Cola Bottler gleichzeitig exklusiv für Belgien, Frankreich, Großbritannien. Luxemburg, Monaco und die Niederlande tätig. Jährlich setzt CCE etwa 42 Milliarden mit unterschiedlichen Coca-Cola-Produkten befüllte Dosen und Glas- sowie PET-Flaschen ab. Insgesamt gesehen repräsentieren CCE-Verkäufe ca. 16 Prozent des Gesamtabsatzes der Coca-Cola Company weltweit.
* Leiter der KHS Benelux B. V., Niederlande, Tel.: +31/76/5 72 32 30
** Verkauf KHS Benelux B. V., Niederlande, Tel.: +31/76/5 72 32 30
Jährliche Produktionsleistung in Dongen: 450 Millionen Liter
Im niederländischen Markt ist CCE seit dem Jahr 1993 aktiv. In diesem Jahr erwarb das Unternehmen den Produktionsstandort Dongen, der seither eine enorme Erweiterung und den stetigen Ausbau erfuhr. Dongen ist heute nicht nur der einzige Produktionsstandort von CCE in den Niederlanden, sondern auch der größte innerhalb der Benelux-Staaten und der zweitgrößte CCE-Produktionsbetrieb im gesamten europäischen Markt. Allein im Jahr 2009 wurden hier 450 Millionen Liter an Coca-Cola-Produkten hergestellt und in unterschiedliche Gebinde abgefüllt. Renner unter den Coca-Cola-Marken: Coca-Cola, Coca-Cola light, Coca-Cola zero und Fanta. An Gebinden stehen neben PET-Flaschen (55 Prozent) nun Dosen mit einem Anteil von 25 Prozent im Vordergrund. Jeweils weitere 10 Prozent betreffen Glasflaschen sowie den Bereich Postmix.
Insgesamt gesehen stammen derzeit 80 Prozent aller im niederländischen Markt konsumierten Coca-Cola-Produkte aus dem Werk Dongen. Die restlichen 20 Prozent werden importiert. Beispielsweise handelt es sich bei Importen um Coca-Cola Markenprodukte wie Acquarius, Burn, Minute maid. Moortgat: „Auch von Dongen aus unterstützen wir im Gegenzug unsere Nachbarländer Belgien und Frankreich wenn nötig mit Coca-Cola-Marken aus unserem Werk. Ein partnerschaftlicher Austausch, der sich in jeder Hinsicht bewährt.“
Wie populär Coca-Cola Marken in den Niederlanden sind, demonstrieren Zahlen eindrucksvoll. Der jährliche Pro-Kopf-Konsum an alkoholfreien Erfrischungsgetränken liegt bei um die 65 Liter. Allein 30 Liter davon entfallen in etwa auf den Konsum von Coca-Cola Markenprodukten. Was mit in sich trägt, dass nahezu jeder zweite in den Niederlanden konsumierte Liter Erfrischungsgetränk aus Dongen stammt.
Deutliches Absatzwachstum geplant
Trotz der hohen Präsenz im Markt wächst und wächst der niederländische Bedarf an Coca-Cola-Markenprodukten weiter. Moortgat: „In 2009 verzeichneten wir ein deutliches Plus. Für 2010 erwarten wir noch mehr an Wachstum.“ Wachstum, das auch ein geplantes Mehr in Hinblick auf den Absatz von Coca-Cola-Markenprodukten in der Dose beinhaltet. Und – hier schließt sich der Kreis – das eine effektiv arbeitende und flexibel zu handhabende Dosenlinie geradezu bedingt.
Neue KHS-Turnkey-Dosenlinie unterstützt Wachstumsprognosen
Derzeit realisiert die neue KHS-Turnkey-Dosenlinie ganz gemäß CCE-Vorgaben eine Leistung von 90.000 0,33-l-Dosen/h. Künftig ist – orientiert an geplantem Wachstum – eine Anlagenleistung von bis zu 120.000 0,33-l-Dosen/h machbar. Vom Abräumer bis zum Füllsystem sind Maschinen bereits darauf hin ausgelegt. Ein zusätzlicher Trockenteil erbringt in Kürze die Kapazitätserweiterung im Bereich Verpackung und Bepalettierung. Bis Mitte des Jahres ist diese zweite geplante Investitionsphase abgeschlossen und die Produktion von 120.000 0,33-l-Dosen/h innerhalb der gesamten Linie möglich.
