InnoPET BloFill ACF-L aseptic block
Stretch blow molder/filler block for flexible processing of high- and low-acid products
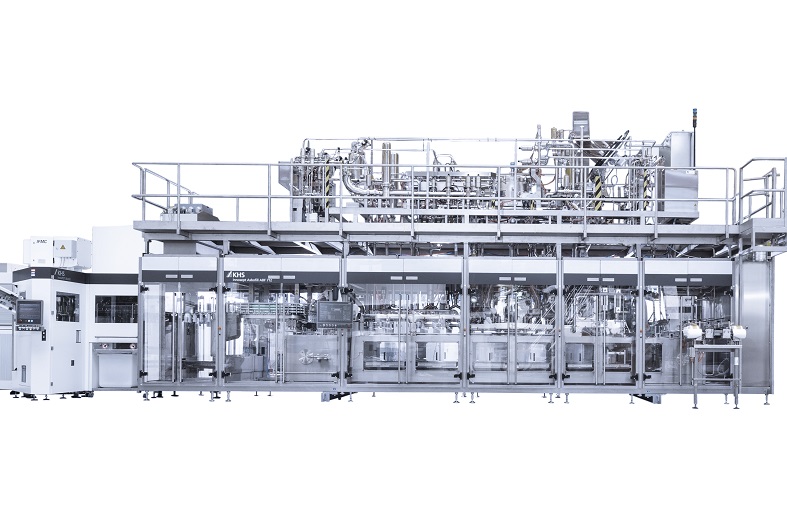
Good to know
A healthy lifestyle and increasing mobility in society are resulting in a steadily growing demand for sensitive and functional beverages in many different plastic bottles. The blocked aseptic InnoPET BloFill ACF-L filler and capper suitably caters for this trend for greater product variety by managing smaller batches: with its enormous flexibility it is perfect for frequent product changeovers. The InnoPET BloFill ACF-L fills milk, mixed milk, sports, yogurt and coffee beverages and fruit and vegetable juices in outstanding quality into PET bottles. The filling machine yields excellent results for capacities of up to 14,000 bottles per hour holding between 100 and 2,000 milliliters.
Well thought out
A new transfer module enables the linear aseptic filler to be blocked with a standard rotary KHS stretch blow molder. This readily combines two systems that have proved themselves on the market for many years. The new, unique Double Gate heating concept (DoGa) on the blow molder allows up to 40% in energy costs to be saved while taking up a minimum amount of space compared to single-lane stretch blow molders of the same capacity. At the same time, the filler provides maximum aseptic safety thanks to its extremely small aseptic zone. Depending on market requirements, the machine can be equipped with a closure system for plastic screw caps and/or foil seals.
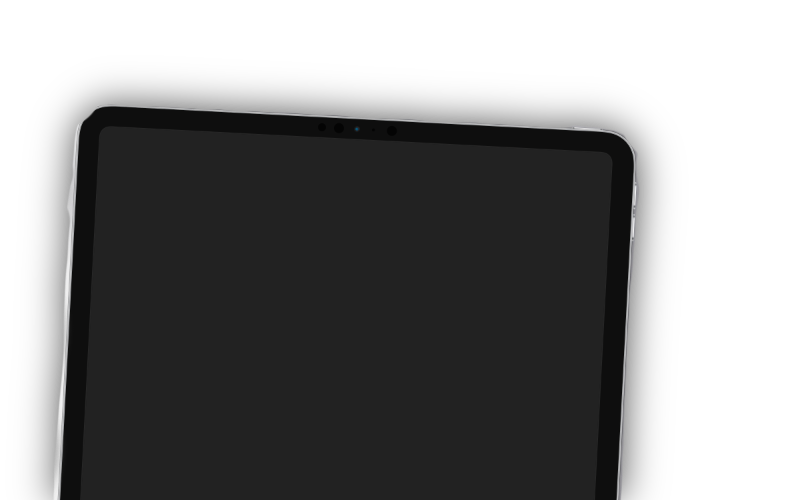
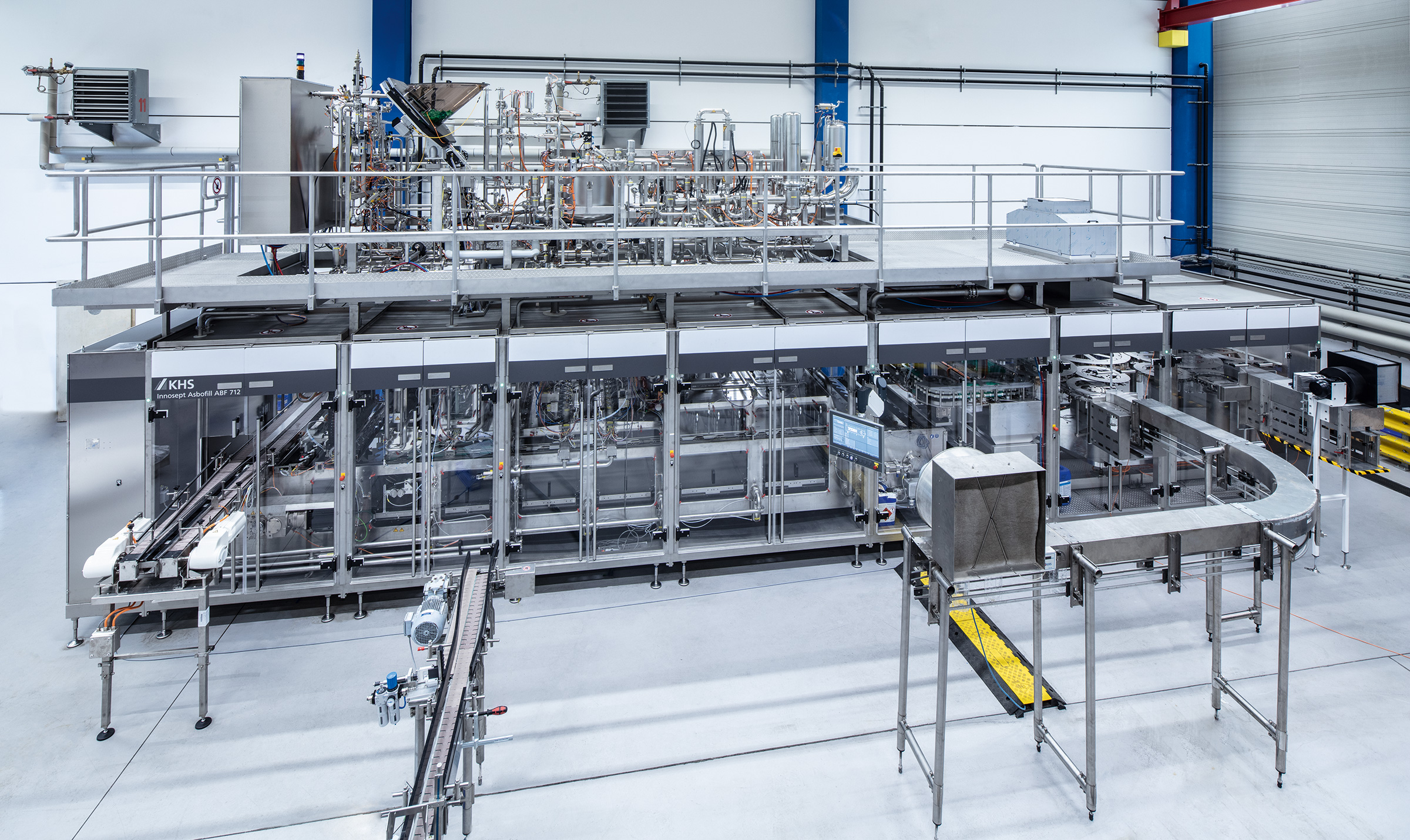
Further reading
Much more
Numerous innovations make for efficient, flexible and safe filling of sensitive beverages – such as the InnoPET BloFill ACF-L, for example.