Verarbeitung von unterschiedlichsten Dosenvarianten ist machbar
Wobei es für die höchst flexibel gestaltete Anlagentechnik keinesfalls bei einer ausschließlichen Verarbeitung von klassischen 0,33-l-Dosen bleiben muss. Denkbar ist hier ganz genauso die Abfüllung und Verpackung von klassischen 0,5-l-Dosen sowie von 0,33-l-, 0,25-l- und 0,15-l-Slim-Dosen. Maurice Malchair, Senior Engineering Manager, CCE Dongen: „Mit unserer neuen KHS-Linie sind wir für momentane und zukünftige Verbraucherwünsche hervorragend gerüstet.“
Maximaler Funktionalität konsequent Rechnung getragen
Neben höchster Flexibilität wird dem Aspekt der maximalen Funktionalität innerhalb der KHS-Linie permanent Rechnung getragen. Das beginnt bereits vor der Dosen-Entpalettierung. Ein Gabelstapler gibt jeweils zwei Leerdosenpaletten auf parallel zueinander verlaufende Transportbänder ab. Insgesamt gesehen ist bei voller Belegung der Transportstrecke mit Leerdosenpaletten eine Produktionszeit von etwa 45 Minuten gewährleistet. Bedienerfreundlich geregelt: ein automatisches Entfernen der Kunststoff-Bandsicherung von den Leerdosenpaletten. Eine vollautomatische Zuführung der Leerdosenpaletten zum Dosenabräumer Innopal ASH ist gegeben.
Schonende Entpalettierung
Innerhalb des Innopal ASH werden die Paletten in einem dreiseitig geschlossenen Schacht auf die jeweilige Abschiebeposition angehoben. Ein vierseitig geschlossenes Schiebesystem regelt während des Abräumvorgangs die Zentrierung jeder einzelnen Lage und bietet die Voraussetzung für die schonende Behandlung des empfindlichen Dosenmaterials. Die Zentrierleisten des Schieberahmens sind motorisch verstellbar. In Verbindung mit der eingesetzten pneumatischen Schachtwandverstellung lässt sich die Maschine auf Knopfdruck auf ein neues Format umstellen. Lediglich die Greifer für den Stahlrahmen sind mit wenigen Handgriffen manuell einzustellen. Produktschonend sind alle Flächen des Entpalettierers, die mit den Dosen in Berührung kommen, mit Kunststoffplatten belegt. Die Maschine ist mit zwei Abhebern ausgestattet. Einer davon greift den Stahldeckrahmen, fährt diesen in eine Parkposition und legt ihn, nachdem die Palette abgeräumt wurde, wieder auf der Palette ab. Die Ablageposition des Rahmens wird mittels Lichtschranke überwacht. Ein automatischer Zwischenlagenabheber befördert Zwischenlagen in ein speziell hierfür vorgesehenes weiteres Magazin. Die Entsorgung der Magazine geschieht bei vorgegebener Belegung auf automatischem Wege und damit ebenfalls äußerst bedienerfreundlich.
Großzügig ausgelegte Transportstrecken sichern Fluss in der Anlage
Nachdem der Innopal ASH die Dosen in die Anlage eingebracht hat, erfahren fehlerhafte Dosen über eine Vakuumbrücke die Aussonderung. Besonderheit hier: Die Vakuumbrücke ist S-kurvenförmig gestaltet, damit sich der weitere Dosentransport aus Layout-Gründen in einer vom Bisherigen abweichenden Transporthöhe fortführen lässt. Mittels Lufttransporteur gelangen „Gut-Dosen“ in Richtung schräg liegendes Rinssystem und werden kurz vor Einlauf in den Rinser überführt, der unter Verwendung von Wasser und Luft spült. Stets wird der Füllgrad der Transporteure über Lichtschranken abgefragt. Ist eine maximale Befüllung der Transportbänder erreicht, stoppt der Leerdosenabräumer automatisch. Marc Adriaansen, Engineering & Maintenance Manager, CCE Dongen: „Wie vor dem Rinssystem sorgen in der gesamten Linie großzügig ausgelegte Transportstrecken für den permanent aufrecht erhaltenen Dosenfluss.“
Herzstück Innofill DVD
Während des Rinsprozesses auf Füllerhöhe heruntergefahrene Dosen gelangen in das Herzstück der Linie, den elektronisch gesteuerten Volumenfüller Innofill DVD, der über 184 Füllstellen verfügt. Höchste Füllgenauigkeit ist hier durch das Prinzip der magnetisch induktiven Durchflussmessung realisiert. Toleranzen von Dosen unterschiedlicher Hersteller spielen folglich keine Rolle mehr. Ist eine Abfüll-Menge von beispielsweise 0,33 Litern im System programmiert, befinden sich auch exakt 0,33 Liter in der Dose. Einfach gestaltet sich beim Innofill DVD bei einem Wechsel von Dosengrößen die Umstellmöglichkeit am Bedienterminal „auf Knopfdruck“. Der Bediener ruft dabei die innerhalb des Systems bereits vorprogrammierten Werte ab und produziert mit der neuen Dosengröße ganz einfach weiter. Die Folge: Zeitersparnis und erhöhte Maschinenverfügbarkeit. Ausschließlich im Falle eines veränderten Dosendurchmessers steht der übliche Formatteilwechsel an.
Vom Ringkessel bis zum Füllventil finden sich beim Innofill DVD überall glatte Produktwege. Aseptische Membran- und Dichtungstechnik ist innerhalb der Füllventile des Innofill DVD ebenso selbstverständlich wie bei sämtlichen weiteren Produkt führenden Kanälen und Wegen.
Gerüstet ist der Innofill DVD neben der Abfüllung von kohlensäurehaltigen Getränken auch für die Abfüllung stiller Getränke. Derzeit ist in Dongen ausschließlich eine Abfüllung von kohlensäurehaltigen Coca-Cola-Markenprodukten gefordert. Hier geschieht nach einem Abdichten der Dose zunächst die Verdrängung von in der Dose vorhandener Luft durch einen Spülvorgang mit CO2. In einem nächsten Schritt wird der Rückgasweg geschlossen, der Gasweg bleibt offen. Die Dose erfährt die Vorspannung auf einen Fülldruck, der sich am CO2-Gehalt des Produktes orientiert. Ist der gewünschte Druck erreicht, öffnet das Flüssigkeitsventil. Produkt wird blasenarm abgestrahlt und fließt an der Dosenwand entlang bei gleich bleibender Füllgeschwindigkeit schonend in die Dose ein. Gas, das in der Dose enthalten ist, entweicht in den Vorspannkanal. Registriert der magnetisch induktive Durchflussmesser die Sollfüllmenge, schließt das Füllventil automatisch. Der Füllvorgang ist beendet. Es folgt eine schaumarme Entlastung, die für besonders schaumempfindliche Getränke auch zweistufig stattfinden kann.
Kompletteinhausung des Füller-Verschließer-Bereiches trägt höchsten hygienischen Maßstäben Rechnung
In Dongen ebenso Standard wie in allen weltweit angesiedelten CCE-Werken: Ein Anlegen höchster hygienischer Maßstäbe in sensiblen Bereichen. So verfügt der Füller-Verschließer-Block über eine Kompletteinhausung. Ein Teil der Decke der Einhausung ist mit Filtereinheiten ausgestattet. Diese Filtereinheiten filtrieren und reinigen die Hallenluft. Permanent besteht innerhalb der Einhausung bei leichtem Überdruck eine Luftströmung von der Decke zum Boden. So wird der Bereich der offen transportierten Dosen stets mit frisch filtrierter Luft versorgt. Spalten in der Verkleidung sowie eine Öffnung der Verkleidung im Bodenbereich sorgen dafür, dass filtrierte Luft in die Abfüllhalle entweichen kann.
Permanente Überprüfung
Zwischen Füll- und Verschließsystem integriert: eine Ausschleusung für nicht ordnungsgemäß befüllte Dosen. Im Anschluss an den Füll- und Verschließvorgang jederzeit machbar: Die Ausleitung von kompletten Füllerrunden auf einen separaten Transportstrang. In Dongen ist eine solche Ausleitung in etwa stündlich geplant – um maximale mikrobiologische Sicherheit zu gewährleisten. Jede einzelne Dose lässt sich bei deren Überprüfung dem jeweiligen Füllventil bzw. Verschließerkopf exakt zuordnen. Eventuell notwendige Maßnahmen können unverzüglich und vor allem treffsicher eingeleitet werden.