Learn moreConvincing
- Innovative heating, cooling and air management systems built on over 40 years of experience in stretch blow molding technology
- Aseptic new developments based on technology proven in practice for over 25 years
- Precise sterilization of bottles and closures with H2O2 aerosol
- Fast format changeovers under aseptic conditions for high line availability
Sustainable
- Innovative, holistic concepts for a long-term reduction in the carbon footprint left by the production process
- Profit long term from low operating costs while enjoying a high level of production reliability
Options
-
Application of nitrogen to stabilize plastic bottles
Brief description: The unit doses liquid nitrogen after filling.
Characteristics: This process allows the bottle weight to be reduced compared to a bottle without internal pressure and the product shelf life is lengthened.
-
Servo capper
Brief description: On the servo capper each capping element is controlled by a vertical/rotary servomotor. This enables all relevant capping process parameters for each bottle to be processed to be electronically monitored and controlled in real time.
Characteristics: At the end of the capping process the process parameters are evaluated and documented and any incorrectly capped bottles marked for rejection.
-
Production data acquisition
Brief description: Hardware and software are added to the production data acquisition (PDA) system to allow media values to be measured and recorded.
Characteristics: The following media values are acquired and logged by the PDA system:
- CIP media (pressure, conductivity, flow rate)
- Compressed air (consumption)
- Steam (consumption)
- Water (consumption)
- H2O2 (consumption)
- Electricity (consumption)