Prozesstechnische Einheit Füller mit Dosier- und Mischanlage
Dem Füllsystem Innofill DVD direkt vorgeschaltet: das jüngst von KHS in den Markt gebrachte, mit einem umfassenden Vorteilspaket versehene Dosier- und Ausmischsystem Innopro Paramix C. Sowohl Entgasungs- als auch Fertiggetränketank sind bei der Drei-Komponenten-Dosier- und Mischanlage Innopro Paramix C liegend angeordnet. Das schließt neben dem geringen Platzbedarf umfassende technologische Vorteile mit ein. Als ein erster Schritt findet innerhalb der Innopro Paramix C die Wasserentgasung nach dem Prinzip der zweistufigen Vakuum-Sprühentgasung statt. Hier ist durch den liegenden Entgasungstank und die Art der Versprühung im Vergleich zu einem stehend aufgebauten Entgasungstank eine größere Oberfläche der Flüssigkeitspartikel gegeben. Das unterstützt den erfolgreichen Entgasungsvorgang. Der Restsauerstoff des Wassers beträgt bei der Innopro Paramix C weniger als 0,3 Milligramm/Liter. Noch vor der Mischpumpe geschieht im Sirupstrang der Innopro Paramix C die präzise Massedurchflussmessung. Das führt selbst bei verdünnten Sirupphasen zu deren automatischer und detailgenauer Erkennung. Folge: Das Mischungsverhältnis von Wasser und Sirup lässt sich stets den Vorgaben entsprechend anpassen. Verdünnte Sirupphasen müssen nicht länger verworfen werden. Damit direkt verbunden: Noch zügiger vonstatten gehende Produktwechsel. Alles in allem tragen genannte Aspekte eine gesteigerte Anlageneffizienz sowie die gezielte Kostenreduzierung mit in sich. Während der Karbonisierung sorgt eine spezielle KHS-Karbonisierdüse für die optimale Verteilung und Bindung der Kohlensäure im Getränk. Einen bedeutenden Vorteil trägt auch hier der liegend gelagerte Fertiggetränkebehälter in sich: Eine analoge Füllstandsmessung im Puffertank in Verbindung mit einer rezepturgesteuerten, vollautomatischen Leistungsregelung der Innopro Paramix C zwischen 30 – 100 % garantieren konstante Produktionsbedingungen bei gleichzeitiger Eliminierung von zusätzlichem CO2-Verbrauch. Dieser Pluspunkt in Verbindung mit dem bis ins letzte Detail durchdachten Entgasungs- und Karbonisiervorgang, der ebenfalls zur Minimierung des Mikroblasenanteils im Produkt beiträgt, führt schließlich auch zu einer konkreten Leistungssteigerung am Füllsystem. Generell sind Innofill DVD und Innopro Paramix C als eine prozesstechnische Einheit definiert. So richtet sich die Innopro Paramix C bei der Produktherstellung direkt an der Leistung des Füllsystems aus.
Bevor befüllte Dosen zu den Verpackungsmaschinen gelangen, geschehen Füllhöhen- und Verschlusskontrolle, Drehung per automatisch angetriebenem Wender, Codierung, eine nochmalige Drehung der Dosen in die Ursprungsposition sowie eine zweite Füllhöhen- und Verschlusskontrolle.
Verpackungstechnik gemäß Advanced Baureihe mit umfassendem Vorteilspaket …
Zur Verpackung der Dosen stehen zwei Verpackungsmaschinen bereit. Zum einen der ShrinkPacker Innopack Kisters SP Advanced, zum anderen der TrayShrinkPacker Innopack Kisters TSP Advanced. Denkbar ist ein ausschließliches Bilden von Shrinkpacks und ein daran anschließendes Führen der Shrinkpacks in Richtung Belader oder ein Bilden von Shrinkpacks mit einer daran anschließenden Führung der Shrinkpacks zum Innopack Kisters TSP Advanced. Der Innopack Kisters SP Advanced realisiert bis zu 120 Takte/Minute. Gebildet werden hier Vierpacks, Sechspacks, Achtpacks und Zwölfpacks. Ein Leaflet-Inserter ist in das System mit integriert.
Bereitgestellte Shrinkpacks setzt der mit bis zu 100 Takten/Minute arbeitende Innopack Kisters TSP Advanced in 24er Trayverpackungen, die in Folie eingeschlagen und geschrumpft werden. Ebenfalls möglich: die direkte Zuführung einzelner Dosen zum TrayShrinkPacker. In diesem Fall werden Dosen in 24er Trays verpackt, bei Bedarf eingeschrumpft und dann zum Bepalettierer geführt. Besonderheit beim Innopack Kisters TSP Advanced: Hier sorgt ein verlängertes Zuschnittmagazin für die minimierte Bedienerbindung.
Dass sowohl ShrinkPacker als auch TrayShrinkPacker zur neuen KHS-Verpackungsmaschinen-Baureihe Advanced zählen, schließt höchste Flexibilität der Verpackungslösungen ebenso ein wie maximale Zukunftssicherheit. So wurde innerhalb der neuen Advanced Baureihe beispielsweise die Modulbauweise konsequent weiterentwickelt. Für jeden Aufgabenbereich gelangen austauschbar konzipierte Funktionsmodule zum Einsatz. Was auch bedeutet, dass jedes Funktionsmodul eine für sich abgeschlossene Einheit bildet und sich einfach aus dem Gesamtsystem herausnehmen oder in das Gesamtsystem integrieren lässt. Aus dem ShrinkPacker kann so bei Bedarf zum Beispiel mühelos ein PadShrinkPacker oder TrayShrinkPacker entstehen. Auch die Anpassung an neue Verarbeitungsbedingungen ist einfach zu realisieren. Ob Dosenverarbeitung, Kunststoff- oder Glasflaschenverarbeitung, ob verschiedenste Formen oder Höhen von zu verpackenden Gebinden – der Fantasie sind hier keine Grenzen gesetzt.
Adriaansen: „Die hohe Flexibilität unserer neuen Verpackungstechnik überzeugt uns ebenso wie die dort gegebene einfache bedienergeführte Formatumstellung und hygienisches Design vom Feinsten.“
Plus bei der bedienergeführten Formatumstellung: Dem Bediener wird über das Bedienpult der Maschine mitgeteilt, wo genau Neueinstellungen bei einem Produktwechsel vorzunehmen sind und wie genau an den Bedienstellen im Einzelnen zu verstellen ist. In der Tat trägt Advanced-Verpackungstechnik auch höchsten hygienischen Maßstäben Rechnung. Trägersysteme der Funktionsmodule bestehen aus lackierten, fest mit der Maschine verschweißten Rohren. Der Ablauf von Reinigungsmittel, Spülwasser und eventuell auslaufendem Produkt ist durch neu konzipierte unterhalb der Funktionsmodule angesiedelte Auffangwannen optimiert.
Malchair: „Weitere Vorteile von ShrinkPacker und TrayShrinkPacker gemäß Advanced Baureihe liegen beispielsweise in einer Ausstattung der Maschinen mit durchweg identischen Servomotoren mit jeweils integrierten Servoreglern. Generell sind wir mit dem „Gesamtpaket Advanced“ sehr zufrieden.“
… mal zwei
So zufrieden, dass ein weiterer ShrinkPacker und ein weiterer TrayShrinkPacker der Advanced Baureihe bereits geordert sind. Beide Maschinen werden künftig für die gezielte Leistungssteigerung der gesamten Linie auf 120.000 Dosen/h sorgen und ebenso wie bereits vorhandene Verpackungstechnik im Anschluss an Codierung und Dosenwender mit in die Anlage integriert.
Moortgat: „Neben der anvisierten Leistungssteigerung lässt die erneute Investition in KHS-Verpackungstechnik und in einen weiteren Belader noch mehr Flexibilität zu. So können wir zeitlich parallel voneinander differierende Verpackungsvarianten herstellen.“
Fazit: „Yes we can“
Ein Aspekt, der CCE in den Niederlanden sehr entgegen kommt, sind hier doch eine Vielzahl an voneinander differierenden Verpackungsvarianten gefragt. Insgesamt gesehen produziert Dongen allein für den niederländischen Markt um die 250 verschiedene Verpackungseinheiten. Was einmal mehr demonstriert, wie wesentlich der Faktor Flexibilität im Bereich der Anlagentechnik ist. Eine Flexibilität, die laut Moorgat künftig zu Absatzsteigerungen von CCE in den Niederlanden mit beitragen wird. Moorgat: „Wir bleiben der Erfrischungsgetränkeanbieter Nummer Eins in den Niederlanden. Auch weil Flexibilität und Effizienz mit Verlässlichkeit und Verantwortlichkeit in unserem Werk in Dongen Hand in Hand gehen. Unser Fazit in drei Worten heißt ganz einfach: Yes we can!“